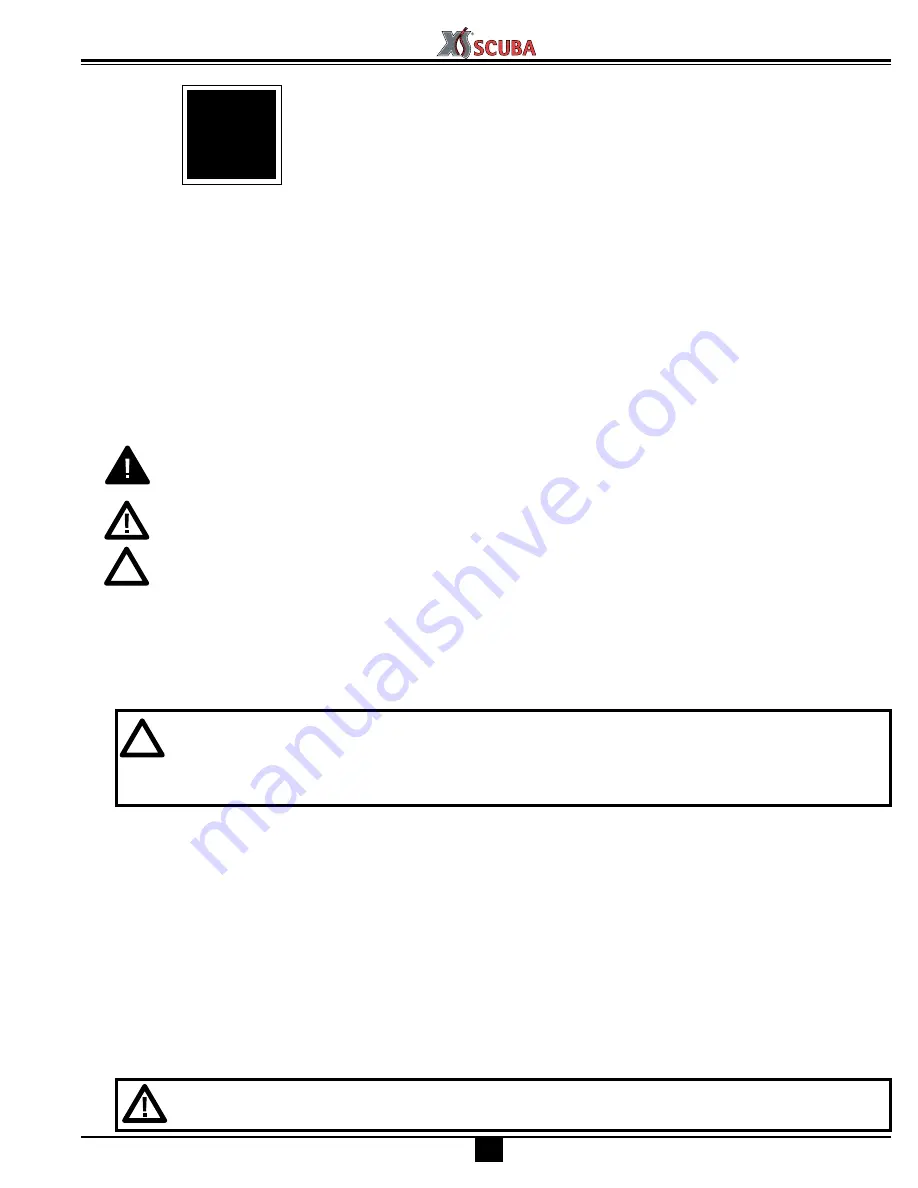
Service & Repair Manual
3
Copyright ©2008 XS Scuba
This manual provides factory prescribed procedures for the correct service and repair of the
AirWave™ second stage regulator. It is not intended to be used as an instructional manual for
untrained personnel. The procedures outlined within this manual are to be performed only by
personnel who have received factory authorized training through a repair seminar that has been
directly sponsored by XS Scuba.
If you do not completely understand all of the procedures outlined in this manual, contact
XS
Scuba
to speak directly with a Technical Advisor before proceeding any further.
Warnings, Cautions, & Notes
Pay special attention to information provided in Warnings, Cautions, and Notes that are ac-
companied by one of these symbols:
A
WARNING
indicates a procedure or situation that may result in serious injury or death if instruc-
tions are not followed correctly.
A
CAUTION
indicates any situation or technique that will result in potential damage to the product, or
render the product unsafe if instructions are not followed correctly.
A
NOTE
is used to emphasize important points, tips, and reminders.
Scheduled Service
Because the AirWave™ regulator is considered to be a life-supporting product, it is extremely
critical that it receives service according to the procedures outlined in this manual on a regularly
scheduled basis; at least once a year with normal or infrequent use.
NOTE: A unit that receives heavy or frequent use, such as in rental, instruction, or com-
mercial applications, should be serviced at least twice each year - or more often - depending
on the conditions of use and the manner in which it is maintained. (Refer to the care and
maintenance procedures outlined in the AirWave User's Guide.)
When performing service, whether it is a routine overhaul or a repair of a specific problem, it is
important to understand how the regulator is designed and how it operates. If you have any ques-
tions, please consult your XS Scuba representative.
EAN/ Nitrox Service
Newly manufactured XS Scuba regulators are assembled and packaged to be compatible with
oxygen enriched air (EAN/ Nitrox), not to exceed 40% oxygen content. If the regulator is going to
be used for this application, however, it must be dedicated and clearly labled as such, in order to
prevent any crossover use with standard compressed air.
Refer to the instructions provided in
the XS Scuba Authorized Service Document, titled - Regulator Parts Cleaning Procedures.
CAUTION: It is important to avoid using, testing, or otherwise pressurizing a dedicated
EAN regulator with standard compressed air, which contains hydrocarbon contaminants.
Introduction
1
SECTION