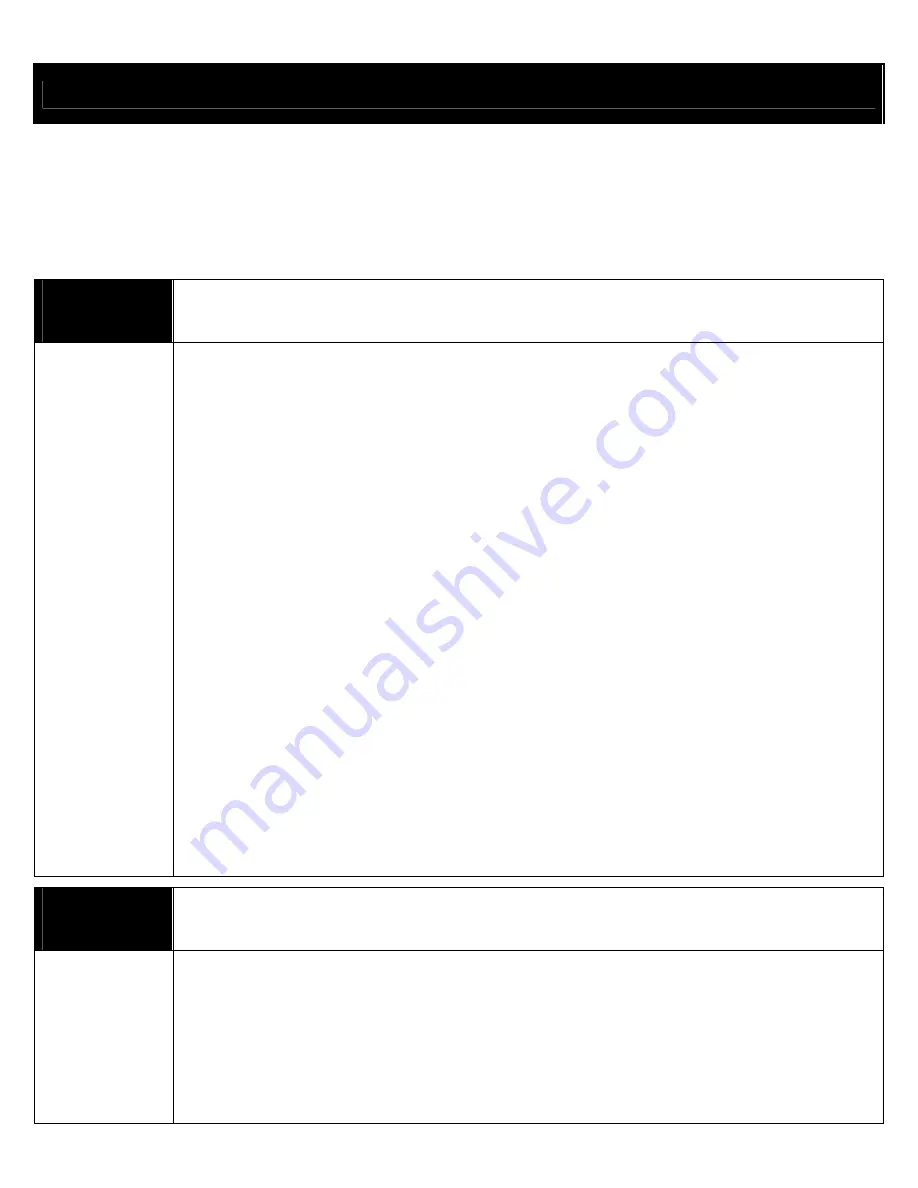
6
Installation
IMPORTANT
: Stainless steel lag screws or PT2000 coated lag screws must be used when installing center bearing brackets, end bearing brackets, jamb
brackets, operator mounting / support brackets and disconnect brackets on treated lumber (preservative-treated). Stainless steel or PT2000 coated lag
screws are NOT necessary when installing products on un-treated lumber.
NOTE
: Pilot drilling, using a 5mm (3/16”) drill bit (B2), is recommended when fastening ø8x40mm (5/16” x 1 5/8”) lag screws (A8) into wood structure.
IMPORTANT
: Right and left hand is always determined from inside the building looking out.
