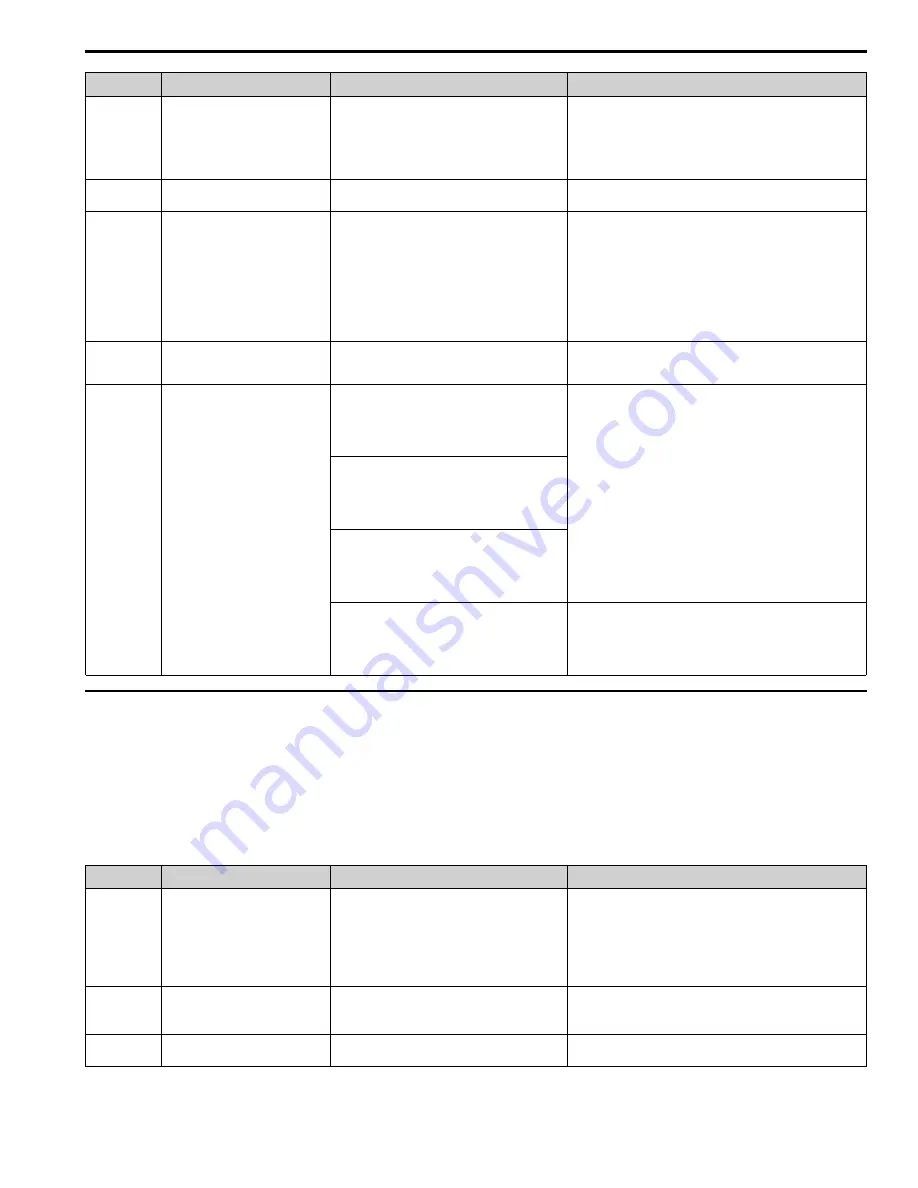
YASKAWA
TOEPC71061782C GA800 Drive Installation & Primary Operation
97
Code
Name
Causes
Possible Solutions
oPE15
Torque Control Setting Error
More than one parameter is selecting torque control at
the same time.
•
d5-01 = 1 [Torque Control Selection = Torque
Control]
•
H1-xx = 71 [MFDI Function Select = Torque
Control]
Correct the parameter settings.
oPE16
Energy Saving Constants Error
The Energy Saving parameters are not set in the
applicable setting range.
