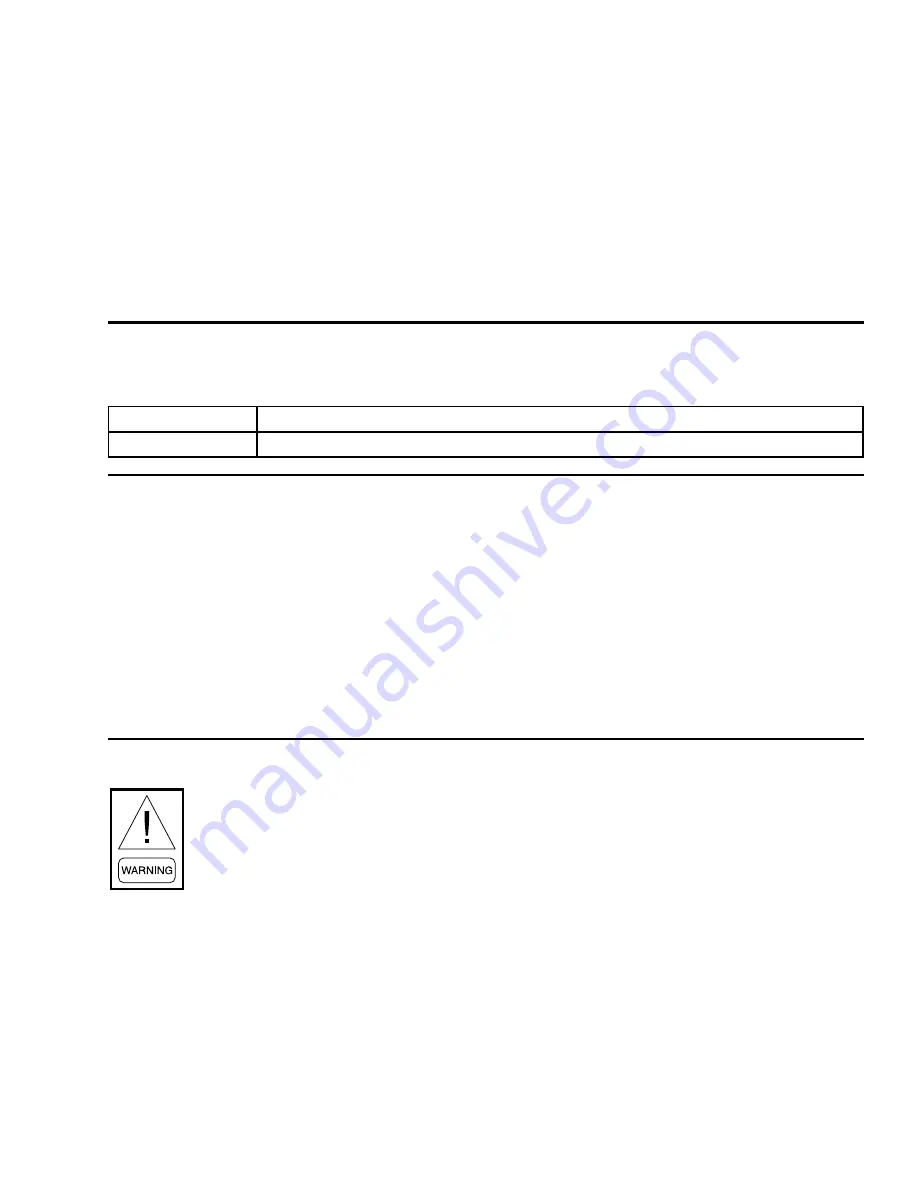
3
JOHNSON CONTROLS
FORM 201.21-NM4 (1020)
CHANGEABILITY OF THIS DOCUMENT
In complying with Johnson Controls’ policy for con-
tinuous product improvement, the information con-
tained in this document is subject to change without
notice. Johnson Controls makes no commitment to
update or provide current information automatically
to the manual or product owner. Updated manuals, if
applicable, can be obtained by contacting the nearest
Johnson Controls Service office or accessing the John-
son Controls Knowledge Exchange website at
https://
docs.johnsoncontrols.com/chillers/
It is the responsibility of rigging, lifting, and operating/
service personnel to verify the applicability of these
documents to the equipment. If there is any question
regarding the applicability of these documents, rig-
ging, lifting, and operating/service personnel should
verify whether the equipment has been modified and
if current literature is available from the owner of the
equipment prior to performing any work on the chiller.
