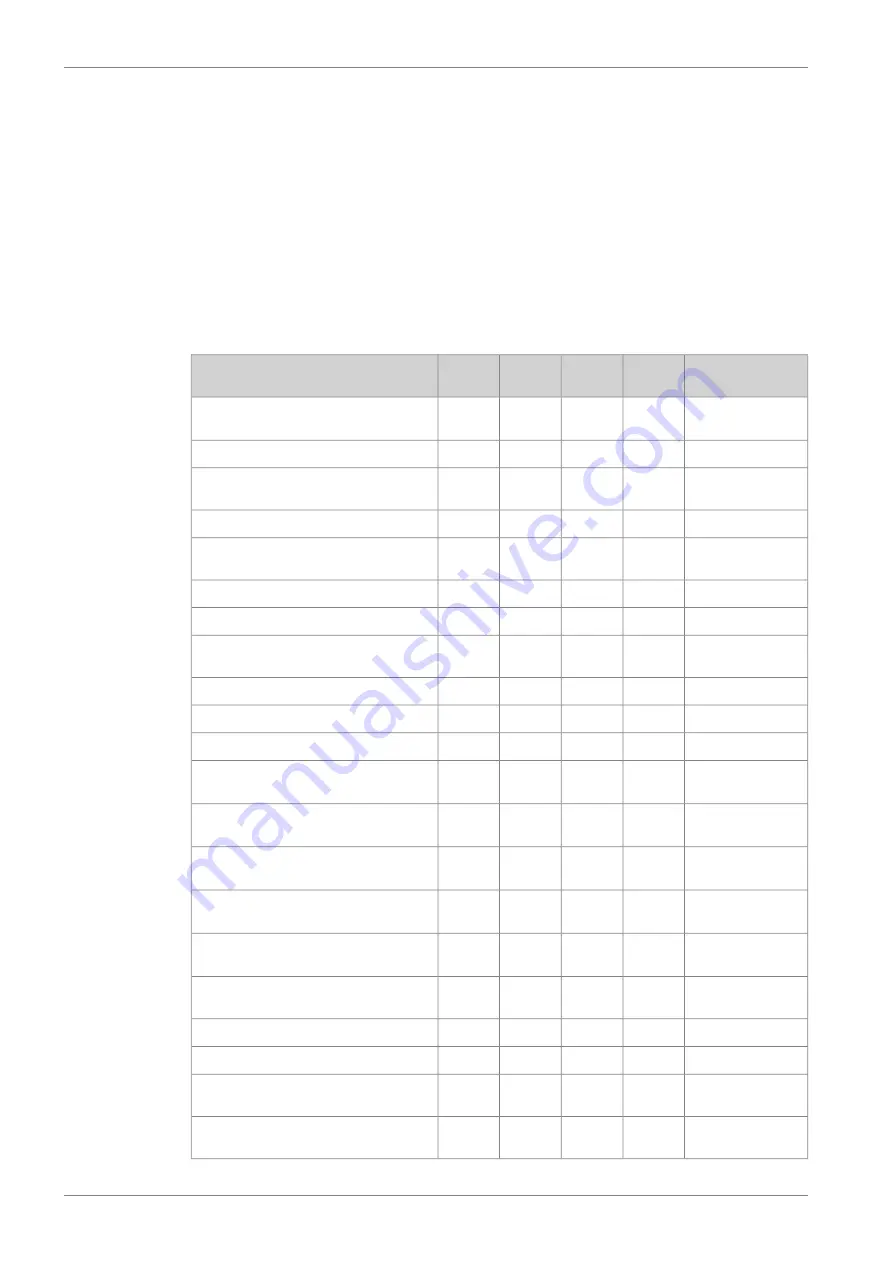
6.1.2
0,10% m/m sulphur fuels for SECA areas
Due to the new sulphur emission legislation being valid since 01.01.2015 in the specified SECA
areas many new max. 0,10% m/m sulphur content fuels have entered the market. Some of
these fuels are not pure distillate fuels, but contain new refinery streams, like hydrocracker
bottoms or can also be blends of distillate and residual fuels.
