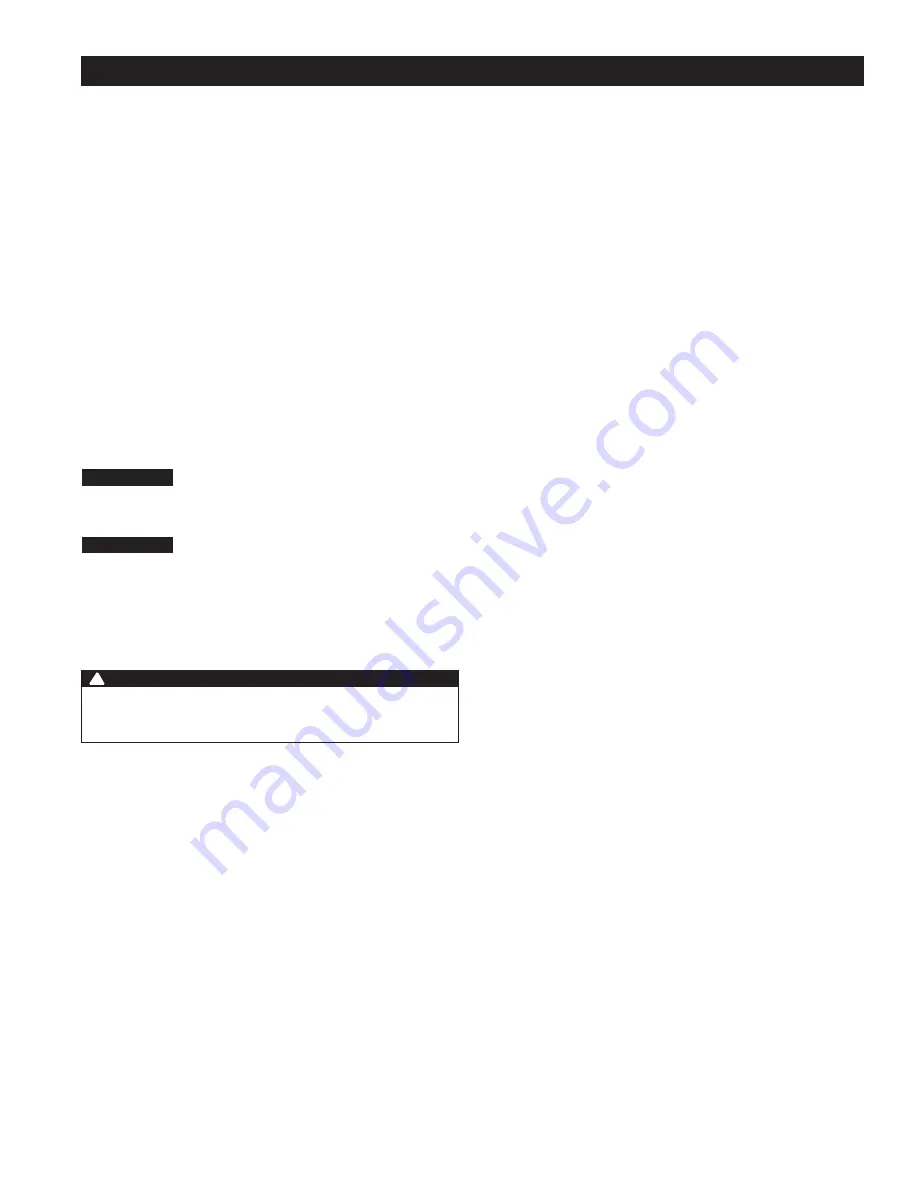
9
System Installation
Pre-Installation Considerations
• A minimum of 25psi of water pressure is required for regeneration
valve to operate effectively.
• A continuous 115 volt, 60 Hertz current supply is required.
Make certain the current supply is always hot and cannot be
turned off with another switch.
• Condition of existing plumbing should be free from lime and
iron buildup. Piping that is built up heavily with lime and/or iron
should be replaced. If piping is clogged with iron, a separate
iron filter unit should be installed ahead of the water softener.
• The softener should be located close to a drain.
• Always provide for the installation of a bypass valve.
• The full weight of the plumbing system must be supported by
pipe hangers or other means.
• Do not install the system where it would block access to the water
heater, main water shutoff, water meter, or electrical panels.
• Install the system in a place where water damage is least likely
to occur if a leak develops.
• If applicable, use di-electric unions where dissimilar metals
are present.
The main control valve and all plumbing connections have
right-hand threads. Turn clockwise to install.
