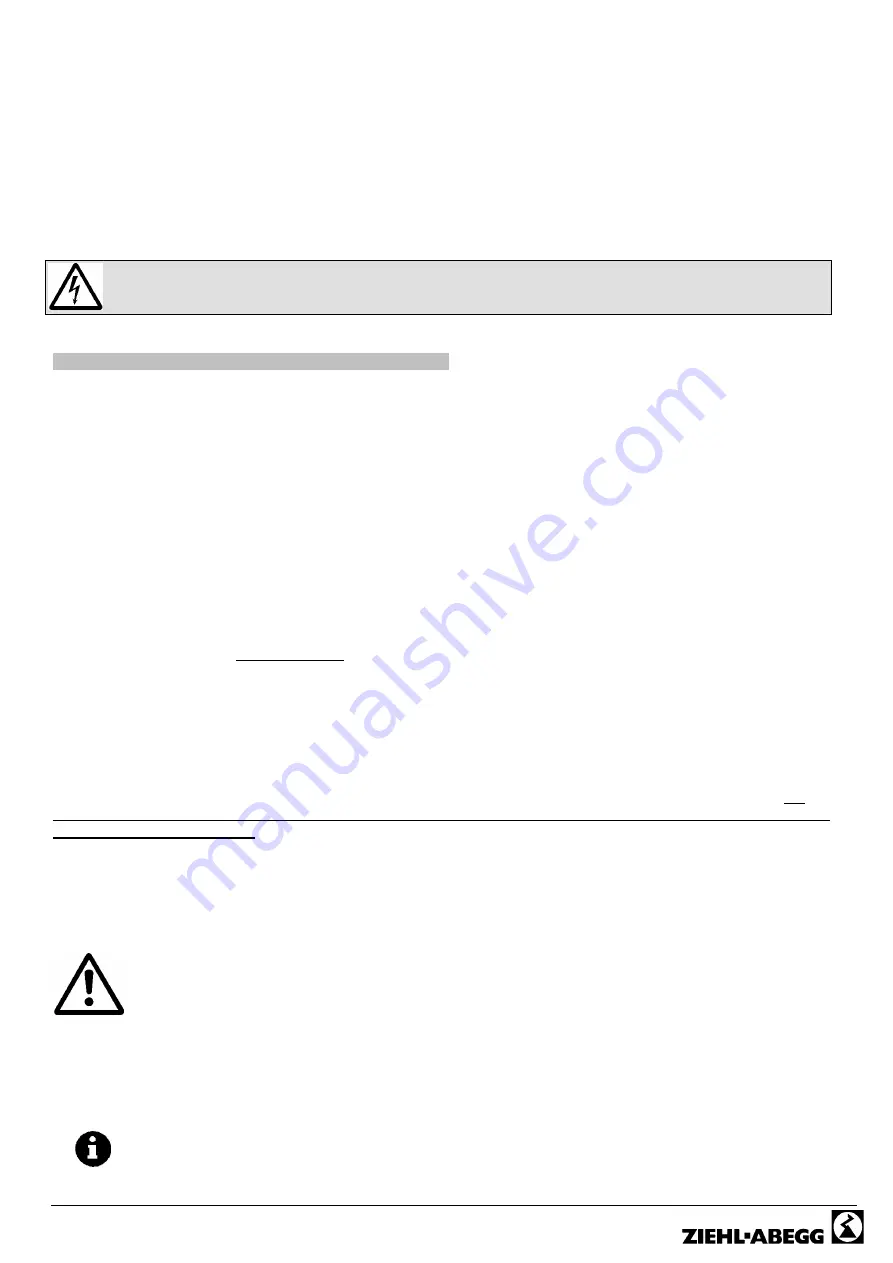
Operating instructions
Dcontrol
Date 0730
TBL02_54-GB 0730
Part-No. 00153238-GB
Page 9 / 28
5. Electrical connections
5.1 Mains connection
Power from the mains is connected to terminals: PE, L1, L2, L3, and N. Here, it must be strictly observed that the mains
voltage lies within the allowable tolerance specifications (
)
General description: Technical data and nameplate affixed
to the side).
The neutral conductor connection “N” is only for the leakage current´s reduction. It is of no significance for the function of
the device. The connection is not applicable for power supply networks without a neutral conductor. Since higher
leakage currents may arise by this across the protective-cable connection “PE”, unwanted triggering by mistake may
occur in systems with FI protection circuits.
If the neutral conductor “N“ is not connected and the “PE“ connection is interrupted, touching can
result in dangerously high leakage currents. In this case, EN 50178 Section 5.3.2.1 for devices with
leakage current above 3.5 mA must be observed.
(Employment in the IT network
)
4.8)
The supply voltage has to correspond to DIN EN 50160!
5.2 Adjustment to specific mains conditions
♦
Fixed 60 Hz assignment
Upon connection, the mains frequency (50 or 60 Hz) is automatically detected and used to trigger ignition of the
thyristors. If, in exceptional cases, a 60 Hz mains frequency can not be clearly identified, fixed assignment can be
necessary (mains failure, as device operates at 50 Hz if 60 Hz is not detected).
By dipswitch S1 No. 6
ON (up) = 60 Hz fix
OFF (down) = automatic detection
♦
Deactivating phase monitoring
The device has built in phase monitoring (
)
Faults and troubleshooting: Mains failure). For special applications (e.g.
unstable mains supply, phase position other than 120° on a soft generator or for transformer operation) this can be
disconnected after consultation with Ziehl-Abegg. The motor is thus no longer protected by TWO PHASE
OPERATION (observe Motor protection chapter).
By dipswitch S1 No. 8
ON (up) = phase monitoring activ
OFF (down) = phase monitoring deactivated
5.3 Motor connection
The motor leads are connected to the terminals: PE, U, V, W. Several fans can be connected to the controller-the
maximum total current of all motors (maximum rated current for electronic control of the voltage) must not exceed the
current rating for the controller.
If the maximum control current for the electronic voltage control is not known, then allowance for an increase in the
motor nominal current must be made. Typical is this for 2- and 4-pole motors at approx. 25 %, for 6-pole motors at
approx. 20 %, for 8- and 10-pole motors at approx. 15 % and higher pole motors at approx. 5 %.
For the control of motors made by other manufacturers (not Ziehl-Abegg), the control characteristics and the
maximum current for electronic regulation of the voltage should be enquired from the manufacturer.
It is recommended that a separate motor protection unit be foreseen for each fan.
For motors with thermistors “TP”:
e.g. type U-EK230E
For motors with thermostats “TB”: e.g. type STDT 16 (E) or AWE-SK
(
)
Enclosure: Circuit suggestion for several motors with motor protection unit
type STDT)
5.3.1 Motor feeder cable
The applicable standard for radiating interference is EN 61000-6-3.
A unshielded motor feeder cable is required for compliance with the standard.