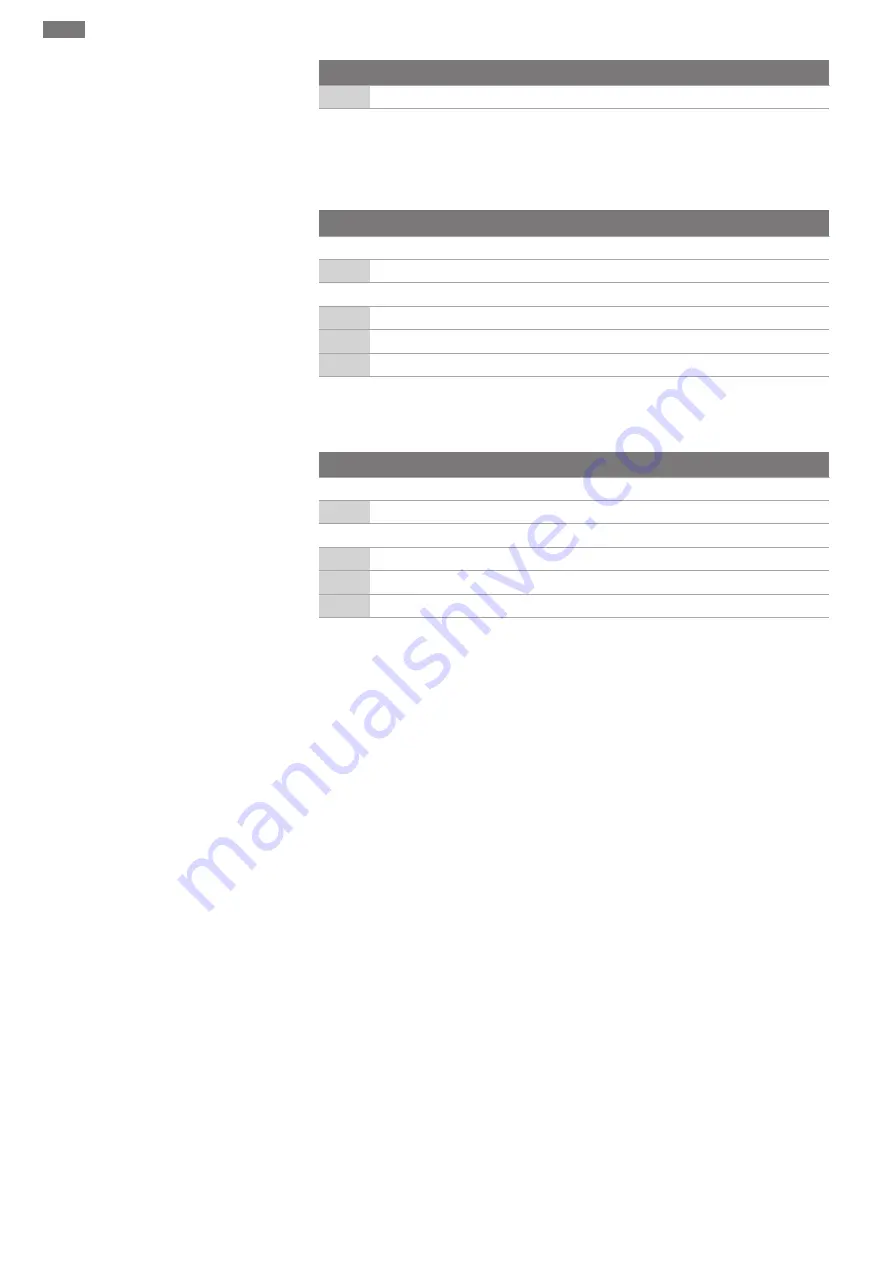
en
26
Installation and operating instructions • Wilo-Flumen OPTI-TR 50-3 ... 120-1, Wilo-Flumen EXCEL-TRE 50-3 ... 90-2 • Ed.01/2022-07
Wiring diagram
DK
Electrode connection
The system must be deactivated when the threshold is reached!
6.5.4.2 Monitoring of motor winding
With bimetallic strips
Connect the bimetallic strips directly to the switchgear or via an evaluation relay.
Connection values: max. 250 V (AC), 2.5 A, cos φ = 1
Wiring diagram for bimetallic strip
Temperature limiter
20, 21
Bimetallic strip connection
Temperature controller and limiter
21
High temperature connection
20
Centre terminal
22
Low temperature connection
With PTC sensor
Connect the PTC sensor via an evaluation relay. "CM-MSS" relay is recommended for this
purpose.
PTC sensor wiring diagram
Temperature limiter
10, 11
PTC sensor connection
Temperature controller and limiter
11
High temperature connection
10
Centre terminal
12
Low temperature connection
Trigger status for temperature controller and limiter
The installed sensor specifies the trigger temperature as part of thermal motor monitoring
using bimetallic or PTC sensors. Depending on the thermal motor monitoring version, the
following triggering status must occur when the trigger temperature is reached:
•
Temperature limiter (1 temperature circuit):
The unit must be deactivated once the trigger temperature has been reached.
•
Temperature controller and limiter (2 temperature circuits):
Once the trigger temperature for the low temperature is reached, the motor can deac-
tivate with automatic reactivation. Upon reaching the trigger temperature for the high
temperature limit, the motor must deactivate with manual reactivation.
Note the additional information in the section on potentially explosive areas described
in the appendix!
6.5.4.3 Pre-chamber monitoring (external
electrode)
Connect the external electrode via an evaluation relay. Relay “NIV 101/A” is recommended
for this. The threshold is 30 kOhm.
Once the threshold is reached, a warning must be output or the unit must be switched
off.
Note the additional information in the section on potentially explosive areas in the ap-
pendix!
6.5.5
Motor protection adjustment
6.5.5.1 Direct activation
•
Full load
Set the motor protection to the rated current according to the rating plate.
•
Partial load operation
Set the motor protection to 5 % above the current measured at the duty point.
6.5.5.2 Star-delta activation
•
The motor protection setting depends on the installation:
–
Motor protection in the motor line: Set the motor protection to 0.58 x rated current.
–
Motor protection installed in the mains supply cable: Set the motor protection to the
rated current.