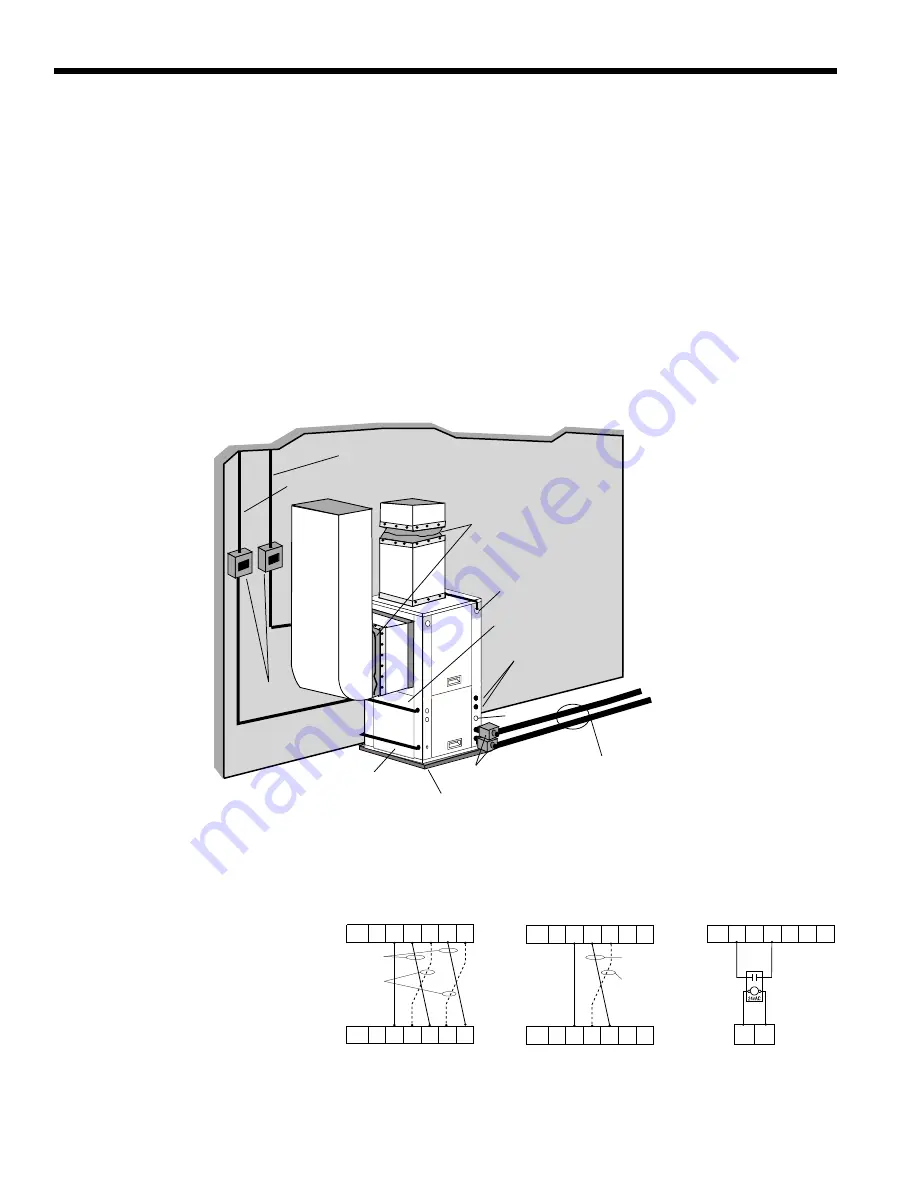
8
E SERIES INSTALLATION MANUAL
Figure 7: Closed Loop Ground Source Application
Closed Loop Ground Source Systems
Note:
For closed loop systems with antifreeze protection, set SW2-2 to the “loop” position (see table on page 18).
Once piping is completed between the unit, pumps and the ground loop (see figure below), final purging and charging
of the loop is required. A flush cart (or a 1.5 HP pump minimum) is needed to achieve adequate flow velocity in the loop
to purge air and dirt particles from the loop itself. Antifreeze solution is used in most areas to prevent freezing. Flush the
system adequately to remove as much air as possible then pressurize the loop to a static pressure of 40-50 PSI (summer)
or 50-75 PSI (winter). This is normally adequate for good system operation. Loop static pressure will fluctuate with the sea-
sons. Pressures will be higher in the winter months than during the cooling season. This fluctuation is normal and should be
considered when initially charging the system.
After pressurization, be sure to remove the plug in the end of the loop pump motor(s) (if applicable) to allow trapped air
to be discharged and to ensure that the motor housing has been flooded. Ensure that the loop pumps provide adequate
flow through the unit(s) by checking the pressure drop across the heat exchanger and comparing it to the unit capacity data
in the specification catalog. Usually 2.5 to 3 GPM of flow per ton of cooling capacity is recommended in earth loop applica-
tions.
Multiple Units on
One Flow Center
When two units are connected to
one loop pumping system, pump control is
automatically achieved by connecting the
SL terminals on connector P2 in both units
with 2-wire thermostat wire. These terminals
are polarity dependant (see Figure 8). The
loop pump(s) may be powered from either
unit, whichever is more convenient. If either
unit calls, the loop pump(s) will automati-
cally start. The use of two units on one flow
center is generally limited to a total of 20
GPM capacity.
E Series to
Electromechanical Units
Shut
Down
C C
SL2
In
SL2
Out
SL1
In
SL1
Out
E Series Unit #1
To Electromechanical Unit
C
S
Shut
Down
C C
SL2
In
SL2
Out
Shut
Down
C C
SL1
In
SL1
Out
SL2
In
SL2
Out
SL1
In
SL1
Out
Single Speed
E Series Unit #1
With pump
wired to Unit 1
With pump
wired to
Unit 2
E Series to E Series
Microprocessor Units
E Series Unit #2
Single Speed
With pump
wired to Unit 1
With pump
wired to
Unit 2
Shut
Down
C C
SL2
In
SL2
Out
Shut
Down
C C
SL1
In
SL1
Out
SL2
In
SL2
Out
SL1
In
SL1
Out
Dual Capacity
E Series Unit #1
E Series Unit #2
Dual Capacity
E Series to E Series
Microprocessor Units
Figure 8: Primary/Secondary Hook-up
Flexible Duct
Collar
Vibration Absorbing Pad
P/T Plugs
Drain
To Loop
or
Flow Center
Desuperheater
Connections
Auxiliary
Heater
Knockout
Low
Voltage to
Thermostat
Unit Supply
Auxiliary Heat
Supply
Insulated piping
or hose kit
Disconnects
(If Applicable)
Unit Power