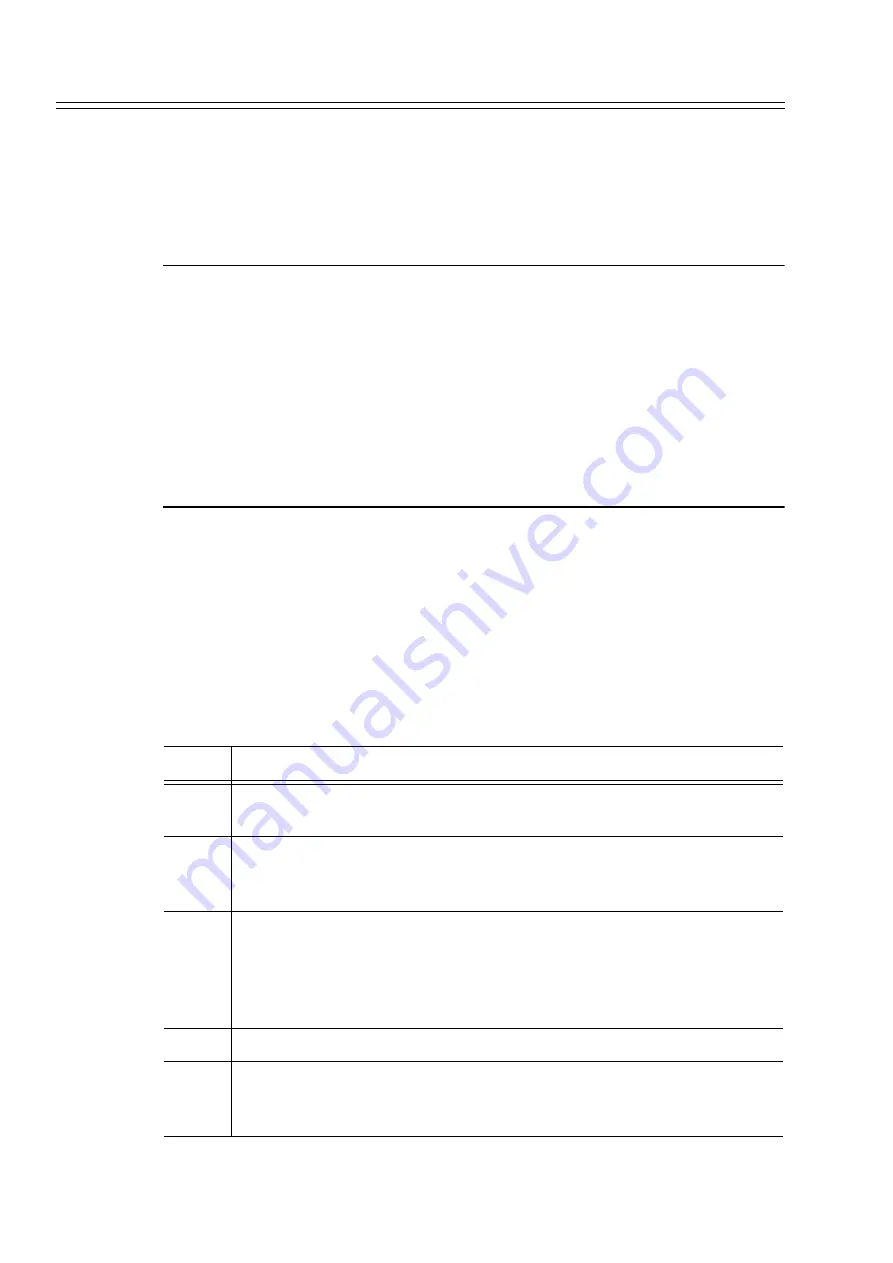
Yamatake Corporation
5-26
ST3000 Smart Transmitter Series 900 Electronic Differential Pressure/Pressure Transmitter
5-3-4 :Liquid Level Measurement of Closed Tank (Wet Leg)
5-3-4-1 Preparation for Measurement
WARNING
• Place the process in manual control mode.
If the process is in automatic control mode, change it to the manual control mode
before performing this work.
• Drain poisonous fluids with care, making provisions for protecting work-
ers.
• Make sure that the differential pressure output valve (main valve), the
drain valve, the gas vent plug (refer to "Figure 4-16 Closed Tank -- Pip-
ing (Wet-leg Sealing Example)".) and the high pressure side and low
pressure side stop valves of the 3-way manifold valve are closed. Also,
make sure that the equalizer valve of the 3-way manifold valve is open.
Calculating setting range
For the procedure for obtaining the setting range by calculation, refer to "5-10 : Set
Range Calculation for Liquid Level Measurement".
Procedure
Perform zero-point adjustment and introduce process pressure into the transmitter
using this procedure:
Zero-point calibration
Step
Description
1
Feed sealing liquid from the seal pot to fill the connecting pipe with seal-
ing liquid.
2
Gradually open the stop valves of both the high-pressure side and the low-
pressure side, and the drain plugs, to fill the pressure receiving part of the
transmitter with sealing liquid.
3
When sealing liquid flows out from the drain plugs, close the stop valves
of both the high pressure side and the low pressure side and the drain
plugs.
In this state, the same pressure is applied to the high pressure side and the
low pressure side of the transmitter (equal pressure state).
4
Referring to procedure 2 in page 5-10, perform zero point calibration.
5
After completing zero-point calibration, close the equalizer valve. Open
the stop valve and the drain plug of the low-pressure side to drain sealing
liquid. Close the stop valve and the drain plug of the low-pressure side.