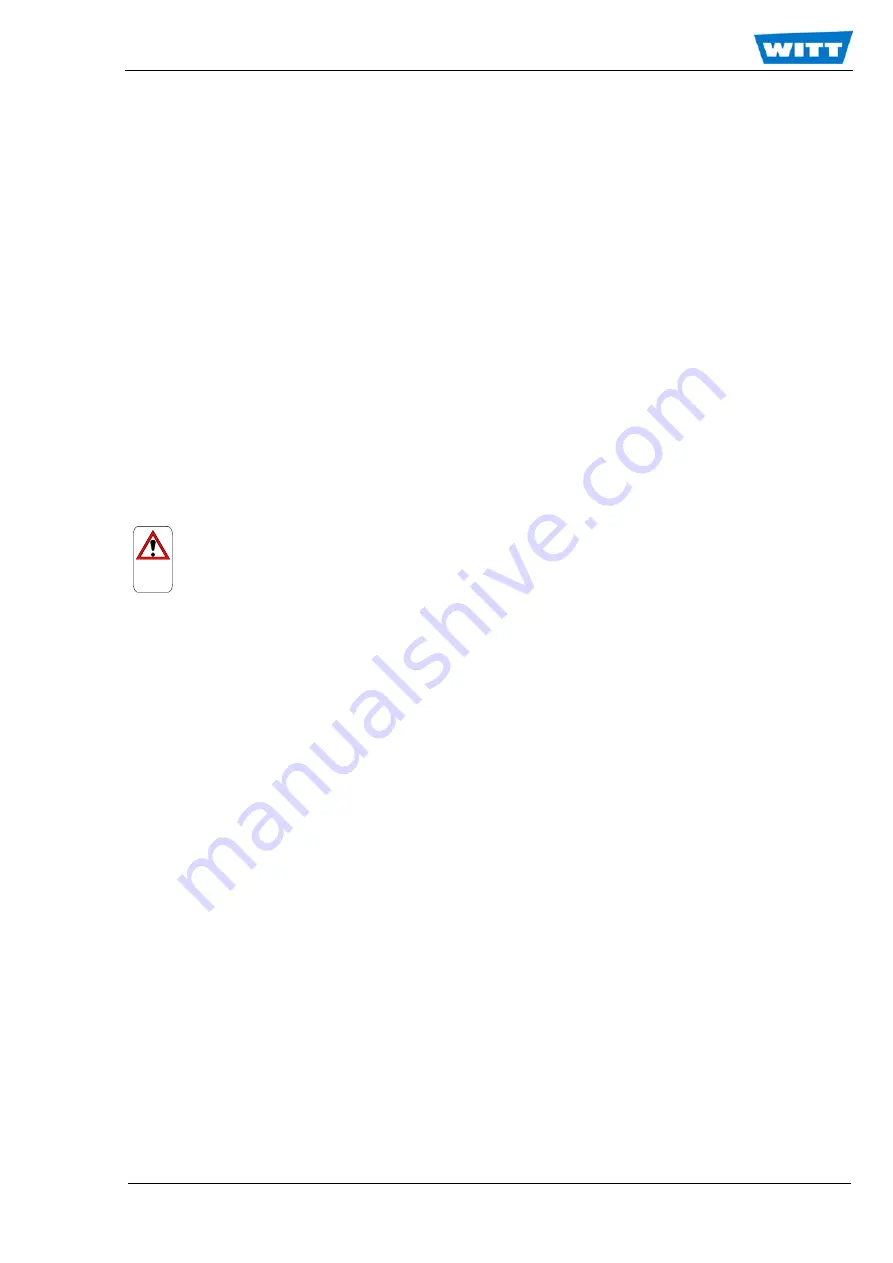
Page 11 of 27
WITT-GASETECHNIK GmbH & Co KG
Salinger Feld 4-8
: +49 (0)2302 89010
www.wittgas.com
Gas Safety- & Control Equipment
D-58454 Witten
Fax: +49 (0)2302 89013
4.2
Applications for the gas mixer
The gas mixer is used for the intermittent generation of gas mixture from two different gases.
A receiver (see technical data section 9) must be connected after the gas mixer, if not already pro-
vided. It is possible to continuously draw mixed gas from 0 to the maximum mixed gas output (see
technical data Section 9) without any change to the precision of the mixing.
The gas mixer is only suitable for the application area specified in the technical data (Section 9).
The information in Section 3 of this manual and the related safety instructions are to be observed.
4.3
Functional description of the gas mixer
Note!
The functional description is given with the aid of the enclosed function schemes (see Sec-
tion 9). You will also find the numbers for the symbols on the function scheme on the com-
ponents themselves. With the aid of the list of symbols and the function scheme, you can
identify components in the gas mixer.
The individual gases are supplied separately to the system via the correspondingly marked gas
connections with filters
(1,2)
and inlet pressure monitoring (
PvDu
and
GB
version).
A mixed gas receiver with safety valve is connected after the gas mixer. Please see the technical
data (Section 9) for the volume. If this is not the case, the customer is obliged to install an appro-
priate mixed gas receiver after the gas mixer; it is to be possible to continuously draw gas mixture
from 0 to the max. gas mixture output from the mixed gas receiver.
In the case of the
PvDu
and
GB
versions, the unit is equipped with inlet pressure monitoring that is
automatically activated when the power supply to the unit is switched on.
If the inlet pressure for one of the gases drops below the permitted minimum pressure, then the
green LED for this gas goes out on the alarm module
(81)
. In addition the alarm is also indicated on
the LCD display. In the case of the
GB
version the solenoid valve
(27)
also closes and the audible
alarm device
(84)
emits an audible warning signal.
Note!
The production of mixed gas is only interrupted on the GB version.
By means of a constant pressure regulator unit, comprising the pressure regulator
(13)
and the pi-
lot pressure regulator
(15)
, the gases to be mixed are set to a constant pressure. This ensures that
the mixture ratio remains constant with reducing pilot gas pressure, however the mixed gas flow is
reduced.
Note!
In the case of the loss of the pilot gas, the production of mixed gas is automatically
interrupted.
The required mixture ratio is set at the proportional mixing valve
(24)
in vol.-%.
The mixed gas then flows through a pressure switch or pressure transmitter / solenoid valve com-
bination
(29,27)
into the receiver. The receiver pressure can be read on the gauge
(28)
.
If the receiver pressure drops to the minimum due to the drawing of gas, the solenoid valve
(27)
in
the outlet on the gas mixer
opens and the receiver is filled with mixed gas to the maximum receiver
pressure. For the factory setting of the receiver pressure, please see the technical data (Section 9).
In the case of the MG100 and MG 200 versions is inside the mixer a metering valve
(30)
for open-
ing the connection to a separate analyser (if supplied).
Optionally a temperature monitor is located in the mixed gas outlet (see chapter 7.7).
4.3.1
Technical data on the gas mixer
Please see the enclosed data sheet for the technical data on the gas mixer (see Section 9).
PvDu
GB