The new 0,10% m/m sulphur fuels are called as Ultra Low Sulphur Fuel Oils (ULSFO) or “hybrid”
fuels, since those can contain properties of both distillate and residual fuels. In the existing
ISO 8217:2017(E) standard the fuels are classed as RMA 10, RMB 30 or RMD 80, if not fulling
the DM grade category requirements, though from their properties point of view this is generally
not an optimum approach. These fuels can be used in the Wärtsilä® 46F engine type, but
special attention shall be paid to optimum operating conditions. See also Services Instruction
WS02Q312.
Test method refer-
ence
RMD 80
RMB 30
RMA 10
Unit
Characteristics
-
6,0 - 24
6,0 - 24
6,0 - 24
mm
2
/s
a)
Kinematic viscosity bef. injection pumps
c)
ISO 3104
80,00
30,00
10,00
mm
2
/s
a)
Kinematic viscosity at 50 °C, max.
ISO 3675 or ISO
12185
975,0
960,0
920,0
kg/m
3
Density at 15 °C, max.
ISO 8217, Annex F
860
860
850
-
CCAI, max.
e)
ISO 8574 or ISO
14596
0,10
0,10
0,10
% m/m
Sulphur, max.
b)
ISO 2719
60,0
60,0
60,0
°C
Flash point, min.
IP 570
2,00
2,00
2,00
mg/kg
Hydrogen sulfide, max.
ASTM D664
2,5
2,5
2,5
mg
KOH/g
Acid number, max.
ISO 10307-2
0,10
0,10
0,10
% m/m
Total sediment aged, max.
ISO 10370
14,00
10,00
2,50
% m/m
Carbon residue, micro method, max.
ASTM D3279
8,0
6,0
1,5
% m/m
Asphaltenes, max.
c)
ISO 3016
30
0
0
°C
Pour point (upper), max., winter quality
d)
ISO 3016
30
6
6
°C
Pour point (upper), max., summer quality
d)
ISO 3733 or
ASTM D6304-C
c)
0,50
0,50
0,30
% v/v
Water max.
ISO 3733 or
ASTM D6304-C
c)
0,30
0,30
0,30
% v/v
Water bef. engine, max.
c)
ISO 6245 or
LP1001
c, h)
0,070
0,070
0,040
% m/m
Ash, max.
IP 501, IP 470 or
ISO 14597
150
150
50
mg/kg
Vanadium, max.
f)
IP 501 or IP 470
100
100
50
mg/kg
Sodium, max.
f)
IP 501 or IP 470
30
30
30
mg/kg
Sodium bef. engine, max.
c, f)
IP 501, IP 470 or
ISO 10478
40
40
25
mg/kg
Alu Silicon, max.
IP 501, IP 470 or
ISO 10478
15
15
15
mg/kg
Alu Silicon bef. engine, max.
c)
6-4
DAAB605814
Wärtsilä 46F Product Guide
6. Fuel Oil System
Содержание 46F Series
Страница 1: ...Wärtsilä 46F PRODUCT GUIDE ...
Страница 4: ...This page intentionally left blank ...
Страница 8: ...This page intentionally left blank ...
Страница 18: ...This page intentionally left blank ...
Страница 46: ...Fig 4 3 Cross section of the V engine 4 6 DAAB605814 Wärtsilä 46F Product Guide 4 Description of the Engine ...
Страница 86: ...This page intentionally left blank ...
Страница 104: ...This page intentionally left blank ...
Страница 154: ...This page intentionally left blank ...
Страница 162: ...This page intentionally left blank ...
Страница 170: ...This page intentionally left blank ...
Страница 176: ...This page intentionally left blank ...
Страница 194: ...This page intentionally left blank ...
Страница 200: ...This page intentionally left blank ...
Страница 202: ...This page intentionally left blank ...
Страница 207: ...Fig 21 7 List of symbols DAAF406507 7 DAAB605814 21 5 21 ANNEX Wärtsilä 46F Product Guide ...