NOTICE
If O-ring lubricant is required, only use a silicone based
compound formulated for potable water O-ring applica-
tions. Watts recommends Ordering Code #68102757 Silicone
Lubricant. The use of other types of lubricants may attack
the control’s plastic or rubber components. Petroleum-based
lubricants can cause swelling in rubber parts, including
O-rings and seals.
NOTICE
WARNING
!
Do not exceed water pressure of 125psi (8.6 bar). Do
not exceed 110°F (43°C). Do not subject unit to freezing
conditions.
General Installation Instructions
1. Turn off water heater(s).
2. Turn off the main water supply to the building and open a treated
water faucet (cold and hot) to relieve any pressure within the
plumbing system.
3. Place the mineral tank(s) in the desired installation location.
Make sure that the location is level and sturdy enough to
support the weight of the system once it is in operation.
4. After the mineral tank(s) have been placed into their final position,
and will not need to be moved again, load the mineral tanks
with resin and gravel media following the instructions below:
4a. Inspect the distributor screens for damage, and make
sure all screens are present before loading the mineral tank
with media. Before proceeding with installation, replace any
damaged components immediately.
4b. Cap the top open end of the distributor tube with tape and
plastic sheeting to keep all media and foreign debris from
entering the distributor tube. This cap must be secure and
not come off during media loading.
4c. Place the distributor tube, screen end down, into the mineral
tank and center it in the bottom. The top of the distributor
tube should be flush with the top of the tank. Test the tape
cap to make sure it can not come off during the media
loading process.
4d. For systems 24" in diameter and larger, fill the mineral tank
1
⁄
3
full with water to prevent breakage of the distributor
tube screens during the media loading process. This step
is not required for tanks smaller than 24" in diameter.
4e. Make sure the plastic and tape cap is secure to the top of
the distributor tube, place a funnel on the top of the tank
and load first the gravel (if different sizes of gravel are used
load the largest gravel first, then the smaller gravel) then
the softening resin into the tank. The cap must not come
off of the distributor tube during the loading of the media.
4f. Remove the funnel from the top of the tank and plastic
cap and tape from the top of the distributor tube. DO NOT
PULL UP ON THE DISTRIBUTOR TUBE when removing
the cap. The distributor tube top must remain flush with
the top of the tank.
4g. Clean any media from the threads and top of the mineral
tank. Media in the threads and on the O-ring sealing sur-
face of the tank can cause tank thread damage and pre-
vent the control valve’s O-ring seal from sealing properly.
4h. Lubricate the O-rings on the bottom of the control valve
(distributor tube port O-ring and top of tank O-ring). Use
nonpetroleum based silicone lubricant only.
4i. Press the factory suppled black upper diffuser into the
base of the control valve.
4j. Place the control valve on top of the tank When perform-
ing this step, seat the top of the distributor tube inside the
distributor port located on the bottom of the control valve
first, then press the control valve down until the control valve
threads come in contact with the tank threads. This ensures
that the distributor tube is properly seated into the bottom of
the control valve.
4k. Tighten the control valve onto the tank with a clockwise
rotation. Be careful not to cross thread the control valve to
tank connection or over tighten it. A hand tight fit is appro-
priate for the control valve torque. DO NOT use a wrench.
Tank or control valve damage could result. DO NOT apply
thread sealant or plumbing tape on the control valve to
tank threaded connection.
5*. Install flow meter(s). For HC-200 Simplex and HCP-200
Progressive Series systems, apply a suitable thread sealant
to the male threads of the meter(s) and with the meter’s
direction of flow arrow pointing in the direction of water flow,
install the meter(s) directly into the outlet port(s) of the system
control valve(s). For HCTA-200 Series Duplex Alternating sys-
tems, apply a suitable thread sealant and install the meter
in the common outlet water line of the two control valves
within 30" of the nearest control valve’s controller. The
meter’s direction of flow arrow must point in the direction of
water flow.
6*. Rotate meter(s) clockwise to tighten, by gripping the meter(s)
on the hexagonal surface with a wrench, and continue to
tighten the water meter(s )until the meter dome(s) is pointing
straight up.
Содержание HC-200 Series
Страница 12: ...12 Installation Diagrams Series HCTA 200 Duplex Alternating Systems Top View Side View Front View...
Страница 13: ...13 Installation Diagrams Series HCP 200 Progressive 2 4 Tank Systems Top View Side View Front View...
Страница 17: ...17 Controller Display...
Страница 43: ...43 Flow Data and Injector Draw Rates Down Flow...