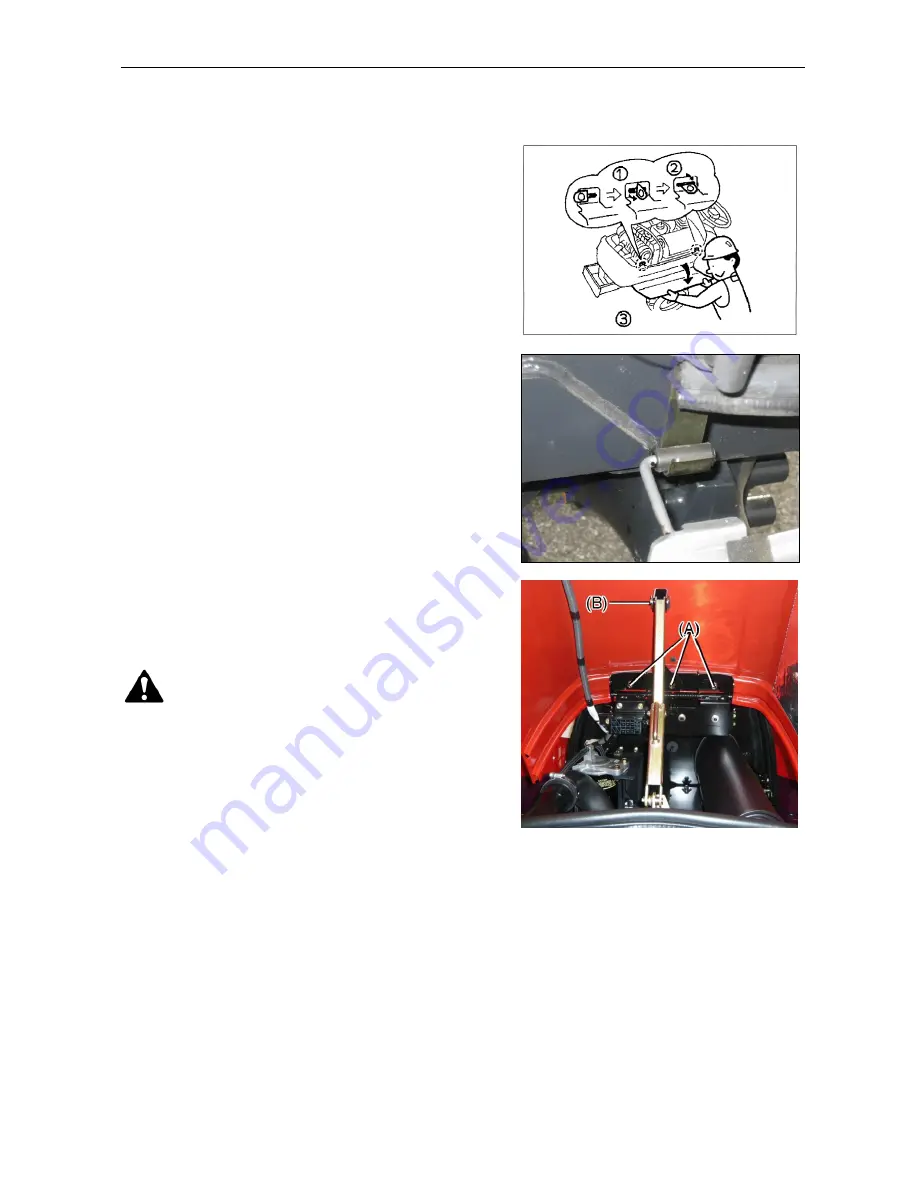
2 DISASSEMBLY OF COMPONENTS
2 DISASSEMBLY OF COMPONENTS
EF494T TM 06/2011 edition
42
2.1
REMOVING THE ENGINE BONNET
COVER
2.1.1
Removing/mounting the side covers
<Removing>
(1) Open the bonnet.
(2) Put the locking knobs in the vertical position
(each forward and rear).