Make sure that
E5-xx
is set correctly as specified by the motor
nameplate data.
oPE18
Online Tuning Param Setting Err
The parameters that control online tuning are set
incorrectly. In OLV control, one of these parameters
was set when
n6-01 = 2 [Online Tuning Selection =
Voltage Correction Tuning]
:
•
E2-02 [Motor Rated Slip]
is set to 30% of the
default setting or lower.
•
E2-06 [Motor Leakage Inductance]
is set to 50%
of the default setting or lower.
•
E2-03 = 0 [Motor No-Load Current = 0 A]
has
been set.
Set
E2-02, E2-03, and E2-06
correctly.
oPE20
PG-F3 Setting Error
The value set in
F1-01 [Encoder 1 Pulse Count
(PPR)]
does not agree with the number of encoder
pulses.
•
Examine the
F1-01
value and the number of encoder pulses.
•
Set
F1-01
correctly.
oPE33
Digital Output Selection Error
These two parameters are set at the same time:
•
H2-60 ≠ F [Term M1-M2 Secondary Function ≠
Not Used]
•
H2-01 = 1xx [Term M1-M2 Function Selection =
Inverse output of xx]
These two parameters are set at the same time:
•
H2-63 ≠ F [Term M3-M4 Secondary Function ≠
Not Used]
•
H2-02 = 1xx [Term M3-M4 Function Selection =
Inverse output of xx]
These two parameters are set at the same time:
•
H2-66 ≠ F [Term M5-M6 Secondary Function ≠
Not Used]
•
H2-03 = 1xx [Term M5-M6 Function Selection =
Inverse output of xx]
Clear the
H2-01 to H2-03 = 1xx [Inverse output of xx]
settings.
Note:
It is not possible to set
H2-01 to H2-03 = 1xx [Inverse output of
xx]
when using output functions for logic operations (
H2-60,
H2-63, H2-66 ≠ F
).
These parameter pairs are set incorrectly:
•
H2-21 [Comparator 1 Lower Limit]
>
H2-22
[Comparator 1 Upper Limit]
•
H2-27 [Comparator 2 Lower Limit]
>
H2-28
[Comparator 2 Upper Limit]
•
Set parameters
H2-21
≤
H2-22
.
•
Set parameters
H2-27
≤
H2-28
.
◆
Auto-Tuning Errors
This table gives information about errors detected during Auto-Tuning. If the drive detects an Auto-Tuning error, the
keypad will show the error and the motor will coast to stop. The drive will not send notification signals for faults and
alarms when Auto-Tuning errors occur.
Two types of Auto-Tuning errors are:
Endx
and
Erx
.
Endx
identifies that Auto-Tuning has successfully completed
with calculation errors. Find and repair the cause of the error and do Auto-Tuning again, or set the motor parameters
manually. You can use the drive in the application if you cannot find the cause of the
Endx
error.
Erx
identifies that Auto-Tuning was not successful. Find and repair the cause of the error and do Auto-Tuning again.
Code
Name
Causes
Possible Solutions
End1
Excessive Rated Voltage Setting
The torque reference was more than 20% during
Auto-Tuning or the no-load current that was
measured after Auto-Tuning is more than 80%.
•
Make sure that the input motor nameplate data is correct.
•
Do Auto-Tuning again and correctly set the motor nameplate
data.
•
If you can uncouple the motor and load, remove the motor from
the machine and do Rotational Auto-Tuning again.
•
If you cannot uncouple the motor and load, use the results from
Auto-Tuning.
End2
Iron Core Saturation Coefficient
The motor nameplate data entered during Auto-
Tuning is incorrect.
•
Make sure that the input motor nameplate data is correct.
•
Do Auto-Tuning again and correctly set the motor nameplate
data.
End3
Rated Current Setting Alarm
The rated current value is incorrect.
Do Auto-Tuning again and set the correct rated current shown on the
motor nameplate.