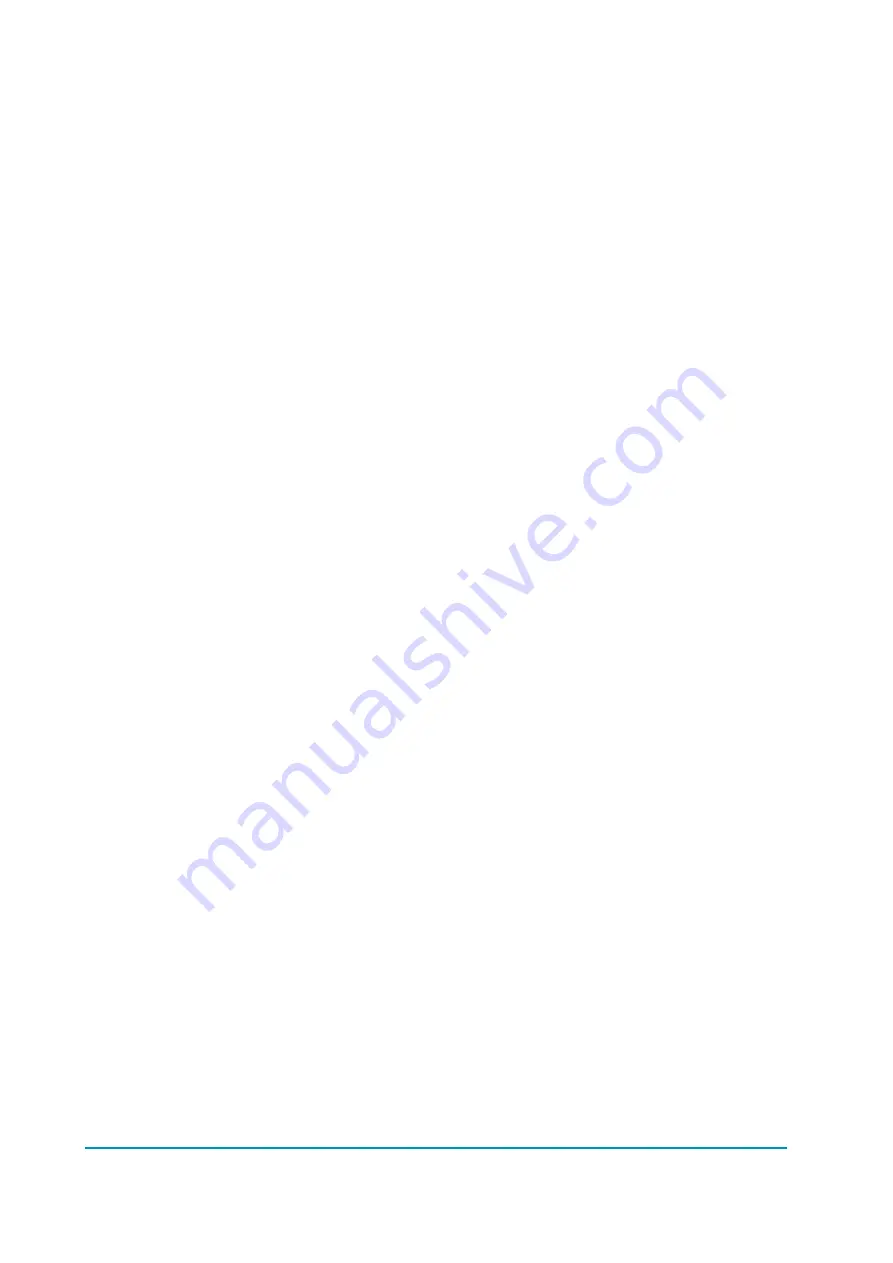
Page - 54/90
AF9ZP0BA - EPS-ACW REACH TRUCK - User Manual
alarm in case it isn’t).
FEEDBACK SECTOR does not change until a complete time sharing cycle
(1st, 2nd and 3rd readings) has been represented on the display.
3) ENC
COUNTING
Counts of the encoder vs. the real straight ahead direction (STEER ANGLE
to 0 deg). At key-on when the straight ahead switch (SW1 to CNA#12)
toggles, an offset (see STEER 0-POS DEG) corresponding to the
displacement between straight ahead switch and actual straight ahead
direction is written on the ENC COUNTING (i.e. ENC COUNTING in general
is not null when the straight ahead switch toggles; ENC COUNTING is
expected to be null when the truck is really driving in the straight ahead
direction instead).
4) ENC
SPEED
Hertz value with 2 decimal digit. This is the speed of the motor measured
with the encoder on the motor shaft.
5) FREQUENCY
Hertz value with 2 decimal digit. This is the frequency applied to the steering
motor.
6) MOTOR
VOLTAGE
It is a percentage. 100% means the sine waves in the motor have the
maximum PWM amplitude.
7) MOTOR
CURRENT
Ampere value. Root Mean Square value of the line current in the motor.
8) IQ
RMS
Ampere value. Root Mean Square value of the quadrature current in the
motor (torque component).
9) ID
RMS
Ampere value. Root Mean Square value of the direct current in the motor
(flux component).
10) TEMPERATURE
Degrees. Temperature of the controller base plate.
11) MOTOR TEMPERATURE
Degrees. Temperature of the motor windings measured with the thermal
sensor inside the motor and connected to CNG#7.
12) PROX SWITCH #1
Provides real time the state of the CW toggle switch (connected to CNA#12).
It is On (active) when CNA#12 is low.
13) PROX SWITCH #2
Provides real time the state of the CCW toggle switch (connected to
CNA#11). It is On (active) when CNA#11 is low.
14) CW LIMIT LEVEL
When the maximum angle limitation via feedback sensors is enabled (see