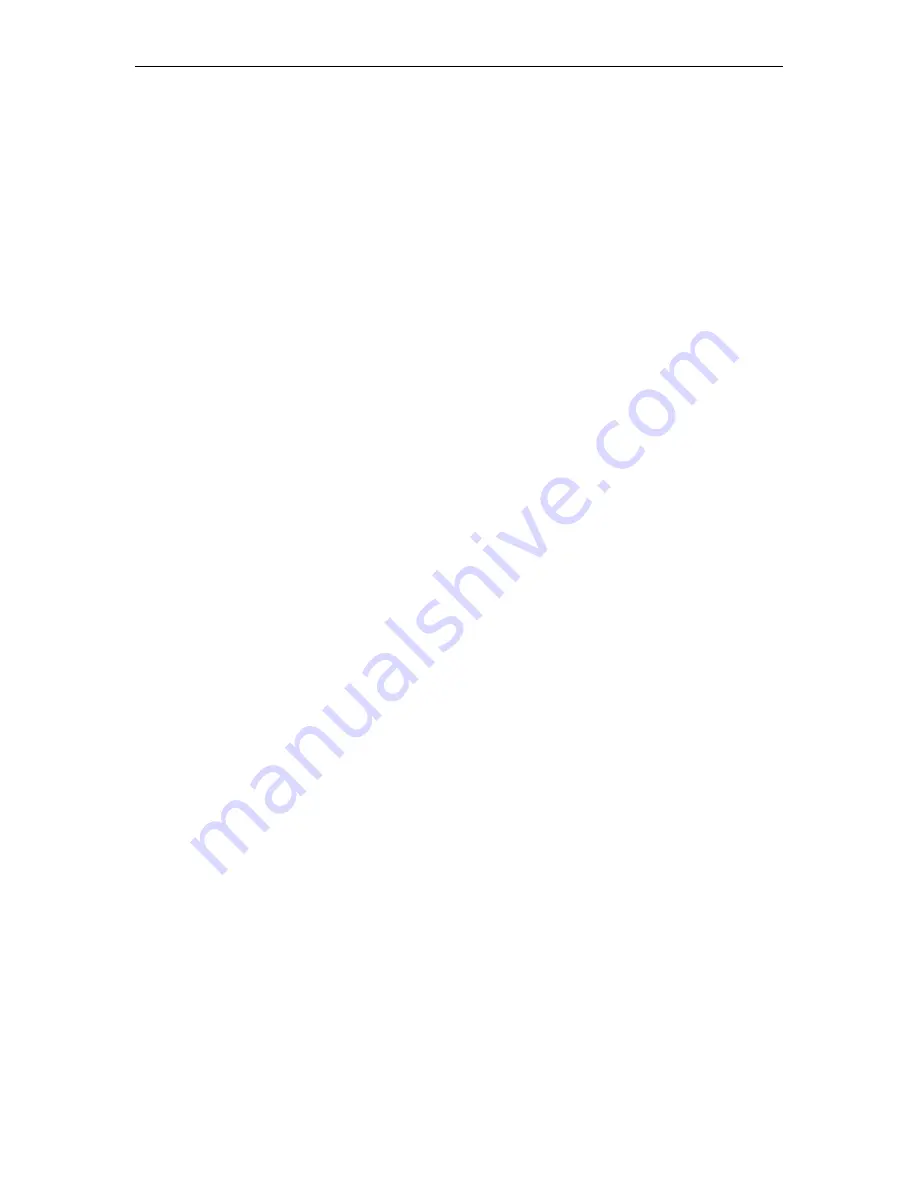
Waterous
200-B Belt-Driven Installation Guide
Rev-
Page 30 of 54
F. Suggested fittings for auxiliary air outlet:
Use 3/8” air hose
3/8” Quarter Turn Ball Valve
Fittings per discharge:
4 - #6 JIC x6 Push Loc
2 -
#6 JIC x1/2”NPT-M 90
1 -
#6 JIC x ¼”NPT-M
1
– Bulkhead fitting, Waterous part # 2330003
Fittings on all hoses should be 37° JIC
G. Air distribution manifold:
We suggest NPT fittings with the appropriate number and size ports. However, the
manifold can be built with air brake tubing if strict attention is paid to the inside diameters:
.375” OD is .250” ID
.500” OD is .375” ID
.625” OD is .500” ID
.750” OD is .625” ID
SECTION 13. AUTO-SYNC SYSTEM
This seldom needs adjusting after the initial setup if the rest of the system is well
maintained.
Note:
Do not adjust the Auto-Sync components to compensate for problems elsewhere
in the CAFS system.
Before you make any adjustments, make sure the oil level in the sump is correct,
the air and oil filters are not overdue for servicing, the oil is not overdue for
changing, the compressor is not overheating, the oil cooler strainer is clean, and
the air lines do not have leaks.
Always start by adjusting UNLOAD mode, then FIXED, then AUTO.
A common problem is unauthorized adjustment of the balance valve in an attempt to
improve performance.
If unauthorized adjustments to the Auto-Sync are a problem we suggest placing a seal
over the adjustment points. This will let maintenance personnel know if the system has
been tampered with.
Содержание 200-B
Страница 39: ...Waterous 200 B Belt Driven Installation Guide Rev Page 39 of 54 Figure 33 Basic CAFS System...
Страница 40: ...Waterous 200 B Belt Driven Installation Guide Rev Page 40 of 54 Figure 34 200 B with T Sump...
Страница 41: ...Waterous 200 B Belt Driven Installation Guide Rev Page 41 of 54 Figure 35 200 B with Vertical Sump...
Страница 42: ...Waterous 200 B Belt Driven Installation Guide Rev Page 42 of 54 Figure 36 Compressor Dimensions...
Страница 43: ...Waterous 200 B Belt Driven Installation Guide Rev Page 43 of 54 Figure 37 T Sump Dimensions...
Страница 44: ...Waterous 200 B Belt Driven Installation Guide Rev Page 44 of 54 Figure 38 10 Vertical Reservoir...
Страница 45: ...Waterous 200 B Belt Driven Installation Guide Rev Page 45 of 54 Figure 39 Oil Cooler...
Страница 46: ...Waterous 200 B Belt Driven Installation Guide Rev Page 46 of 54 Figure 40 200 B Oil and Separator...
Страница 47: ...Waterous 200 B Belt Driven Installation Guide Rev Page 47 of 54 Figure 41 Separator Bracket...
Страница 48: ...Waterous 200 B Belt Driven Installation Guide Rev Page 48 of 54 Figure 42 Hydraulic Schematic with T Sump...
Страница 50: ...Waterous 200 B Belt Driven Installation Guide Rev Page 50 of 54 Figure 44 Electrical Schematic for Auto sync...