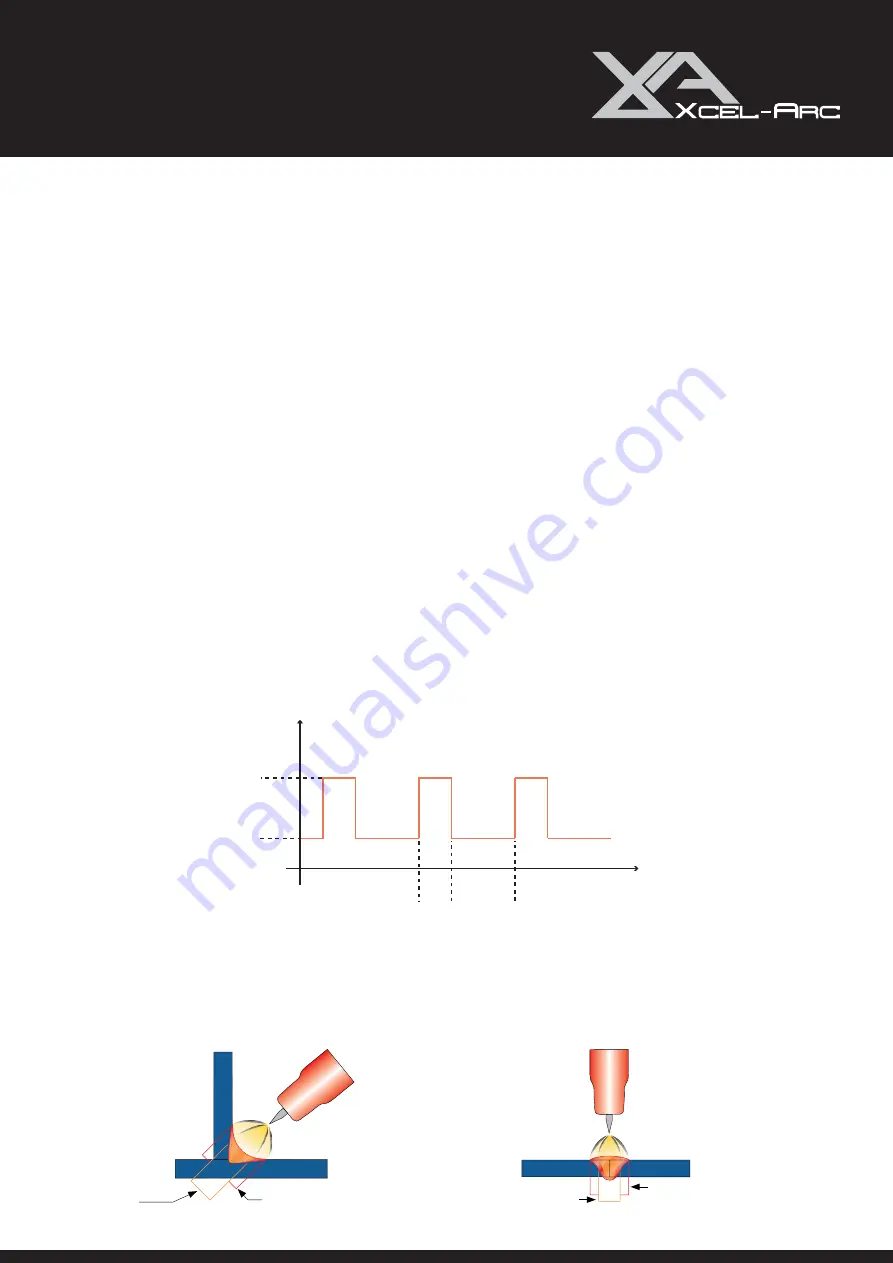
32
|
RAZORWELD™ 205SS MIG/TIG/STICK Welder Manual
TIG WELDING GUIDE
no pulse
high frequency
pulsing
no pulse
high frequency
pulsing
DC Pulse TIG Welding
Pulse TIG welding is when the current output (amperage) changes between high and low current.
Electronics within the welding machine create the pulse cycle. Welding is done during the high-amperage interval
(this high amperage is referred to as peak current). During the low amperage period, the arc is maintained but
the current output of the arc is reduced (this low amperage is referred to as base current). During pulse welding
the weld pool cools during the low amperage period. This allows a lower overall heat input into the base metal. It
allows for controlled heating and cooling periods during welding providing better control of heat input, weld pene
-
tration, operator control and weld appearance.
There are 4 variables within the pulse cycle:
Peak Current - Base Current - Pulse Frequency - Pulse Width
Setting and manipulation of these variables will determine the nature of the weld current output and is at the dis-
cretion of the operator.
Peak Current
is the main welding current (amps) set to melt the material being welded and
works much the same
as setting maximum amperage values for regular DC TIG: as a guide use 30-40 amps for every 1mm of material
thickness.
Base Current
is the set level of background current (amps) which cools the weld puddle and affects overall heat
input. Background Amps is a percentage of peak amperage. As a rule, use enough background current to reduce
the weld pool to about half its normal size while still keeping the weld pool fluid. As a guide start by setting the
background amperage at 20 to 30 percent of peak amperage.
Pulse Frequency
is the control of the amount of times per second (Hz) that the welding current switches from
Peak Current to Base Current. DC Pulse TIG frequency generally ranges from 20 to 300 HZ depending on the job
application. Control of the pulse frequency also determines the appearance of the weld.
Pulse Width is the control of the percentage of time during one pulsing cycle the power source spends at the
peak current (main amperage). Example is with the Pulse Width set at 80 percent and a rate of 1 pulse per sec
-
ond (PPS), the machine will spend 80% of the pulse at peak amperage and 20% at the base current. Increasing
the pulse width percentage adds more heat to the job, while decreasing pulse width percentage reduces heat
peak
background
ON
OFF
Current
Time
DC Pulse Tig welding allows faster welding speeds with better control of the heat input to the job, reducing the
heat input minimising distortion and warping of the work and is of particular advantage in the welding of thin stain-
less steel and carbon steel applications. The high pulse frequency capability of the advanced inverter agitates the
weld puddle and allows you to move quickly without transferring too much heat to the surrounding metal. Pulsing
also constricts and focuses the arc thus increasing arc stability, penetration and travel speeds.