1
Door Assembly Mounting
(See Diagram 1 on page 3 of Drawings of Installation, Use and Maintenance manual)
Tools Needed:
Electric Drill (With
Clutch)
5mm (3/16”) Drill Bit
Level
Tape Measure
Step Ladder
11mm (7/16”) Hex
Head Driver
11 mm (7/16”)
Wrench
NOTE:
Spreader bar will always be shipped at the bottom of the door assembly (A1) to secure the door frame. To ensure
proper door spacing and alignment, do not remove the spreader bar assembly (1a) until door-frame is secured to the jamb and
bottom plate (1b) is anchored to the floor.
NOTE:
TorqueMaster® III counterbalance system and cables are under extreme tension! Never tamper with the
TorqueMaster® III counterbalance system or serious injury may occur.
NOTE
: Do not operate emergency disconnect handle until frame, horizontal track, and spreader bar are completely installed.
NOTE:
Start assembly / installation process only after door assembly is positioned vertically in the opening.
Remove the shipping brackets (1c) by removing the two screws (1d) and bolt (1e). Re-install the two screws (1d) to secure the
top brackets (1f) to the top section, as shown in
FIG. 1.1
. Repeat for right hand side.
Starting on the left side, align the outside edge of flagangle (1i) with the groove of the molded transition track (A9). Slide the
molded transition track assembly into position until the slot (1j) in flagangle aligns with hole (1k) in the molded transition track.
Secure molded transition track assembly to flagangle with one Ø6 x 15mm (1/4” - 20 x 9/16”) track bolt (A6) and Ø6mm (1/4” -
20) flange hex nut (A7), as shown in
FIG. 1.2
and
1.3.
Repeat for right hand side.
NOTE
: ensure the Ø6 x 15mm (1/4” - 20 x 9/16”) track bolt is going through the molded transition track first, and the
Ø6mm (1/4” - 20) flange hex nut is on the outside of flagangle, as shown in
FIG. 1.3
.
NOTE
: Check for smooth transition between molded transition track (A9) and top of vertical track (1m), as shown in
FIG.
1.3
.
Place the door frame (A1) into the door opening. Level (B3) the door frame horizontally and vertically. Secure leveled door
frame with proper anchors (A10) and Ø8 x 40mm (5/16” x 1-5/8”) lag screws (A8) through the four jamb brackets (1g), as shown
in
FIG. 1.4
and
FIG. 1.5
. Secure the angle bracket located on the left hand side of the opener (1x), to the ceiling using one
proper anchor (A10) and one Ø8 x 40mm (5/16” x 1-5/8”) lag screw (A8) through the slotted hole in the angle bracket (2o), as
shown in
FIG. 1.6
. Once the angle bracket is secured to the ceiling, tighten the Ø6mm (1/4” - 20) flange hex nut (A7).
NOTE
: ensure that the angle bracket is secured to a ceiling joist or other structurally sound framing member and not just into
drywall or into paneling.
Secure the bottom plate (1b) to the floor with one Ø8 x 40mm (5/16” x 1-5/8”) lag screw (A8) and anchor (A10), as shown in
FIG. 1.5
. Repeat for opposite side.
2
Horizontal Track Mounting
(See Diagram 2 on page 4 of Drawings of Installation, Use and Maintenance manual)
Tools Needed:
11mm (7/16”) Wrench
Screw Driver (Flat
Head)
Slide the horizontal track (A2) into the groove of the molded transition track (A9) and secure with one Ø6 x 15mm (1/4” – 20 x
9/16”) track bolt (A6) and Ø6mm (1/4” - 20) flange hex nut (A7), as shown in
FIG. 2.1
. Repeat for other side.
NOTE
: On some models this may already have been done at the factory.
NOTE
: ensure the Ø6 x 15mm (1/4” - 20 x 9/16”) track bolt is going through the inside of horizontal track first, and the Ø6mm
(1/4” - 20) flange hex nut is on the outside of the molded transition track, as shown in
FIG. 2.1
.
Remove the spreader bar assembly (1a) from the door frame by removing the Ø6 x 15mm (1/4” - 20 x 9/16”) track bolts (A6)
and Ø6mm (1/4” - 20) flange hex nuts (A7), as shown in
FIG. 2.2
. Repeat for other side. Set the spreader bar assembly with the
Ø6 x 15mm (1/4” - 20 x 9/16”) track bolts and Ø6mm (1/4” - 20) flange hex nuts aside.