The Control/VSD Cabinet contains lethal High AC and DC voltages. Before performing service inside
the cabinet, remove the AC supply feeding the chiller and verify using a non-contact voltage sensor.
The DC Voltage on the VSD DC Bus will take 5 minutes to bleed off, after AC power is removed.
Always check the DC Bus Voltage with a Voltmeter to assure the capacitor charge has bled off before
working on the system.
• NEVER short out the DC Bus to discharge the filter capacitors.
• NEVER place loose tools, debris, or any objects inside the Control Panel/VSD
Cabinet.
• NEVER allow the Control Panel VSD Cabinet doors to remain open if there is
a potential for rain to enter the panel. Keep doors closed and assure all latches
are engaged on each door unless the unit is being serviced.
• ALWAYS lockout the disconnect supplying AC to the chiller.
• The 1L Line Inductor will reach operating temperatures of over 300° F. DO NOT open panel doors
during operation. Assure the inductor is cool whenever working near the inductor with power off.
WARNING!
It is the responsibility of rigging, lifting, and operating/
service personnel to verify the applicability of these
documents to the equipment. If there is any question
regarding the applicability of these documents, rig-
ging, lifting, and operating/service personnel should
verify whether the equipment has been modified and
if current literature is available from the owner of the
equipment prior to performing any work on the chiller.
CONDITIONED BASED MAINTENANCE
Traditional chiller maintenance is based upon assumed
and generalized conditions. In lieu of the traditional
maintenance program, a Johnson Controls YORK
Conditioned Based Maintenance (CBM) program can
be substituted. This CBM service plan is built around
the specific needs for the chiller, operating conditions,
and annualized impact realized by the chiller. Your lo-
cal Johnson Controls Branch can propose a customized
Planned Service Agreement that leverages real time
and historical data, delivering performance reporting,
corrective actions required and data enabled guidance
for optimal operation and lifecycle assurance. The pro-
gram will include fault detection diagnostics, operation
code statistics, performance based algorithms and ad-
vance rules based rationale delivered by the Johnson
Controls Connected Equipment Portal.
AFFECTED PAGES
DESCRIPTION
3
Conditioned Based Maintenance program information added
REVISION NOTES
Revisions made to this document are indicated in the following table. These revisions are to technical information,
and any other changes in spelling, grammar, or formatting are not included.
Содержание YCAV1039
Страница 43: ...43 JOHNSON CONTROLS FORM 201 21 NM4 1020 43 JOHNSON CONTROLS 6 This page intentionally left blank ...
Страница 55: ...55 JOHNSON CONTROLS FORM 201 21 NM4 1020 55 JOHNSON CONTROLS 6 This page intentionally left blank ...
Страница 67: ...67 JOHNSON CONTROLS FORM 201 21 NM4 1020 67 JOHNSON CONTROLS 6 This page intentionally left blank ...
Страница 83: ...83 JOHNSON CONTROLS FORM 201 21 NM4 1020 83 JOHNSON CONTROLS 6 035 20890 009 REV LOCATION LABEL CON T LD11141 ...
Страница 229: ...229 JOHNSON CONTROLS FORM 201 21 NM4 1020 229 JOHNSON CONTROLS 8 This page intentionally left blank ...
Страница 249: ...249 JOHNSON CONTROLS FORM 201 21 NM4 1020 249 JOHNSON CONTROLS 8 This Page intentionally left blank ...
Страница 277: ...277 JOHNSON CONTROLS FORM 201 21 NM4 1020 277 JOHNSON CONTROLS 8 This page intentionally left blank ...
Страница 308: ...308 JOHNSON CONTROLS FORM 201 21 NM4 1020 308 JOHNSON CONTROLS MAINTENANCE NOTES ...
Страница 309: ...309 JOHNSON CONTROLS FORM 201 21 NM4 1020 309 JOHNSON CONTROLS 9 NOTES ...