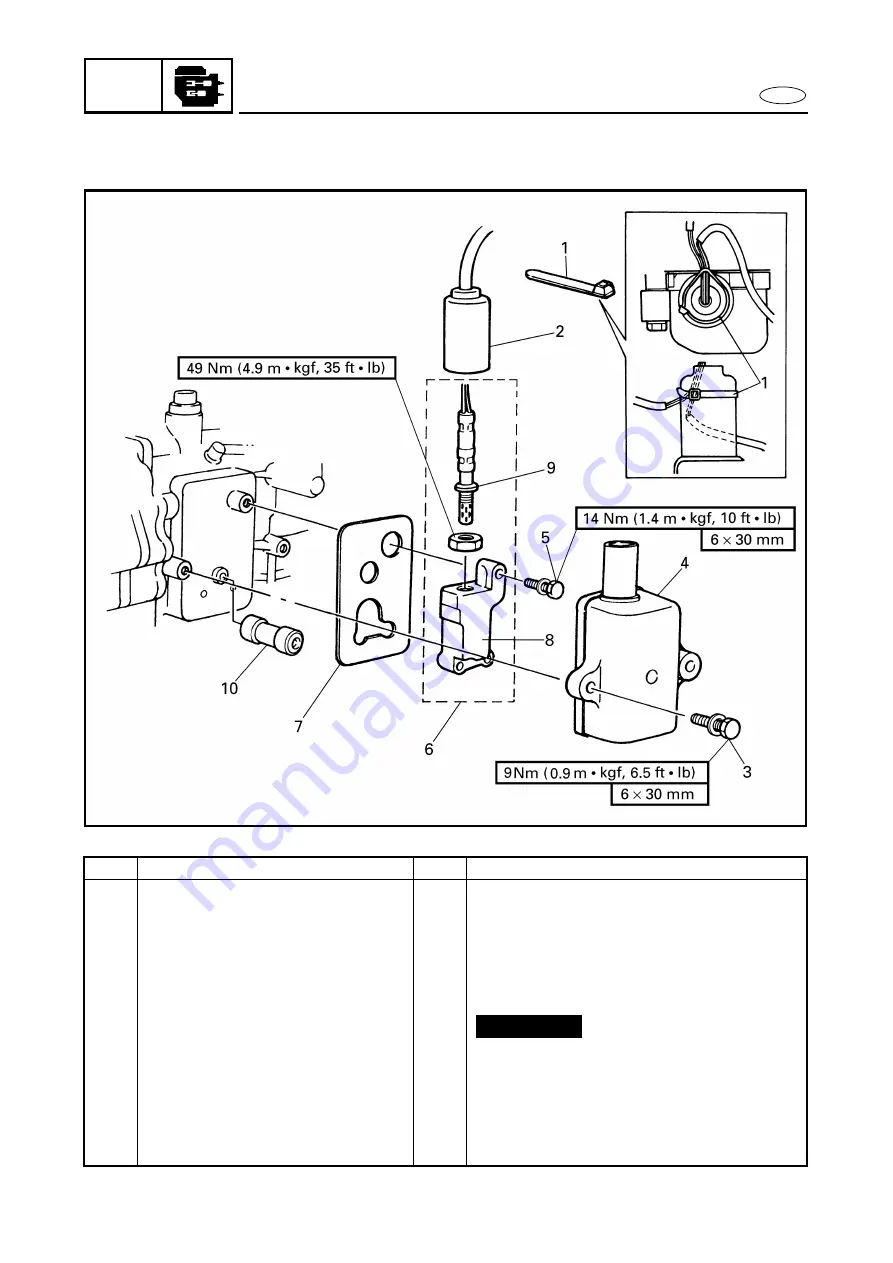
5-25
POWR
E
OXYGEN DENSITY SENSOR
OXYGEN DENSITY SENSOR
5
REMOVING/INSTALLING THE OXYGEN DENSITY SENSOR
5
Order
Job/Part
Q’ty
Remarks
1
Plastic locking tie
1
2
Rubber cap
1
3
Bolt
2
(with washer)
4
Oxygen density sensor cover
1
5
Bolt
3
(with washer)
6
Oxygen density sensor assembly
1
7
Gasket
1
8
Oxygen density sensor bracket
1
9
Oxygen density sensor
1
Refer to “INSPECTING THE OXYGEN
DENSITY SENSOR” on page 8-22.
10
Oxygen density sensor joint
1
For installation, reverse the removal
procedure.
5200
Not reusable
Содержание SX150C
Страница 1: ...SX150C VX150C DX150C SX200C SERVICE MANUAL 67H 28197 1F 11 LIT 18616 02 80 LIT186160280...
Страница 52: ...3 19 E INSP ADJ GENERAL LUBRICATION POINTS 3 Apply Water resistant grease 3290 3300 3310 3320 3330...
Страница 61: ...4 7 FUEL E FUEL INJECTORS INSPECTING THE FILTERS Check Filter Damage tears Replace Contaminants Clean 4040...
Страница 329: ...YAMAHA MOTOR CORPORATION USA Printed in USA Jan 2004 0 0 1 CR E...