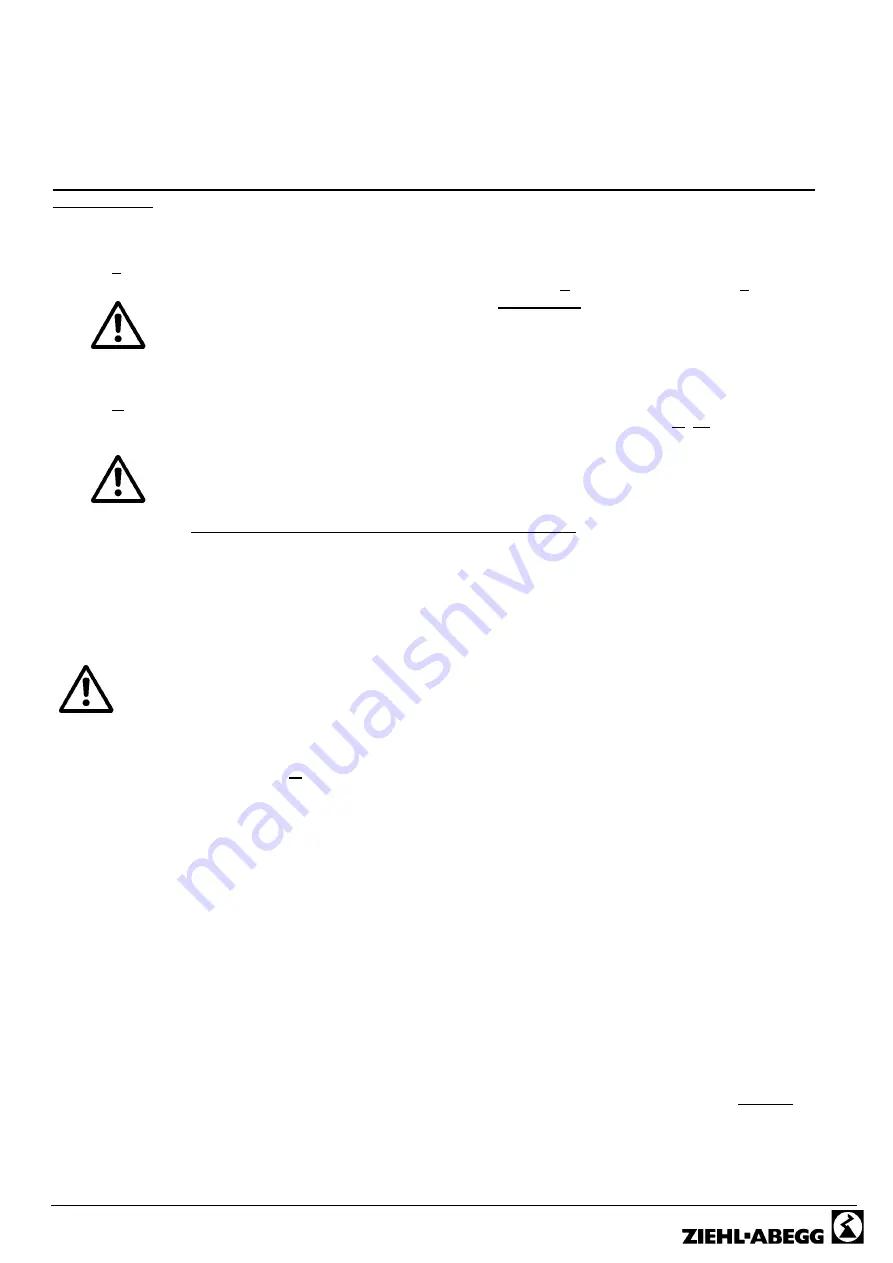
Operating instructions
Dcontrol
Date 0730
TBL02_54-GB 0730
Part-No. 00153238-GB
Page 10 / 28
5.4 Motor noise
Motor noise can occur when fans are controlled using electronic voltage controllers (Phase cutting = series “P...”). Such
noise can be system-dependently perceived as a disturbance. This noise is relatively low for fast-running fans where the
noise from the air is high. The noise from motors in slower-running fans where the noise from the air is less, can be
dominated by resonance in the lower speed ranges.
For systems where noise is critical, we recommend using our
Fcontrol
series frequency converters with integrated
sinusoidal filter
5.5 Motor protection
♦
PKDT5
The motor can be protected by connecting the thermostats “TB” (PKDT: T = motor protection using TB connection).
{
It shall be observed for motors with built-in thermistors “TP” that these cannot be
connected to the “TK” terminals (type PKDT). A separate triggering unit (e.g. type
U-EK230E) is required in this case for the PTC thermistor.
{
When several motors are connected ensure that the thermostats “TB” are always
connected in series.
♦
PKDM5..80
The motor can be protected by connecting the thermostats “TB” or thermistors “TP” (PKDM: M = motor protection
using “TB” or “TP” connection).
{
When several motors are connected ensure that the thermostats “TB” or thermistor
“TP” are always connected in series. A maximum of six individual thermistors (DIN
44081 or DIN 44082) may be connected in series to a single device. Depending on
the motor type, at least two or three individual sensors are built in.
{
Monitoring of motors in “Ex“ zones is not permissible. For systems of this type, an
additional motor protection unit is required, with disconnection via a separate
motor protection circuit.
The unit switches off when a connected thermostat or thermistor has tripped the circuit (interruption between both TK
terminals). The unit then remains switched off. The fault-indicating relay opens (terminals 11-12 bridged) the red LED for
motor fault illuminates, the green LED for operating goes off. The unit starts up again once the drive has cooled down by
switching the mains voltage OFF and then ON again or by enable ON/OFF (terminal “D1”).
{
An outside voltage may never be connected to the terminals “TK”!
{
The internal motor protection does not function if a bypass circuit has been realised.
In this case and as well as other precautions, an additional motor protective device
is necessary.
5.6 Special function only for PKDM..: Motorstart with maximum output voltage „Hard start function “
For types PKDM “Hard start function” can be activated for the connected fans.”Hard start” function means to force the
controller to generate for approx. 10 seconds max. voltage (100%) ignoring any control signal.
Afterwards the output voltage adjusts itself to the given or over the control amplifier calculated value.
For operation as P-controller the „Hard start function“ works also by switching over the control function (“Heating” /
“Cooling”).
By dipswitch S1 No. 5
ON (up) =
with “hard start function”
OFF (down) = no „Hardstart function“
(factory setting)
After switching on of the mains voltage on the output voltage rises during the firmly programmed
run-up time to the given value
5.7 Signal cable (sensor cable)
Pay attention to sufficient distance from powerlines and motor wires
to prevent interferences
.
The control cables may not be longer than 30 m. Screened control cables must be used when the cable length is longer
than 20 m. When using a screened cable, the screen must be connected to the protective conductor at one end, i.e. only
at the control unit (as short and of as low an inductance as possible!).