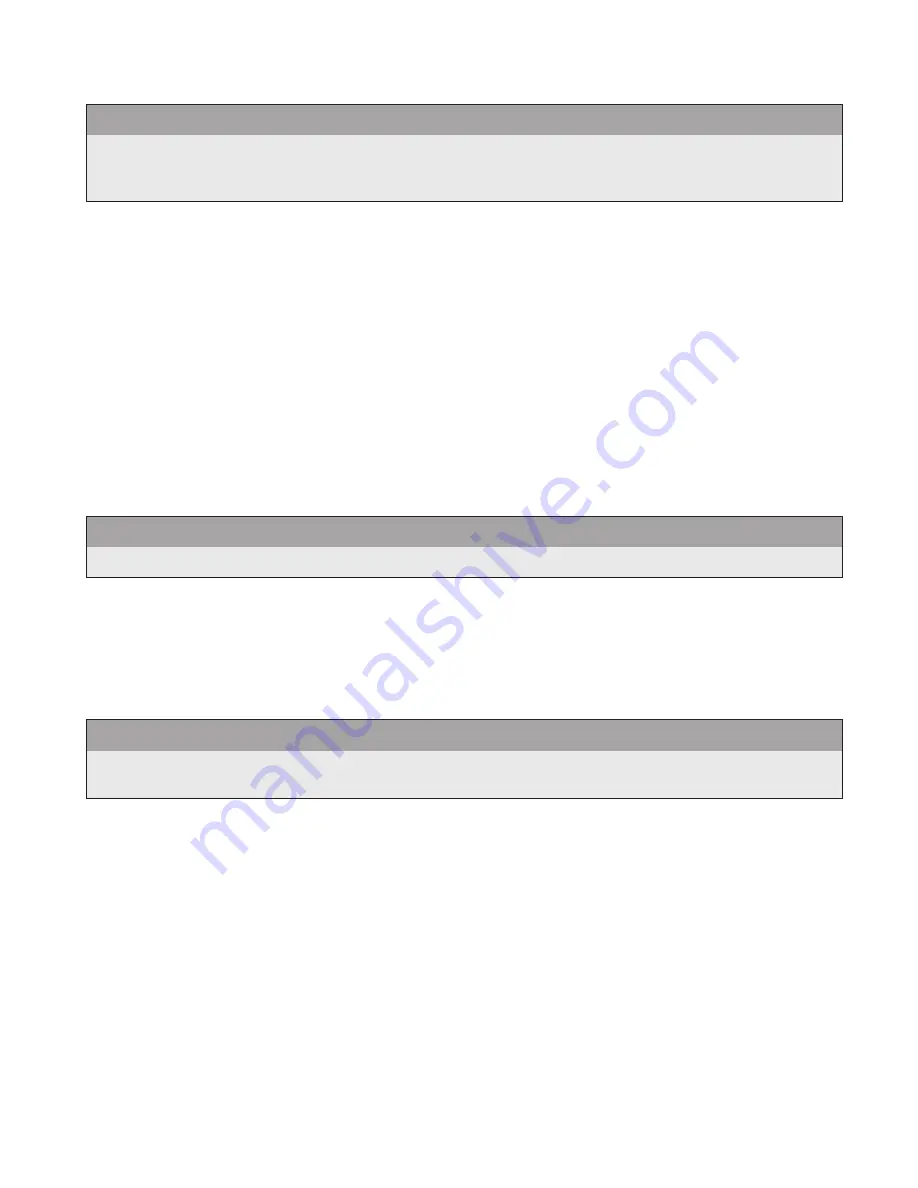
Page 17
Section 7
(continued)
CAUTION
Failure to properly set the Motor Overload Setting switches can result in loss of motor overload protection
and will void the motor warranty. Nuisance tripping or motor damage can occur if these switches are not set
properly.
Setting the Acceleration/Deceleration Switches
Switch 4 from bank 1 and switches 1 and 2 from bank 2 control the acceleration/deceleration ramp times. The
acceleration/deceleration switches (ACCEL/DECEL RAMP SETTINGS) control how fast the controller will change
the speed of the motor. The ramp setting is the time it takes the motor to change from minimum speed to
maximum speed. For example, if the ramp setting is set to 1 second and the minimum speed is set to 30Hz, the
motor will ramp up from 30Hz to 60Hz in 1 second. A faster ramp setting should be used in systems where the
flow rate can change quickly. This means that the motor can react faster to maintain the set pressure. A slower
ramp setting should be used in systems where the flow rate changes slowly or where fast changes in speed can
cause water hammer or pressure surges.
Setting the No Water Restart Time Switches
Switches 3 and 4 from bank 2 control the no water restart time. The no water (dry well) restart time switches
control the time between a no water (dry well) error and the restart of the system. For example, if the no water
restart time switches are set to 30 minutes, the system will restart 30 minutes after a no water (dry well) error
has been detected. For the 10 minute restart time, the controller will not restart if 5 faults are detected within 60
minutes. All other settings will continue to restart after the chosen restart time.
NOTE
Failure to properly set the motor overload switches can result in nuisance no water (dry well) faults.
Setting the Minimum Frequency Switch
Switch 1 from bank 3 controls the minimum frequency. The minimum frequency switch controls the slowest
speed that the motor will run. For submersible pump/motor applications these switches must always be set to
30Hz minimum speed. For above ground applications with high suction pressure, the 15Hz setting can be used
to prevent pressure oscillation at low speeds. In some cases the suction pressure may be high enough that the
pump exceeds the pressure setting at 30Hz. In this case the 15Hz setting can be used.
CAUTION
Failure to properly set the minimum frequency switch can result in motor damage and will void the motor
warranty. The minimum frequency must be set to 30Hz for submersible applications.
Setting the Carrier Frequency Switch
Switch 2 from bank 3 controls the carrier frequency. For model numbers without the F suffix, the switch can be
used to change the output carrier frequency to avoid audible noise issues in above ground applications. For
model numbers with the F suffix, this switch is disabled and the carrier frequency is always set to 2 kHz.
Setting the Pressure
When power is applied the pump will start and the system pressure will increase to the factory preset pressure
(50 PSI if SP1 is enabled and a 300 PSI sensor is used or 75PSI if SP2 is enabled and a 300 PSI sensor is used).
After the pressure has stabilized, use the increase (INC) or decrease (DEC) pressure adjust pushbuttons to
adjust the pressure setting. Push and Hold the increase or decrease pushbutton until the desired pressure
setting is reached. The new pressure setting will save when the system goes into standby mode (solid green
light/pump off). Pressure set point 1 will be adjusted and stored when the SP2/SP1 switch input is open.
Pressure set point 1 is preset to 50 PSI when used with a 300 PSI transducer. Pressure set point 2 will be
adjusted and stored when the SP2/SP1 switch input is closed. Pressure set point 2 is preset to 75 PSI when used
with a 300 PSI transducer.
STARTING THE SYSTEM