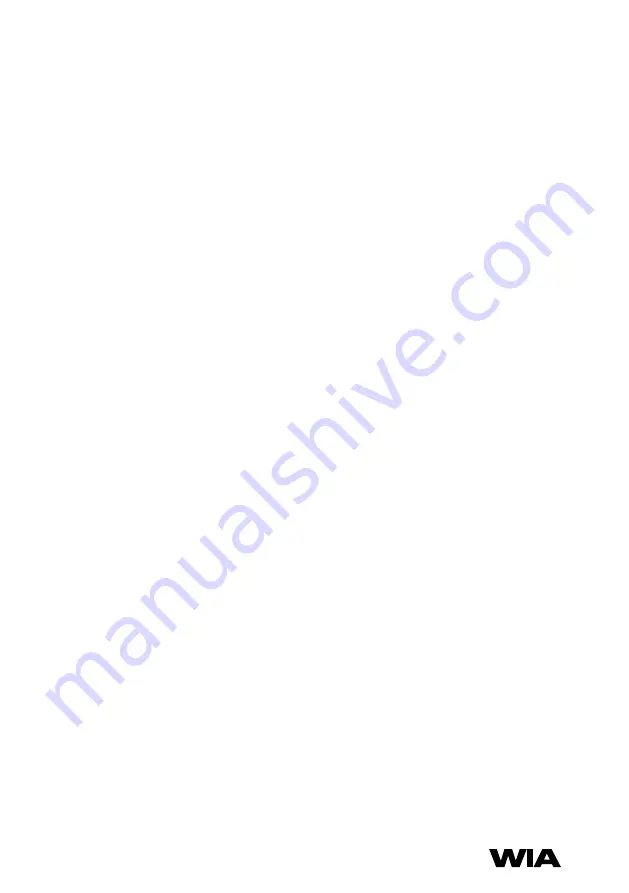
5
4
Burn Protection
The welding arc is intense and visibly bright.
Its radiation can damage eyes, penetrate
light-weight clothing, reflect from light-
coloured surfaces, and burn the skin and
eyes. Burns resulting from gas-shielded
arcs resemble acute sunburn, but can be
more severe and painful.
Wear protective clothing - leather or heat
resistant gloves, hat, and safety-toe boots.
Button shirt collar and pocket flaps, and
wear cuff less trousers to avoid entry of
sparks and slag.
Avoid oily or greasy clothing. A spark may
ignite them. Hot metal such as electrode
stubs and work pieces should never be
handled without gloves.
Ear plugs should be worn when welding in
overhead positions or in a confined space.
A hard hat should be worn when others are
working overhead.
Flammable hair preparations should not be
used by persons intending to weld or cut.
Toxic Fumes
Adequate ventilation with air is essential.
Severe discomfort, illness or death can
result from fumes, vapours, heat, or oxygen
depletion that welding or cutting may
produce. NEVER ventilate with oxygen.
Lead, cadmium, zinc, mercury, and
beryllium bearing and similar materials
when welded or cut may produce harmful
concentrations of toxic fumes. Adequate
local exhaust ventilation must be used,
or each person in the area as well as
the operator must wear an air-supplied
respirator. For beryllium, both must be used.
Metals coated with or containing materials
that emit fumes should not be heated
unless coating is removed from the work
surface, the area is well ventilated, or the
operator wears an air-supplied respirator.
Work in a confined space only while it is
being ventilated and, if necessary, while
wearing air-supplied respirator.
Vapours from chlorinated solvents can
be decomposed by the heat of the arc (or
flame) to form phosgene, a highly toxic
gas, and lung and eye irritating products.
The ultra-violet (radiant) energy of the arc
can also decompose trichlorethylene
and perchloroethylene vapours to form
phosgene. Do not weld or cut where solvent
vapours can be drawn into the welding or
cutting atmosphere or where the radiant
energy can penetrate to atmospheres
containing even minute amounts of
trichlorethylene or perchloroethylene.
Fire and Explosion Prevention
Be aware that flying sparks or falling slag can
pass through cracks, along pipes, through
windows or doors, and through wall or
floor openings, out of sight of the operator.
Sparks and slag can travel up to 10 metres
from the arc.
Keep equipment clean and operable, free
of oil, grease, and (in electrical parts) of
metallic particles that can cause short
circuits.
If combustibles are present in the work
area, do NOT weld or cut. Move the
work if practicable, to an area free of
combustibles. Avoid paint spray rooms, dip
tanks, storage areas, ventilators. If the work
can not be moved, move combustibles at
least 10 metres away out of reach of sparks
and heat; or protect against ignition with
suitable and snug-fitting fire-resistant
covers or shields.