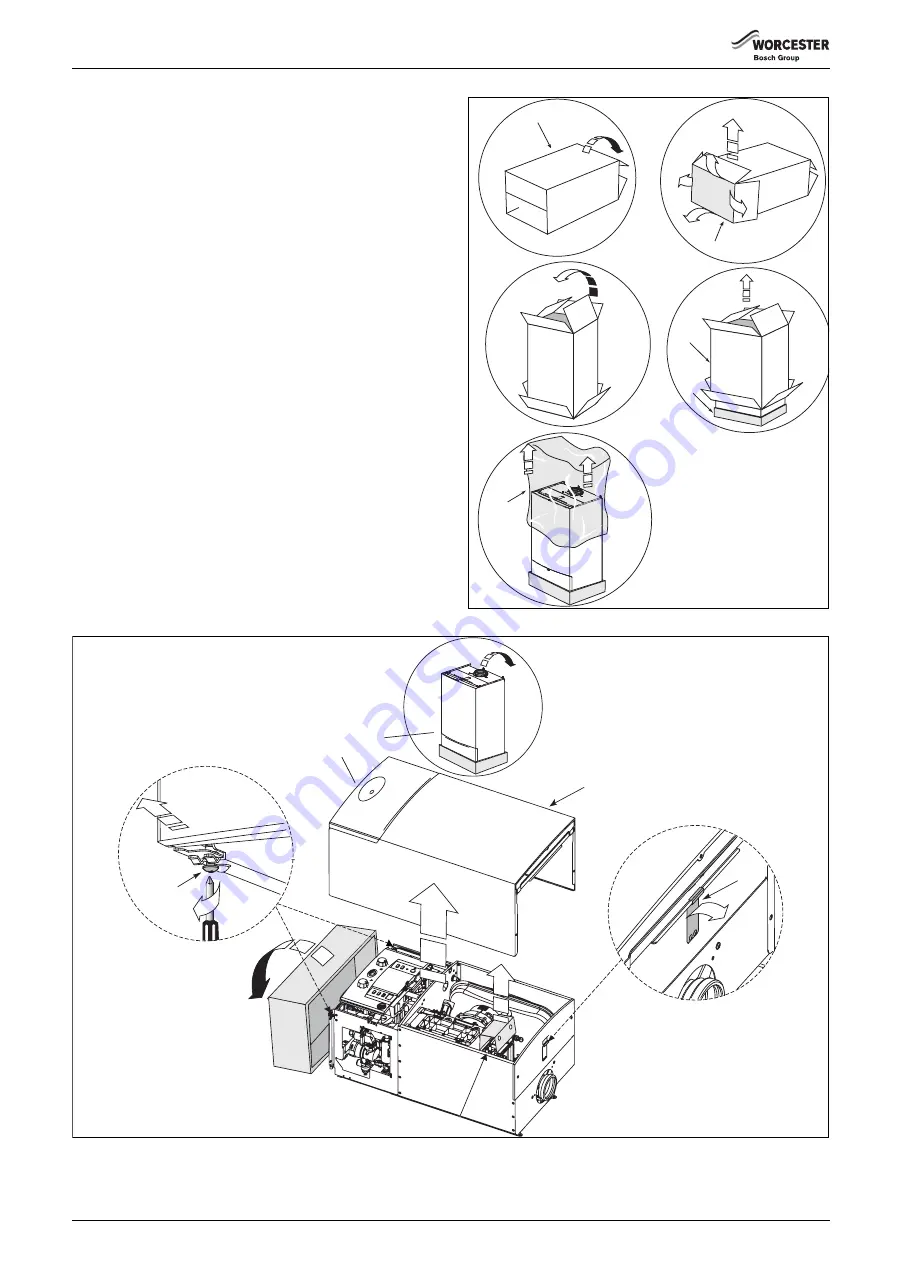
INSTALLATION
6 720 812 175 (2014/07)
22
4.3
UNPACKING THE APPLIANCE
1. With the wall frame and ancillary items removed
lay the carton (A) on its back.
2. Open the carton bottom flaps and fold under boiler. Do not remove
the packaging base.
3. Stand carton (A) with boiler upright on the packaging base (B).
4. Remove outer carton (A) and place safely away from the working area.
5. Remove the protective wrapping (C).
6. Lie the boiler on its back.
7. Remove the packaging base (B) and place safely away from the
working area.
REMOVING OUTER CASE
8. Loosen but do not remove the 2 screws (E) securing boiler casing at
the bottom of the appliance.
9. Pull upwards to release the clip (F) on top of the boiler and pull the
case upwards.
10. Remove the outer case.
11. Remove the protective packaging (G) from the electrode assembly.
A - Outer carton
B - Packaging base
C - Protective wrapping
D - Appliance outer case
E - Screws
F - Clip
G - Protective packaging
Fig. 24
Fig. 25 Unpacking the boiler
1.
A
TRU
CK H
ER
E
2.
B
3.
4.
B
A
5.
C
6720647361-10.1Wo
6
8
7
9
10
E
F
D
G
11
6720647361-11.3Wo
Do not use
the frame as
a handle