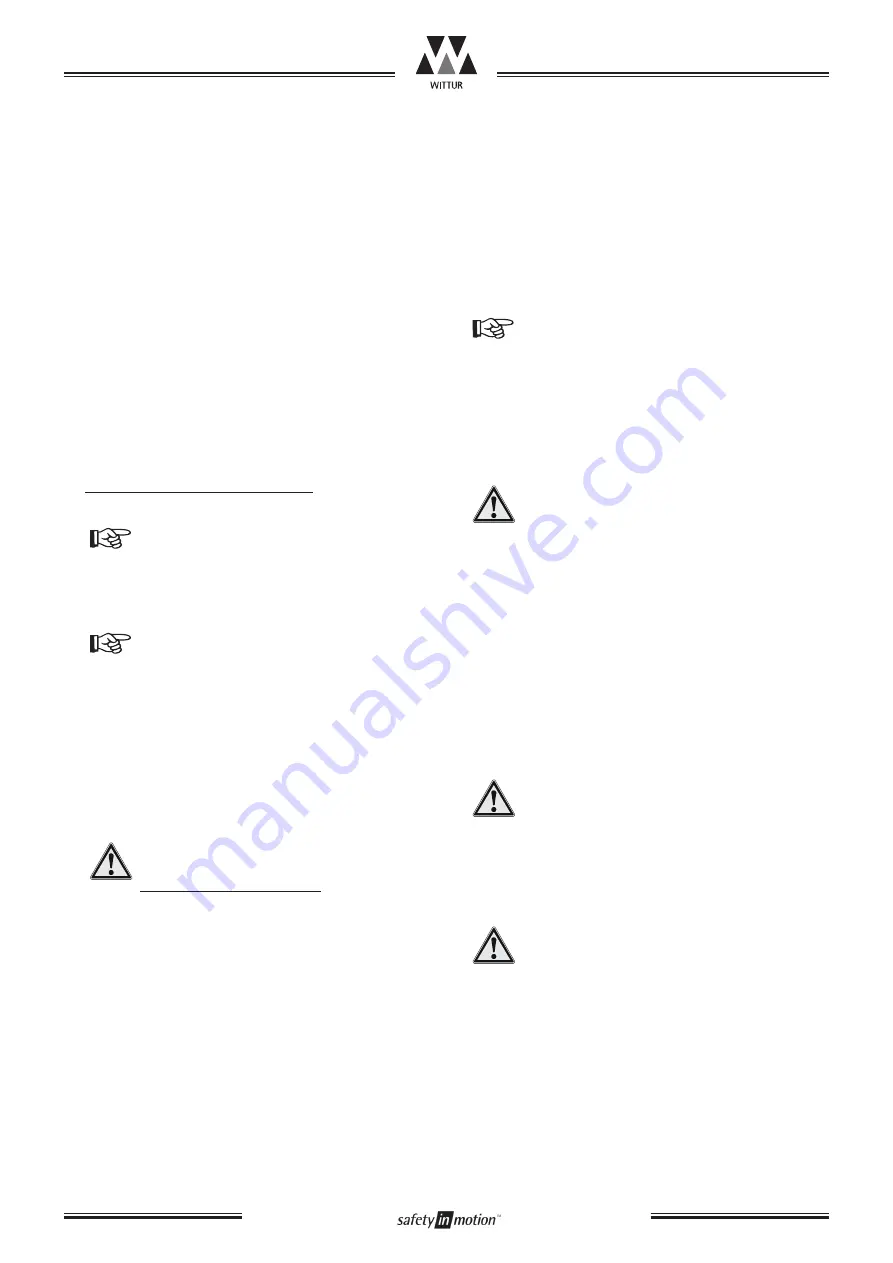
Based on the proper installation of the elevator in
compliance with all regulations, it can be assumed
that the functionality of the system is guaranteed.
Quality and function of the individual components
are subject to strict controls and are tested before
factory shipment. Prior to the initial acceptance
and perhaps even prior to TÜV tests a functional
review of the safety gear system should be per-
formed.
First test run after installation
Before the first test run:
The protective coating of grease is to be
carefully removed from the guide rails!
Clean the guide rails!
The cleaning of the guide rail must be
done with a disc brake cleaner or a similar
fluid e.g. De-Solv-It 1000 degreaser,.... . It
is important that the cleaning agent does
not leave any residue on the guide rail. It
is also not allowed to do mechanical
cleaning like grinding. If the surface can-
not be cleaned properly contact the man-
ufacturer.
Clear all people and objects from the lift
shaft before commencing the test run
Risk of crushing injuries!
The entire lift travel path should be slowly trav-
elled (in inspection mode) before the functions
tests. Attention should be paid to the clearance of
all fastened parts, especially with regards to the
guide brackets/safety gear devices. Find and
remove any protruding bolts or other dangerous
restrictions well in advance.
Preparations before tests:
When sliding guides shoes are used, clean
the installation (the sliding guide shoes
too) and if necessary also the safety gear.
Then applie a thin coating of the guide rail
oil to the guide rails or fill the oiler.
When roller guide shoes are used the guide
rail must not be lubricated at all.
The lubrication oil must not include high
pressure additives.
(see chapter 5.1.1)
• Check the activating force of the safety gear
synchronization (it should be between 200
and 250 N). This value can be higher if the
travel is over 75m. Calculate the minimum
required force F1 as follows:
F1 = mass of overspeed governor rope x down-
wards acceleration x safety factor (2)
e.g.: F1min = 100kg x 1,5m/s 2 x 2=300N
This is the minimum force which should be
measured on the car frame safety gear
synchronization to prevent unintended
gripping. If the force is less than the
retaining spring of the safety gear syn-
chronization must be adjusted.
The operating force of the optional
WITTUR synchronization is 200N - 250N.
This force can not be adjusted on site.
Änderungen vorbehalten!
Subject to change without notice!
4
Function testing
© WITTUR – All rights reserved
Progressive Type Safety Gear
CSGB-01C
Operating instructions
Blatt/
sheet
PM.7.003609.EN.012
Datum/
date
14.07.2016
Stand/
version
A-02.05.2017
Geprüft/
approved
WAT/MZE