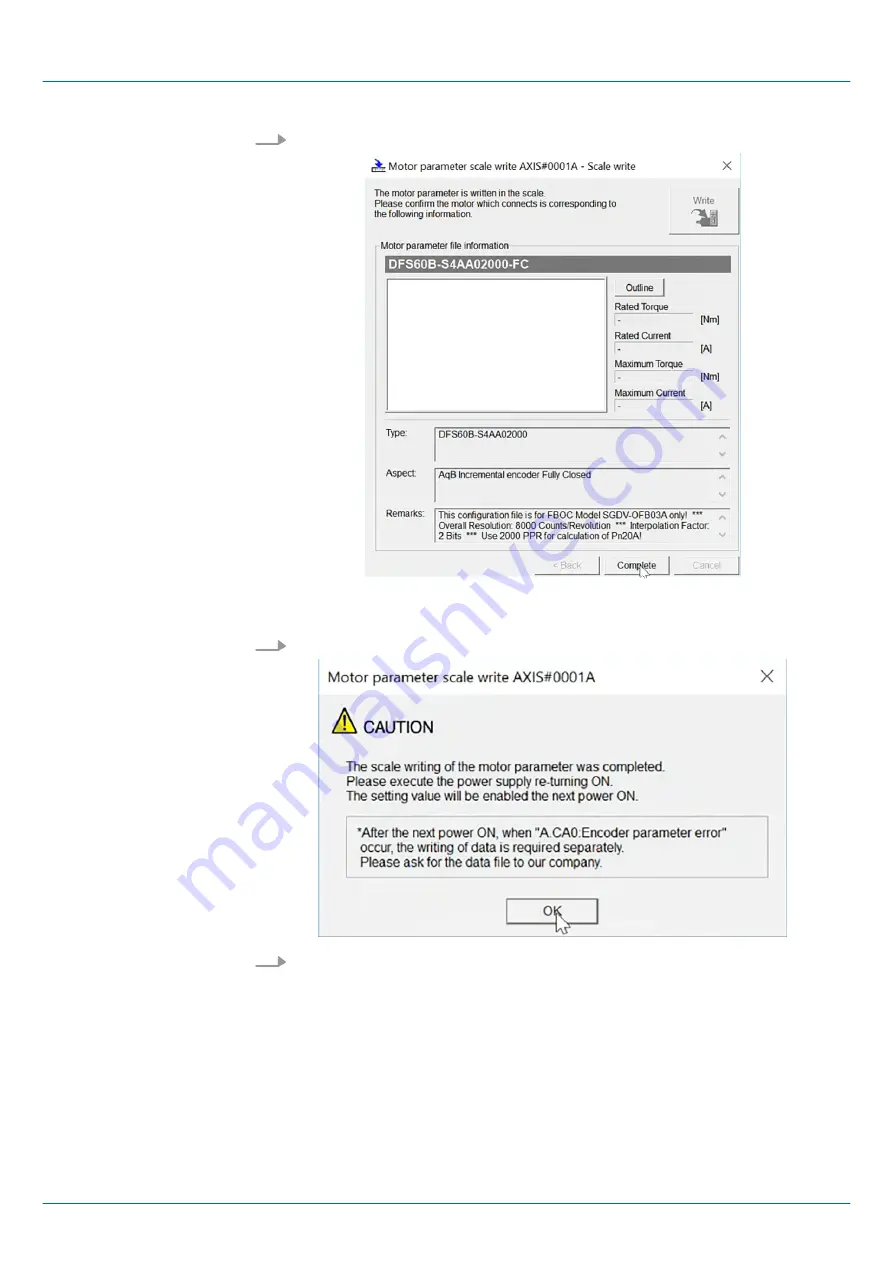
7.
If the motor parameters were transferred successfully, click “Complete”.
ð
If a data transmission error occurred, a message is displayed asking to select
the next step.
8.
Confirm the message box with “OK”.
9.
Then restart the SERVOPACK by switching the control power supply OFF and ON
again.
It is mandatory to search for the SERVOPACK again and to reconnect!
Sigma-5 and Sigma-7 Series SERVOPACKs
Set-up Procedure
Feedback Option Module Set-up
| | Feedback Option Module Type 3 - Manual version C - Revision 0 | en |
67