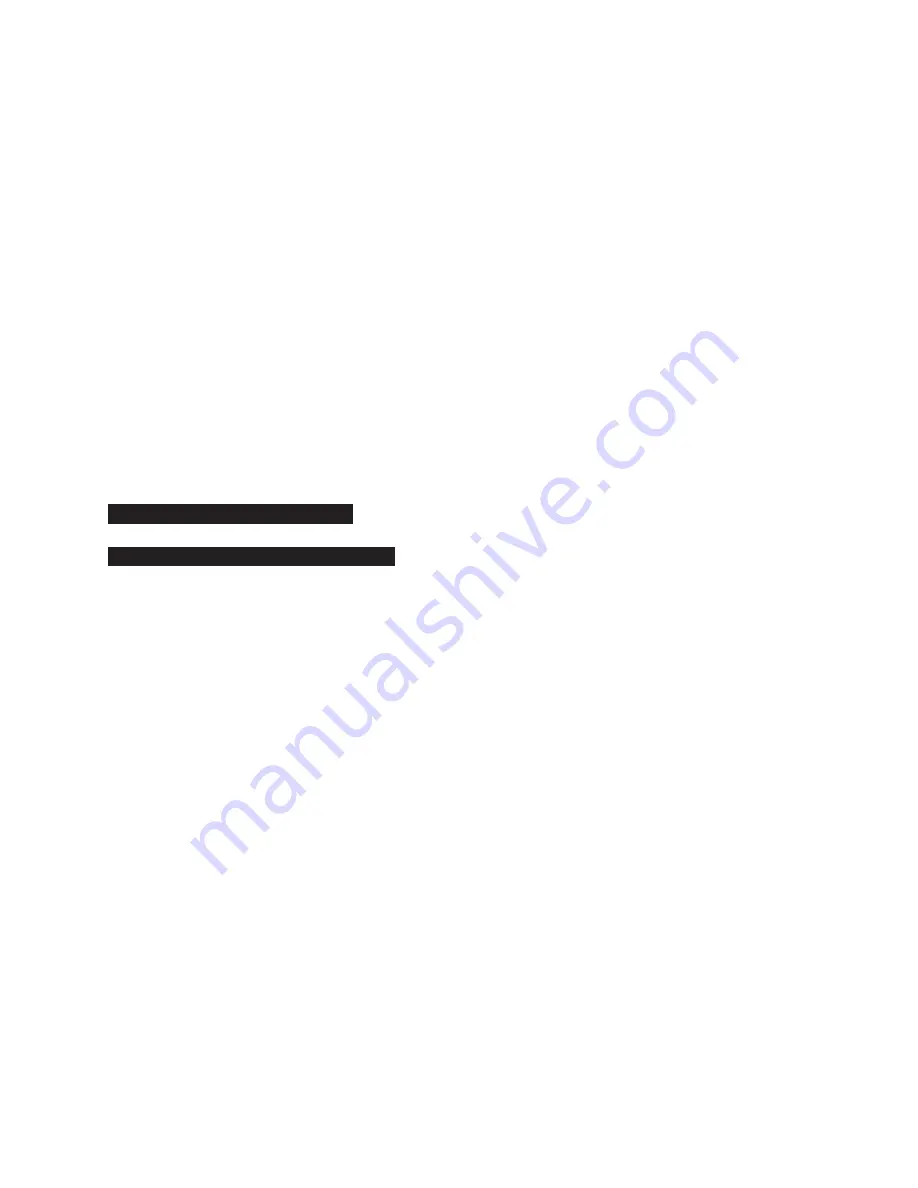
FORM 160.52-O1
41
YORK INTERNATIONAL
On shutdown of the system for any reason, the oil pump
operates and continues to run for 150 seconds. The
system cannot restart during that time interval.
