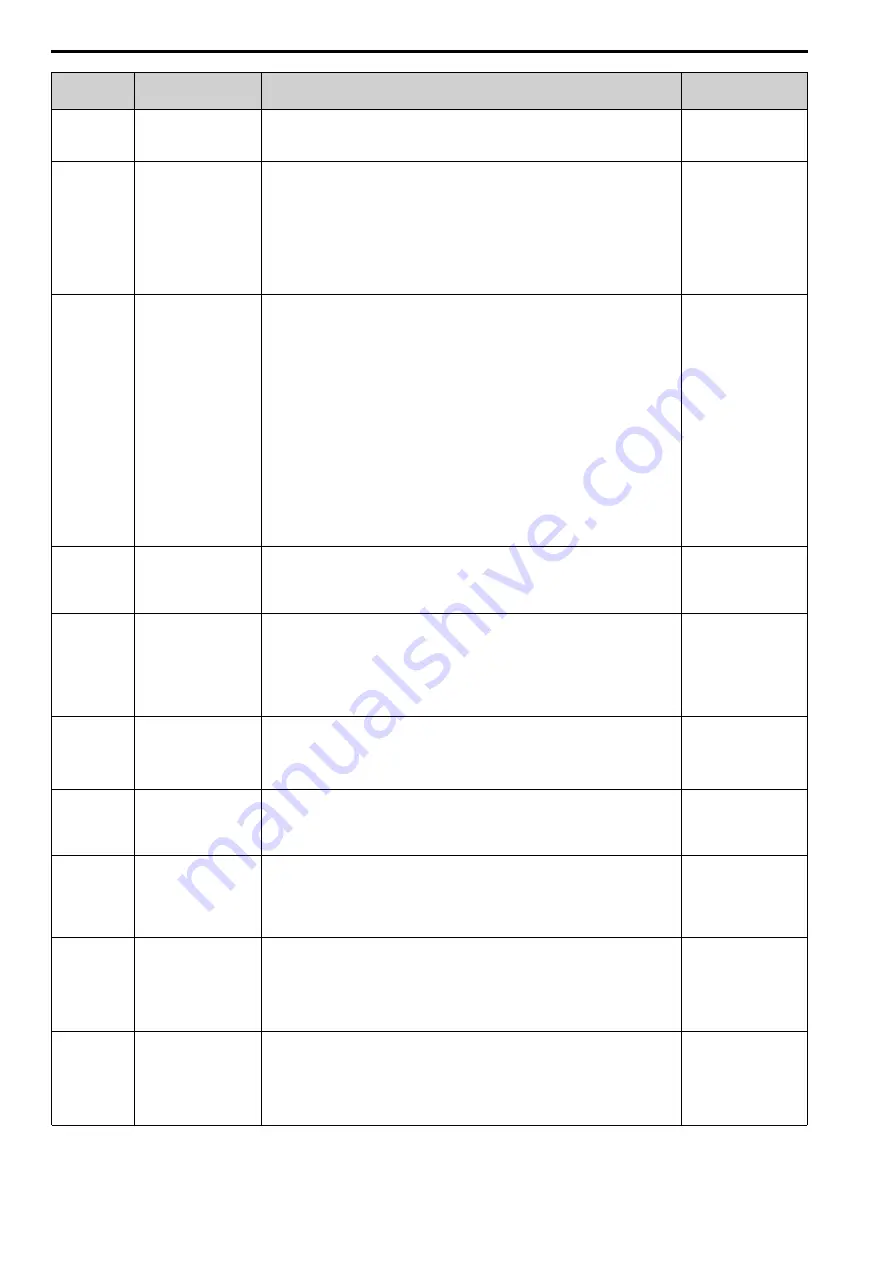
6 MECHATROLINK Option Drive Parameters
20
YASKAWA
SIEP C730600 86F MECHATROLINK-II Technical Manual
No.
(Hex.)
Name
Description
Default
(Range)
F6-02
(03A3)
Comm External Fault
[EF0]
Detect
Selects the condition for external fault detection
[EF0]
.
0 : Always detected
1 : Detection during run only
0
(0, 1)
F6-03
(03A4)
Comm External Fault
[EF0]
Select
Selects drive response when the drive detects an external fault input
[EF0]
during option
communications.
