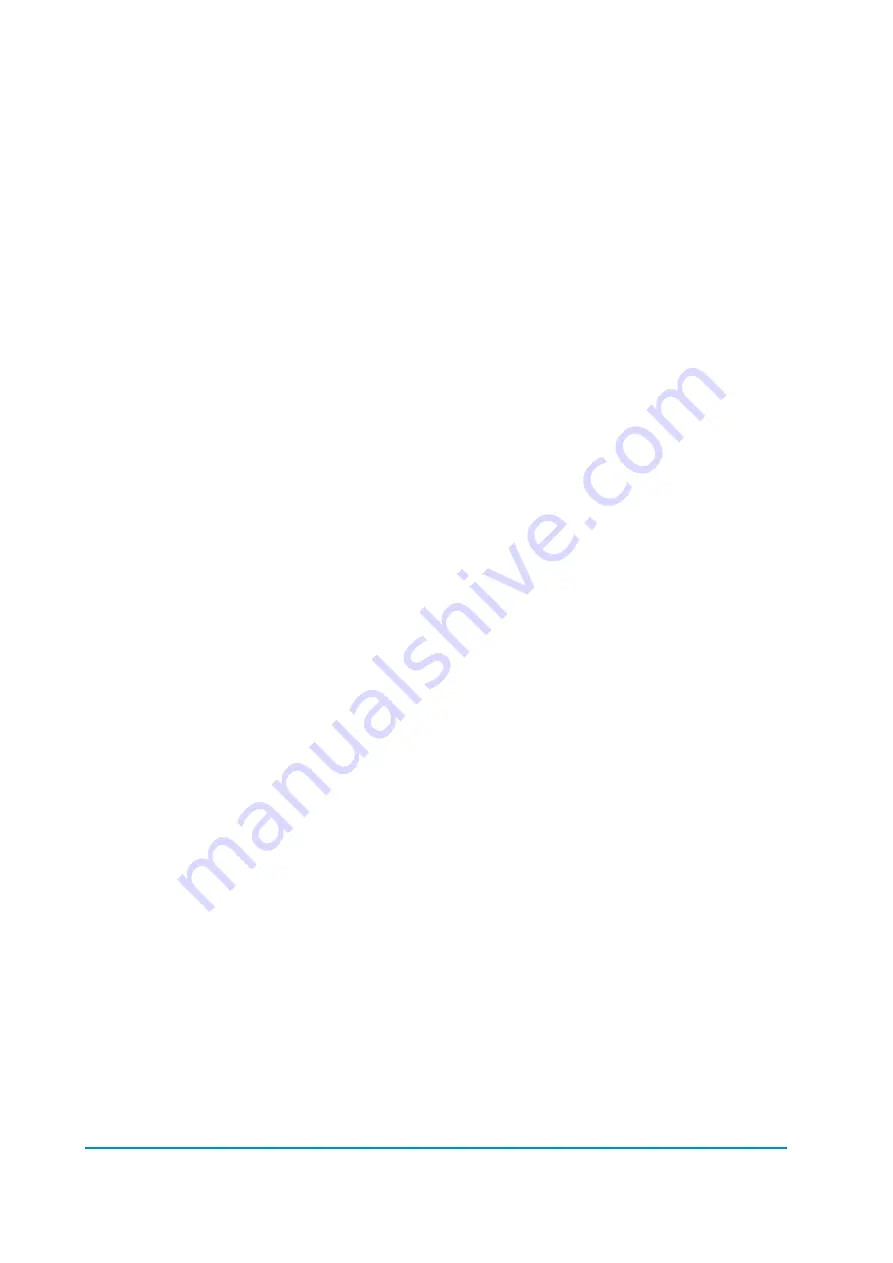
Page - 40/90
AF9ZP0BA - EPS-ACW REACH TRUCK - User Manual
1) ADJUSTMENT
#01
This setting is used to acquire the motor resistance (see 13.3.3.3
ADJUSTMENT #2).
2) SET
CURRENT
This setting is factory adjusted to calibrate the ADJUSTMENT #03 and #04
below.
3) ADJUSTMENT
#02
Motor resistance in milliohms. This is the resistance of the motor measured
between two motor terminals. The motor resistance may be either self-
acquired (Zapi adjusted) or may be set by rolling up or down this adjustment.
4) ADJUSTMENT
#03
(Factory adjusted).
Parameter to
compensate for the gain of the current
amplifier in phase W.
5) ADJUSTMENT
#04
(Factory adjusted). Parameter to
compensate for the gain of the current
amplifier in phase V.
6) SET BATTERY TYPE
Set this adjustment to the nominal battery voltage. Pay attention, never set
SET BATTERY TYPE higher than 36 V for a 24/36 V controller. Never set
SET BATTERY TYPE lower than 36V for a 36/48V controller.
7) STEER 0-POS DEG
Degrees with two decimal digits and sign. This adjustment is used to
compensate the offset between the straight ahead switch and the real
straight ahead direction in the truck. It is set in steps of 0.351 degrees
against the straight ahead switch direction.
Use the 0-POS TEACHING procedure to properly set STEER 0-POS DEG.
8) PULSE IN 180DEG
This adjustment shows the encoder counting corresponding to a half steered
wheel revolution. It is an important setting especially for applications without
steered wheel angle limitation. Procedure for PULSE IN 180DEG consists of
collecting the encoder counting corresponding to a full steered wheel
revolution and then dividing that to a half. To do that two ways are available:
autoteaching (see 12.6), and PULSE IN 180DEG manual setting (see 12.5).
Autoteaching procedure automatically saves the new counting on PULSE IN
180DEG. As an alternative, PULSE IN 180DEG may be also manually written
and saved in EEPROM (see 12.5).
9) PLS IN HALF MOON
This adjustment show the encoder counting corresponding to a partial
steered wheel revolution (about a half) occurring between two falling edges
of the straight ahead sensor: the first falling edge is generated with the
incidence of the first iron plate (cam) limit; the second falling edge is
generated with the incidence of the second iron plate (cam) limit (see Figure
8.5.1-1). It is an important setting for applications without steered wheel
angle limitation. Procedure for PLS IN HALF MOON consists of collecting the
encoder counting corresponding to the angle covered by the half moon cam.
To do that use autoteaching (see 12.6).
Autoteaching procedure automatically saves the new counting on PLS IN