OIL HEATER
During long idle periods, the oil in the compressor oil
reservoir tends to absorb as much refrigerant as it can
hold, depending upon the temperature of the oil and
the pressure in the reservoir. As the oil temperature is
lowered, the amount of refrigerant absorbed will be in-
creased. If the quantity of refrigerant in the oil becomes
excessive, violent oil foaming will result as the pres-
sure within the system is lowered on starting. This foam-
ing is caused by refrigerant boiling out of the oil as the
pressure is lowered. If this foam reaches the oil pump
suction, the bearing oil pressure will fluctuate with pos-
sible temporary loss of lubrication, causing the oil pres-
sure safety cutout to actuate and stop the system. See
Control Center, Section 2.
If the oil temperature falls below 55°F (12.7°C), the dis-
play will read
SYSTEM SHUTDOWN – PRESS STATUS
.
Pressing the
STATUS
key causes the message to read
DAY 10:00 AM – LOW OIL TEMP – AUTO START
. The sys-
tem will be allowed to automatically restart when oil
temperature rises to 30°F (16.7°C) above condenser
temperature.
MOTOR DRIVELINE
The compressor motor is an open-drip-proof, squirrel
cage, induction type constructed to YORK design speci-
fications. 60 hertz motors operate at 3570 rpm. 50 hertz
motors operate at 2975 rpm.
The open motor is provided with a D-flange, cast iron
adapter mounted to the compressor and supported by
a motor support.
Motor drive shaft is directly connected to the compres-
sor shaft with a flexible disc coupling. This coupling
has all metal construction with no wearing parts to as-
sure long life, and no lubrication requirements to pro-
vide low maintenance.
For units utilizing remote electro-mechanical starters,
a terminal box is provided for field connected conduit.
Motor terminals are brought through the motor casing
into the terminal box. Jumpers are furnished for three-
lead type of starting. Motor terminal lugs are not fur-
nished. Overload/overcurrent transformers are fur-
nished with all units. For units furnished with factory
packaged Solid State Starters, (optional) see right.
HEAT EXCHANGERS
Evaporator and condenser shells are fabricated from
rolled carbon steel plates with fusion welded seams.
Heat exchanger tubes are internally enhanced type.
The evaporator is a shell and tube, flooded type heat
exchanger. A distributor trough provides uniform distri-
bution of refrigerant over the entire shell length. Stain-
less steel mesh eliminators or suction baffles are lo-
cated above the tube bundle to prevent liquid refriger-
ant carryover into the compressor. A 2" liquid level sight
glass is located on the side of the shell to aid in deter-
mining proper refrigerant charge. The evaporator shell
contains dual refrigerant relief valves.
The condenser is a shell and tube type, with a discharge
gas baffle to prevent direct high velocity impingement
on the tubes. A separate subcooler is located in the
condenser to enhance performance. Dual refrigerant
relief valves are located on condenser shells with op-
tional isolation refrigerant isolation valves.
The removable compact water boxes are fabricated of
steel. The design working pressure is 150 psig (1034
kPa) and the boxes are tested at 225 psig (1551 kPa).
Integral steel water baffles provide the required pass
arrangements. Stub-out water nozzle connections with
Victaulic grooves are welded to the water boxes. These
nozzle connections are suitable for Victaulic couplings,
welding or flanges, and are capped for shipment.
Plugged 3/4" drain and vent connections are provided
in each water box.
REFRIGERANT FLOW CONTROL
Refrigerant flow to the evaporator is controlled by a
variable orifice.
A level sensor senses the refrigerant level in the con-
denser and outputs an analog voltage to the Micro
Board that represents this level (0% = empty; 100% =
full). Under program control, the Micro Board modu-
lates a variable orifice to control the condenser refrig-
erant level to a programmed setpoint. Other setpoints
affect the control sensitivity and response. These set-
points must be entered at chiller commissioning by a
qualified service technician. Only a qualified service
technician may modify these settings. Manual opera-
tion of the refrigerant level control can be selected. This
allows the prerotation vanes keypad keys to manually
control the variable orifice. This manual control can also
be used to position the variable orifice in a fixed posi-
tion. Instructions for selecting manual level control and
entering the level control setpoints are contained in the
Special Setpoints and Programming Procedures sec-