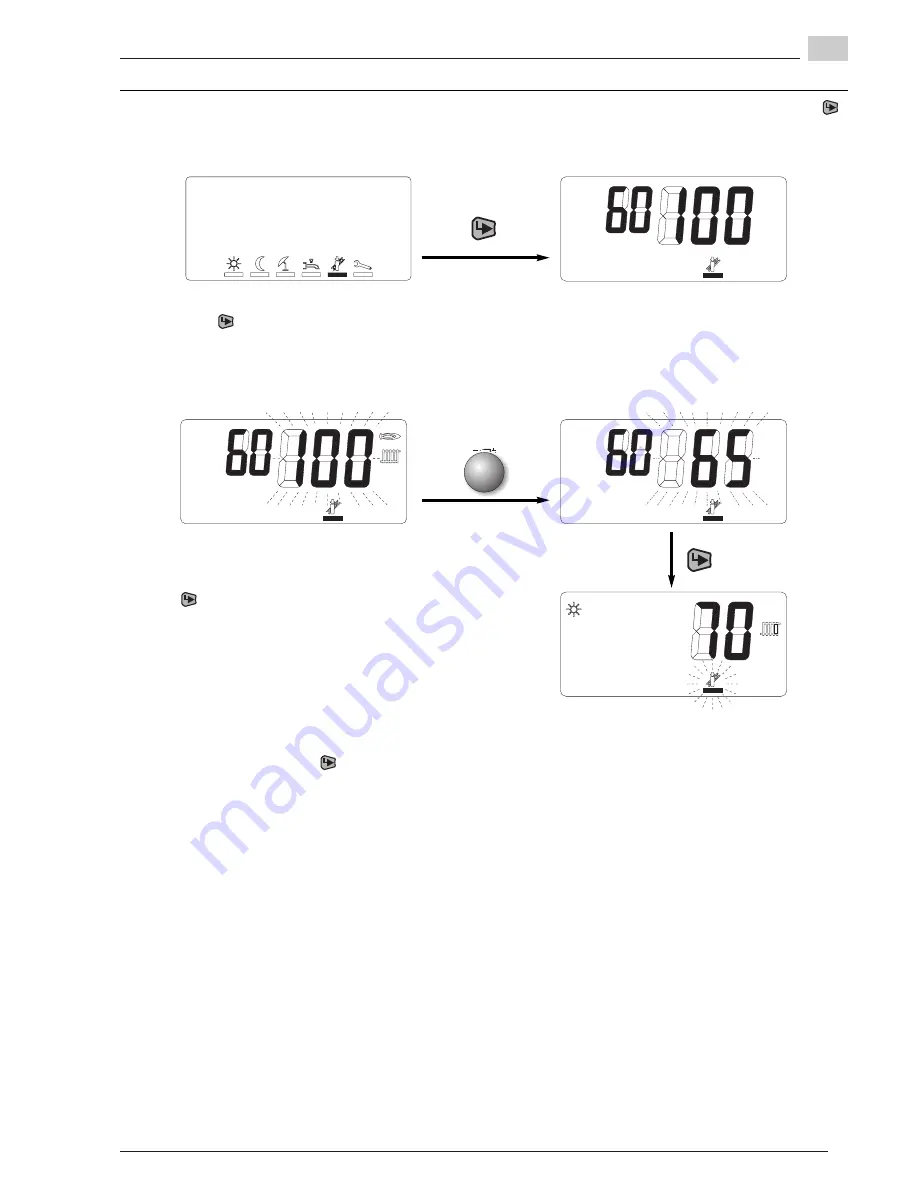
37
5
Turn the dial knob anticlockwise until the desired ratings
setting is reached. The value shown is that of the current
burner rating (in % of the maximum burner rating).
By pressing the key again the setting level, in which
the variable heat rating can be changed from maximum
heat rating to minimum heat rating, is activated.
Change over to chimney sweep mode by pressing the
key. The 3 large numbers show the current rating and the
2 smaller number show the current boiler temperature.
5.5.2 Variable ratings setting
Move the selection cursor below the “Chimney sweep”
symbol by turning the dial knob.
Press the key to exit the setting level. The WTC
remains in operation for 2 minutes with the rating last set.
Within these 2 minutes the time sequence can be
restarted in the heating engineer menu using the dial knob.
This offers the possibility to call up information in the Info
level (see Ch. 6.3.2).
Note:
•
To exit the chimney sweep function, select ESC using
the dial knob and confirm with key.
•
If the heat rating is reduced in the heating engineer
level (parameter P37), the percentage ratings setting
range is also modified, that means, as the min. rating
of the boiler is predetermined, the percentage value
displayed increases accordingly.
Содержание thermo condens WTC 15-A
Страница 92: ...92 Notes A ...
Страница 93: ...93 A ...