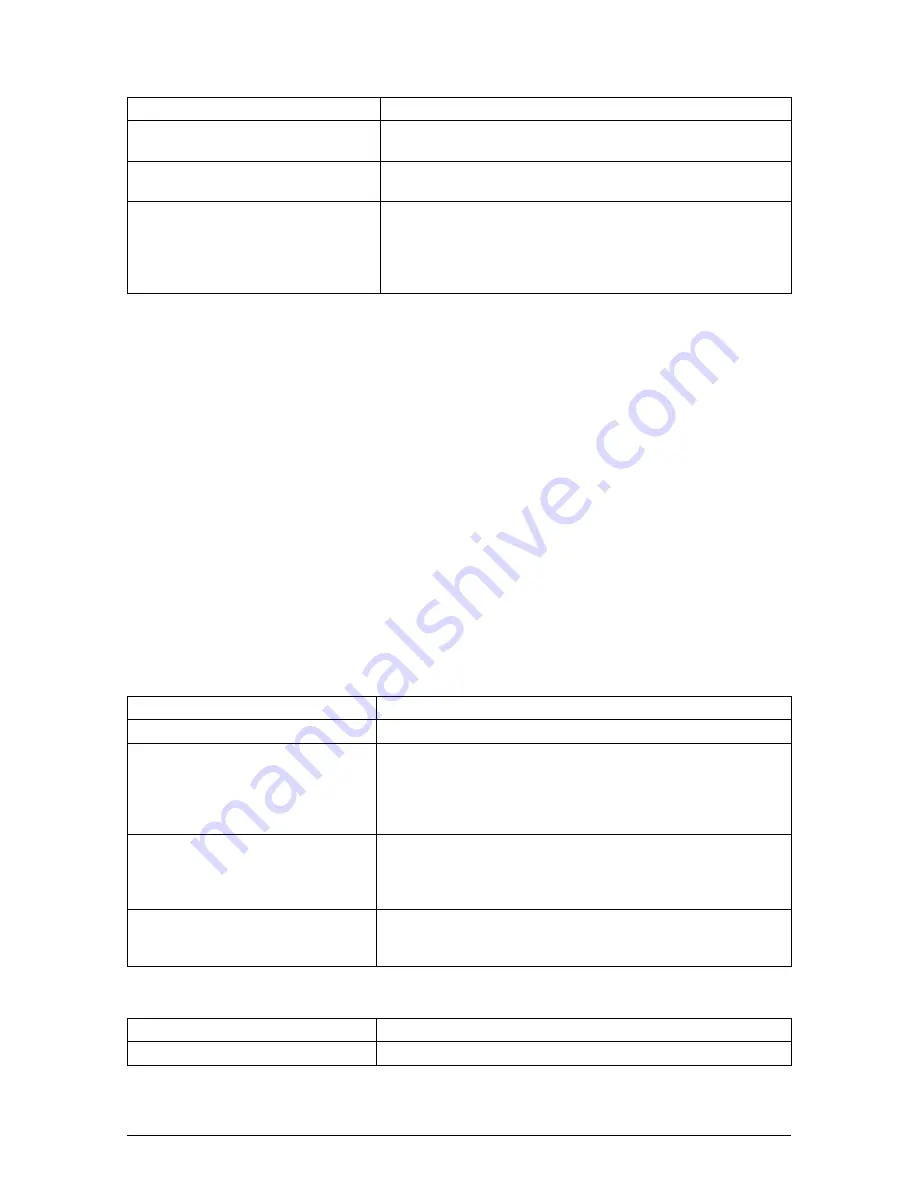
28
XYZ Machine Tools Ltd
XYZ Bed Mill Safety, Installation, Maintenance, Service & Parts List Manual
Possible Cause
Check This
Machine Tool & Setup problem
Check for any looseness in the setup (Tool, Tool holder, Part,
Vice, or Fixture). See Machine Tool & Setup Section 4.1
X, Y, and Z-axis Gibs are loose
Check the adjustment of the X, Y, and Z-axis Gibs using the X,
Y, and Z-axis Gib adjustment procedures. See Section 5.2.1
X and Y-axis Drive Trains are loose
Check Repeatability using the Repeatability and Positional
Accuracy procedure. Step by step, carefully inspect the Drive
Train for any looseness. It may be necessary to disassemble
and then reassemble the Drive Train. See Mechanical Drive
Train (X, Y) Section 4.2
3.1.4
Parts Have Incorrect Dimensions
Parts are being machined with dimensions that are different than those programmed. Typical accuracy
expectations should be:
Circles: 0.05 mm TIR over 75 mm DIA
Positional Accuracy: 0.01 mm
Repeatability: 0.01 mm
Note: The typical slideway-milling machine is not capable of achieving more precise results.
The system should be expected to repeat within the resolution of the displayed DRO numbers of 0.01
mm.
Do the following Service Code:
Code 33 Software Identification. This is needed if you call Customer Service
Code 123 Calibration
Code 11 Measure's the backlash in the system. Only used on machines with Dual Feedback
systems
Code 12 Feed Forward Constant
Code 127 Measure's the backlash in the system. Only used on machines with no Dual Feedback
Code 128 Enter backlash compensation
3.1.4.1
Every Part Has the Same Error
Possible Cause
Check This
Machine Tool & Setup problem
See Machine Tool & Setup Section 4.1
Programming Error
In the program, look for common errors in programming such
as transposing numbers, tool diameters, and pressing INC SET
when ABS SET is meant. This is especially suspected if the
dimensional errors are larger than a few thousandths. See the
Controls Programming, Operations and Care manual.
Configuration file that contains
calibration file and backlash
constants has been erased or
corrupted.
Verify configuration file (Code 313) does not read default
values. Load saved configuration file from floppy disk in
electrics cabinet with Code 141.
Calibration or Backlash problem
Recalibrate the machine. Reset the Backlash. Check
Repeatability and Positional Accuracy. See Calibration &
Backlash Constants
3.1.4.2
The Dimensional Errors Are Random or Accumulate in Size Over the Part Program
Run
Possible Cause
Check This
Machine Tool & Setup problem
See Machine Tool & Setup Section 4.1