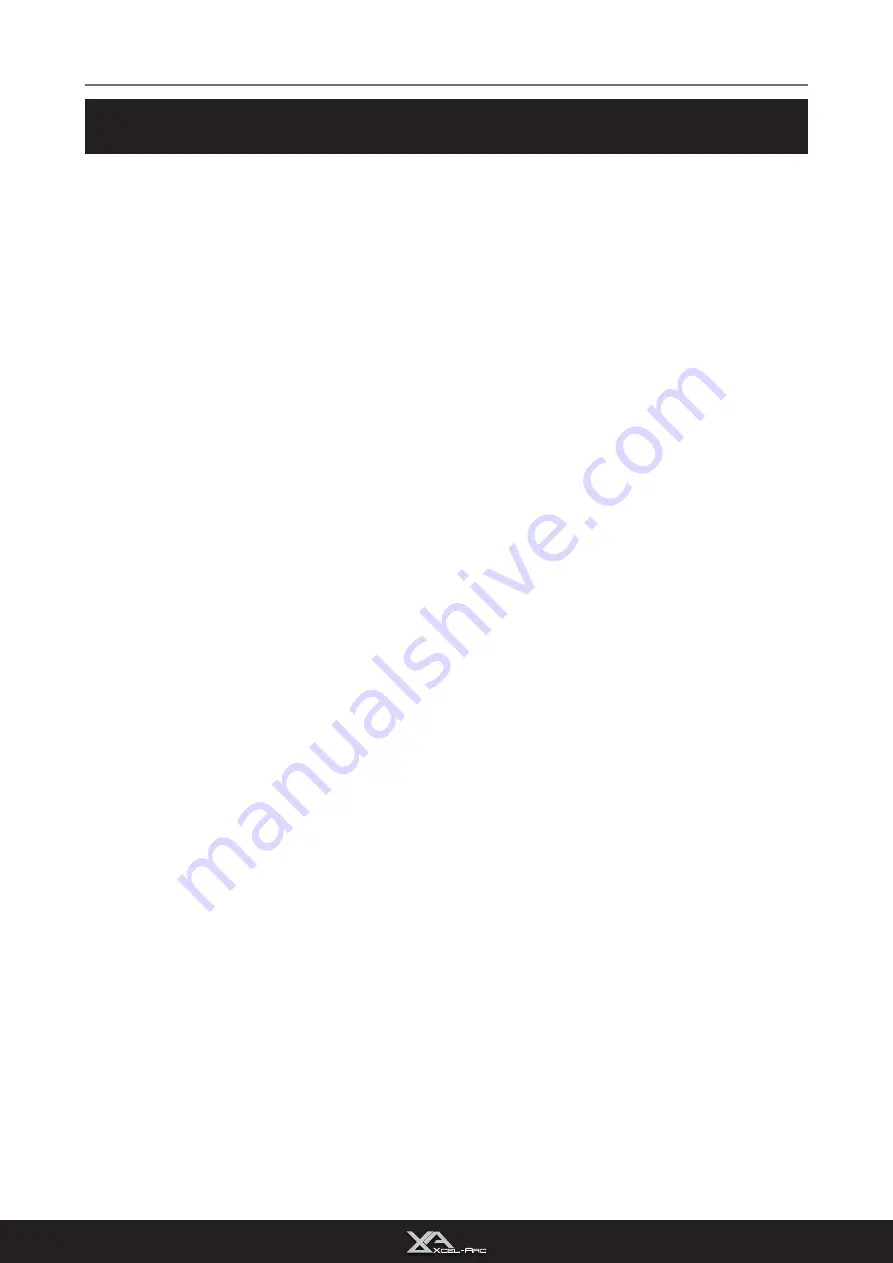
1. The cutting torch fails to ignite the arc when the torch trigger is pressed.
• Air pressure too high or too low, check and adjust air pressure to 0.5MPA (75psi).
• The shield cup is not installed correctly, turn off the power source, install and screw it down properly,
then turn on the power source.
• The electrode, swirl ring or cutting tip is not installed correctly, turn off the power source, install the electrode,
swirl ring or cutting tip correctly, and screw shield cup down properly, then turn on the power source.
2. The cutting torch fails to ignite the arc when the torch trigger is pressed
the temperature lamp is on.
• Power Supply is overheated (OC/OT lamp on), let the unit cool down for at least 5 minutes. Make sure
the unit has not been operated beyond Duty Cycle limit. Refer to page 8 for duty cycle specifications.
• Faulty components in unit return for repair.
3. No cutting output; Torch activated, power source on; Air flows;
Fan operates.
• Torch not correctly connected to the power source, check that torch leads are correctly connected to
the power source.
• Work cable not connected to the workpiece, or connection is weak, make sure that work cable has a
proper connection to a clean, dry area of the workpiece.
• Faulty components in unit, return for repair
• Faulty torch, return for repair
4. Low cutting output
• Incorrect setting of CURRENT (A) control, check and adjust to the proper setting.
• Faulty components in the unit, return for repair.
5. Difficult Starting
• Worn torch parts (consumables), shut off input power. Remove and inspect torch shield cup, cutting
tip, swirl ring and electrode. Replace electrode, cutting tip or swirl ring if worn; replace shield cup if
excessive spatter has adhered to it.
6. Arc shuts off during operation; arc will not restart when the torch
switch is activated.
• Power Supply is overheated (OC/OT lamp on), let the unit cool down for at least 5 minutes. Make sure
the unit has not been operated beyond Duty Cycle limit. Refer to Section 2 for duty cycle specifications.
• Torch consumables worn, check torch shield cup, swirl ring, cutting tip and electrode; replace as needed.
• Faulty components in unit return for repair.
7. No air flow; the power LED on; Fan operates.
• Air not connected or pressure is too low, check air connections. Adjust air pressure to the proper setting.
• Faulty components in unit return for repair.
8. Torch cuts but low quality
• Current (A) control set too low, increase the current setting.
• The torch is being moved too fast across the workpiece, reduce cutting speed.
• Excessive oil or moisture in torch, hold torch 1/8 inch (3 mm) from a clean surface while purging and
• Observe oil or moisture build-up (do not activate torch). If there are contaminants in the air, additional
filtering may be needed. Refer to sub-micronic air filter page page 17.
WARNING: There are extremely dangerous voltage and power levels present inside this unit. Do not attempt to
diagnose or repair unit by removing external cover unless you are an authorised repair agent for Xcel-Arc.
FAQ & TROUBLESHOOTING
19
Содержание VIPER CUT 30Mk II
Страница 2: ...2...
Страница 23: ...NOTES 23...