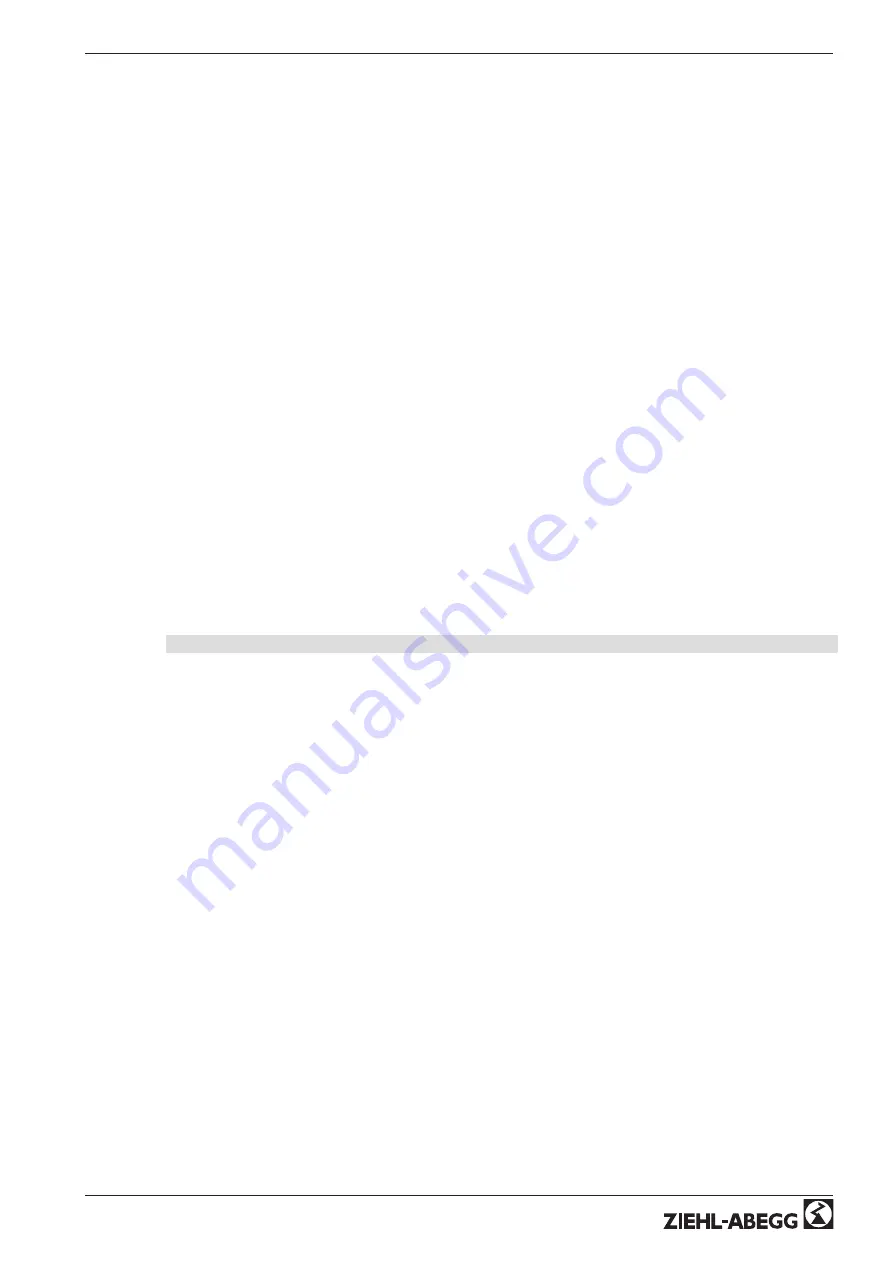
10.1 Special features for measurements at the EC-Controller and motor
10.1.1
Measuring arrangement
Pulse-width-modulated voltages can cause malfunctions and measurement errors by capacitive
unbalances.Such types of errors can be avoided, or at least be considerably reduced, if a number of
basic rules are observed:
1. Spatial separation of control cables from motor current and lines cables.
2. Spatial separation of line and motor cables.
3. Screening of the control cables.
4. Screening of the motor cables.
5. Use only screening measuring cables with the probe. Do not con
gure these parallel to motor
cables
10.1.2
Voltage measurements
Voltage measurements can be made without restrictions only on the the mains side of the frequency
inverter or EC controller.
Due to the content of the harmonic frequencies, on the motor side meaningful measurements are only
possible when using measuring equipment that is capable of measuring the fundamental voltage.
10.1.3
Current measurements
Current measurements can be made without restrictions only on the motor side of the frequency
inverter or EC controller.
Line side measurements of the current may only be performed using true r.m.s. measuring equipment.
The line current cannot be measured with suf
cient accuracy using customary measuring equipment
(for sinusoidal currents of corrected arithmetic mean).
10.1.4Checking the motor magnets
The motor magnets can be tested on-site.
With the incoming line disconnected from the terminals, the motor is rotated manually with the
ywheel. An alternating voltage is measured on terminals U1, V1 proportionate to the rotational
speed.
If the motor magnets are intact, the ratio: speed / rated speed = measured voltage / rated voltage.
If the motor is designed for a 400 V power supply, for example, at n = 2.000 min
-1
, then about 20 V will
be induced at 100 min
-1
.
10.1.5
Checking synchronisation
For an incorrectly connected motor feeder cable U, V, W, or the position sensors H1, H2, H3, the
motor will run either
“
intermittently
”
or not at all because H1, H2, H3 are not in synchronisation with U,
V, W.
The connections and terminal designations should be carefully checked if these symptoms
occur.
Synchronisation can be established by exchanging H1
↔
H2 and further by H2
↔
H3 etc. if necessary
(there is a total of six possibilities!).
The drive must be absolutely circular and vibration-free.
For correct synchronisation, the motor current is almost proportional to the given motor torque. I.e. for
applications where the load characteristic is square-wave (e.g. fans and pumps). approx. 1/4 of the
nominal current is still
owing at half the designed speed. The current
owing is already considerably
higher at lower rotational speeds in the case of an incorrect connection.
Operating Instruction
Econtrol
–
model series EXDM
Diagnostics menu
L-BAL-E008-GB 0945 Index 005
Part.-No. 00156742-GB
74/85