(3) Remove the side covers.
<Mounting>
(1) Clamp the cover lower hooks (x 2).
(2) Fix the cover top with the locking knob.
2.1.2
Removing the engine bonnet cover
Remove the 3 bolts (A) and the pin (B), and remove
the engine bonnet cover.
CAUTION
This work should be done by 2 people. If you work
alone, you may be injured.
Содержание EF-494T
Страница 1: ...EF494T TM 06 2011 edition ...
Страница 30: ...1 PERIODICAL INSPECTION 1 PERIODICAL INSPECTION EF494T TM 06 2011 edition 22 1 PERIODICAL INSPECTION ...
Страница 85: ...3 ENGINE 3 ENGINE EF494T TM 06 2011 edition 77 3 ENGINE ...
Страница 86: ...3 ENGINE 3 ENGINE EF494T TM 06 2011 edition 78 3 1 FUEL SYSTEM 3 1 1 Flow of fuel and layout of components ...
Страница 88: ...3 ENGINE 3 ENGINE EF494T TM 06 2011 edition 80 B Return ...
Страница 126: ...4 CLUTCH 4 CLUTCH EF494T TM 06 2011 edition 118 4 CLUTCH ...
Страница 130: ...4 CLUTCH 4 CLUTCH EF494T TM 06 2011 edition 122 ...
Страница 133: ...5 TRANSMISSION 5 TRANSMISSION EF494T TM 06 2011 edition 125 5 TRANMISSION ...
Страница 136: ...5 TRANSMISSION 5 TRANSMISSION EF494T TM 06 2011 edition 128 5 2 TRANSMISSION SYSTEM CROSS SECTION ...
Страница 158: ...6 REAR AXLE AND BRAKE 6 REAR AXLE AND BRAKE EF494T TM 06 2011 edition 150 6 REAR AXLE AND BRAKE ...
Страница 167: ...7 FRONT AXLE 7 FRONT AXLE EF494T TM 06 2011 edition 159 7 FRONT AXLE ...
Страница 169: ...7 FRONT AXLE 7 FRONT AXLE EF494T TM 06 2011 edition 161 7 2 CROSS SECTION VIEW ...
Страница 176: ...8 POWER STEERING 8 POWER STEERING EF494T TM 06 2011 edition 168 8 POWER STEERING ...
Страница 187: ...9 HYDRAULIC LIFT UNIT 9 HYDRAULIC LIFT UNIT EF494T TM 06 2011 edition 179 9 HYDRAULIC LIFT UNIT ...
Страница 210: ...10 ELECTRIC EQUIPMENT 10 ELECTRIC EQUIPMENT EF494T TM 06 2011 edition 202 10 ELECTRIC EQUIPMENT ...
Страница 214: ...10 ELECTRIC EQUIPMENT 10 ELECTRIC EQUIPMENT EF494T TM 06 2011 edition 206 10 1 2 Circuit diagram Engine start ...
Страница 225: ...10 ELECTRIC EQUIPMENT 10 ELECTRIC EQUIPMENT EF494T TM 06 2011 edition 217 10 3 2 Circuit diagram Alarm ...
Страница 231: ...10 ELECTRIC EQUIPMENT 10 ELECTRIC EQUIPMENT EF494T TM 06 2011 edition 223 10 4 2 Circuit diagram Safety ...
Страница 234: ...11 APPENDIXES 11 APPENDIXES EF494T TM 06 2011 edition 226 11 APPENDIXES ...
Страница 235: ...11 APPENDIXES 11 APPENDIXES EF494T TM 06 2011 edition 227 11 1 HYDRAULIC CIRCUIT DIAGRAM ...
Страница 236: ...228 11 2 ELECTRICAL CIRCUIT DIAGRAM 11 2 1 WIRING HARNESS ...
Страница 238: ...230 11 2 3 ELECTRICAL WIRING DIAGRAM ...
Страница 239: ......