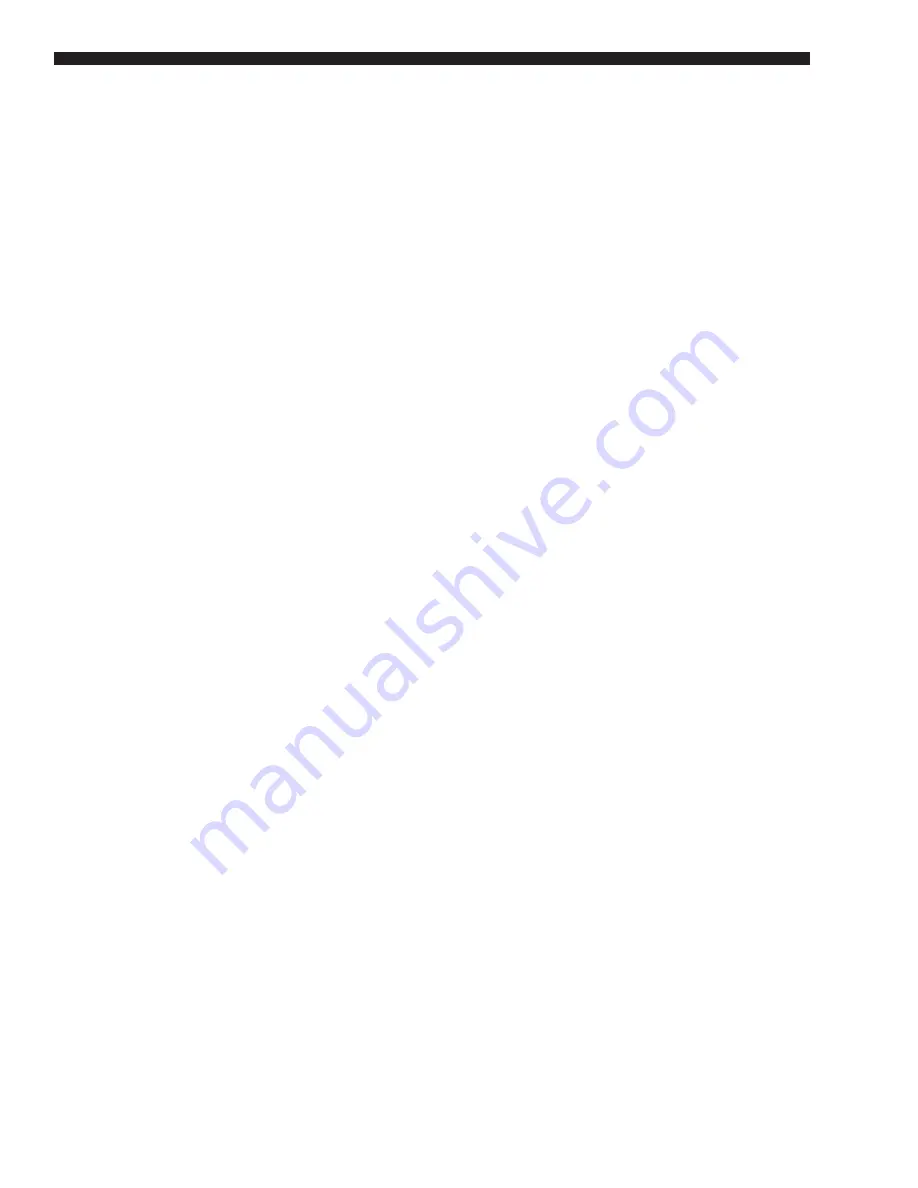
JOHNSON CONTROLS
FORM 150.72-EG6 (516)
56
B. Factory Run Test: Chiller shall be pressure-tested, evacuated and fully charged with re-
frigerant and oil, and shall be factory operational run tested with water flowing through
the vessel.
C. Chiller manufacturer shall have a factory trained and supported service organization.
D. Warranty: Manufacturer shall Warrant all equipment and material of its manufacture
against defects in workmanship and material for a period of eighteen (18) months from
date of shipment or twelve (12) months from date of start-up, whichever occurs first.
1.03 DELIVERY AND HANDLING
A. Unit shall be delivered to job site fully assembled with all interconnecting refrigerant
piping and internal wiring ready for field installation and charged with refrigerant and
oil by the Manufacturer.
B. Provide protective covering over vulnerable components for unit protection during
shipment. Fit nozzles and open ends with plastic enclosures.
C. Unit shall be stored and handled per Manufacturer’s instructions.
PART 2 - PRODUCTS
2.01 CHILLER MATERIALS AND COMPONENTS
A. General: Install and commission, as shown on the schedules and plans, factory as-
sembled, charged, and tested air cooled scroll compressor chiller(s) as specified
herein. Chiller shall be designed, selected, and constructed using a refrigerant with
Flammability rating of “1”, as defined by ANSI/ASHRAE STANDARD 34 Number Des
-
ignation and Safety Classification of Refrigerants. Chiller shall include not less than
two refrigerant circuits above 50 tons (200kW), scroll compressors, direct-expansion
type evaporator, air-cooled condenser, refrigerant, lubrication system, interconnecting
wiring, safety and operating controls including capacity controller, control center, mo-
tor starting components, and special features as specified herein or required for safe,
automatic operation.
B. Cabinet: External structural members shall be constructed of heavy gauge, galvanized
steel coated with baked on powder paint which, when subject to ASTM B117, 1000
hour, 5% salt spray test, yields minimum ASTM 1654 rating of “6”.
C. Operating Characteristics: Provide low and high ambient temperature control options
as required to ensure unit is capable of operation from 30°F to 115°F (-1°C to 46°C)
ambient temperature. [Optional: 0°F to 125°F (-18°C to 52°C) ambient.]
D. Service Isolation valves: Discharge (ball type) isolation valves factory installed per
refrigerant circuit.
E. Includes a system high-pressure relief valve in compliance with ASHRAE15.
F. Pressure Transducers and Readout Capability
1. Discharge Pressure Transducers: Permits unit to sense and display discharge pres-
sure.
2. Suction Pressure Transducers: Permits unit to sense and display suction pressure.
Guide Specifications (Cont'd)
Содержание YLAA
Страница 4: ...JOHNSON CONTROLS FORM 150 72 EG6 516 4 THIS PAGE INTENTIONALLY LEFT BLANK ...
Страница 35: ...FORM 150 72 EG6 516 JOHNSON CONTROLS 35 THIS PAGE INTENTIONALLY LEFT BLANK ...
Страница 48: ...JOHNSON CONTROLS FORM 150 72 EG6 516 48 Wiring Diagram ...
Страница 49: ...FORM 150 72 EG6 516 JOHNSON CONTROLS 49 LD18444 Wiring Diagram Cont d ...