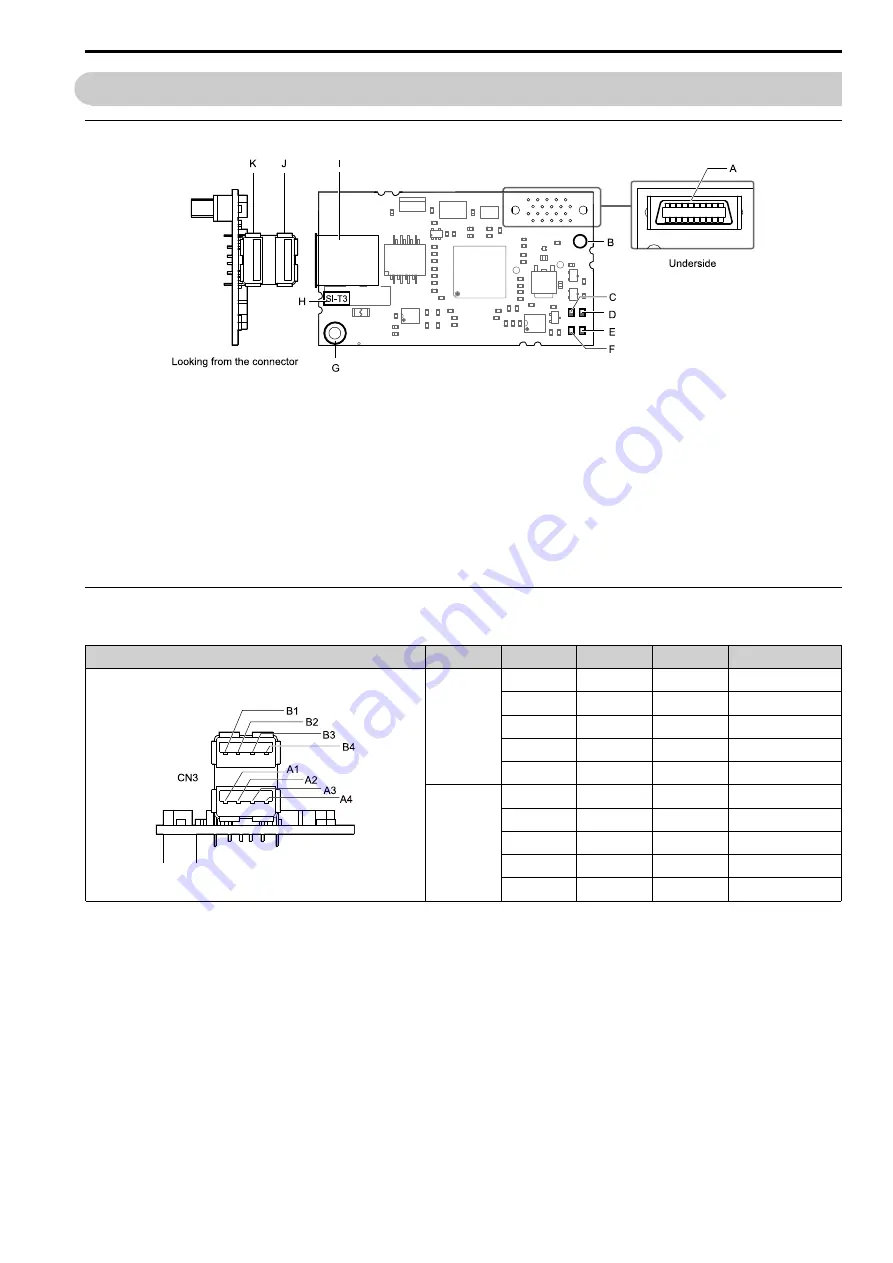
4 Drive Components with Option
YASKAWA
SIEP C730600 86F MECHATROLINK-II Technical Manual
9
4
Drive Components with Option
◆
MECHATROLINK-II Option
A - Connector (CN101)
B - Installation hole
C - LED (ERR)
D - LED (RUN)
E - LED (TX)
F - LED (RX)
G - Ground terminal (FE) (installation
hole)
H - Model
I - Communication connector CN3
J - Connector B
K - Connector A
Figure 4.1 SI-T3 Option Components
*1
Refer to
MECHATROLINK-II Option LED Display on page 10
for details on the LEDs.
*2
Connect the provided ground wire during installation. Installation on GA700, GA800, CR700, and CH700 drives does not require the
ground wire.
◆
Communication connector
Table 4.1 Communication Connector
Connector
Connector
Pin No.
Signal Name
I/O
Function
A
A1
(NC)
-
-
A2
SRD
–
I/O
Send/receive data (
–
)
A3
SRD+
I/O
Send/receive data (+)
A4
(NC)
-
-
Shell
SLD
-
Shield
B
B1
(NC)
-
-
B2
SRD
–
I/O
Send/receive data (
–
)
B3
SRD+
I/O
Send/receive data (+)
B4
(NC)
-
-
Shell
SLD
-
Shield
Note:
Connectors A and B are available for the same functions.