0 : Ramp to Stop
1 : Coast to Stop
2 : Fast Stop (Use C1-09)
3 : Alarm Only
Note:
When you set this parameter to
3
or
4
, the drive will continue operation after it detects a fault.
If you set this parameter to 3 or 4, make sure that you install an emergency stop switch.
1
(0 - 3)
F6-06
(03A7)
Torque Reference/Limit by
Comm
When you enable this parameter, d5-01 determines whether the value is read as the Torque Limit
value (d5-01 = 0) or the Torque Reference value (d5-01 = 1).
0 : Disabled
1 : Enabled
Note:
•
Control method availability of this parameter is different for different product series.
–
1000-Series Drives:
Parameter is available in CLV, AOLV/PM, and CLV/PM. In AOLV/PM, this value is read
as the Torque Limit.
In AOLV/PM, this value is read as the Torque Limit.
–
GA500 Drive:
Parameter is available in OLV, AOLV/PM, and EZOLV. This value is read as the Torque
Limit.
–
GA700, GA800 Drives:
Parameter is available in OLV, CLV, AOLV, AOLV/PM, CLV/PM, and EZOLV.
In OLV and EZOLV, this value is read as the Torque Limit.
–
CR700, CH700 Drives:
Parameter is available in OLV, CLV, and AOLV. This value is read as the Torque Limit.
•
The setting specifies that network communications provide the torque reference or torque
limit. If the PLC does not supply a torque reference or torque limit, the motor cannot rotate.
0
(0, 1)
F6-07
(03A8)
MultiStep Ref Priority
Select
0 : MultiStep References Disabled
1 : MultiStep References Enabled
Note:
Default setting is
1
for GA500.
0
(0, 1)
F6-08
(036A)
Comm Parameter Reset
@Initialize
Selects whether communication-related parameters
F6-xx
and
F7-xx
are set back to original
default values when you use parameter
A1-03
to initialize the drive.
0 : No Reset - Parameters retained
1 : Reset - Back to factory default
Note:
The drive will not change this setting value when you set
F6-08 = 1
and use
A1-03
to
initialize the drive.
0
(0, 1)
F6-20
(036B)
MECHATROLINK Station
Address
Sets the station number
Note:
•
Cycle power for setting changes to take effect.
•
All station addresses must be unique. If set to 20 or 3F, a Station Address Error
[AEr]
will
occur and the ERR light will turn on.
21 (Hex.)
(20 - 3F (Hex.))
F6-21
(036C)
MECHATROLINK Frame
Size
0 : 32-byte
1 : 17-byte
Note:
Cycle power for setting changes to take effect.
0
(0, 1)
F6-22
(036D)
MECHATROLINK Link
Speed
Sets the communications speed for MECHATROLINK-II.
0 : 10 Mbps
1 : 4 Mbps
Note:
Cycle power for setting changes to take effect.
0
(0, 1)
F6-23
(036E)
MECHATROLINK
Monitor Select (E)
Set MEMOBUS/Modbus register to monitor SEL_MON of INV_CTL and INV_I/O.
Note:
•
Cycle power for setting changes to take effect.
•
Set byte 21, SEL_MON1/2 of INV_CTL, or byte 38, SEL_MON 3/4 and byte 39, SEL_
MON 5/6 of INV_I/O to 0E (Hex.) to enable the register set with
F6-23
. Bytes of the
response data enable the register content set with
F6-23
. Refer to the manual packaged with
the drive for more information about registers that you can set.
0 (Hex.)
(0 - FFFF (Hex.))
F6-24
(036F)
MECHATROLINK
Monitor Select (F)
Set MEMOBUS/Modbus register to monitor SEL_MON of INV_CTL and INV_I/O.
Note:
•
Cycle power for setting changes to take effect.
•
Set byte 21, SEL_MON1/2 of INV_CTL, or byte 38, SEL_MON 3/4 and byte 39, SEL_
MON 5/6 of INV_I/O to 0F (Hex.) to enable the register set with
F6-24
. Bytes of the
response data enable the register content set with
F6-24
. Refer to the manual packaged with
the drive for more information about registers that you can set.
0 (Hex.)
(0 - FFFF (Hex.))