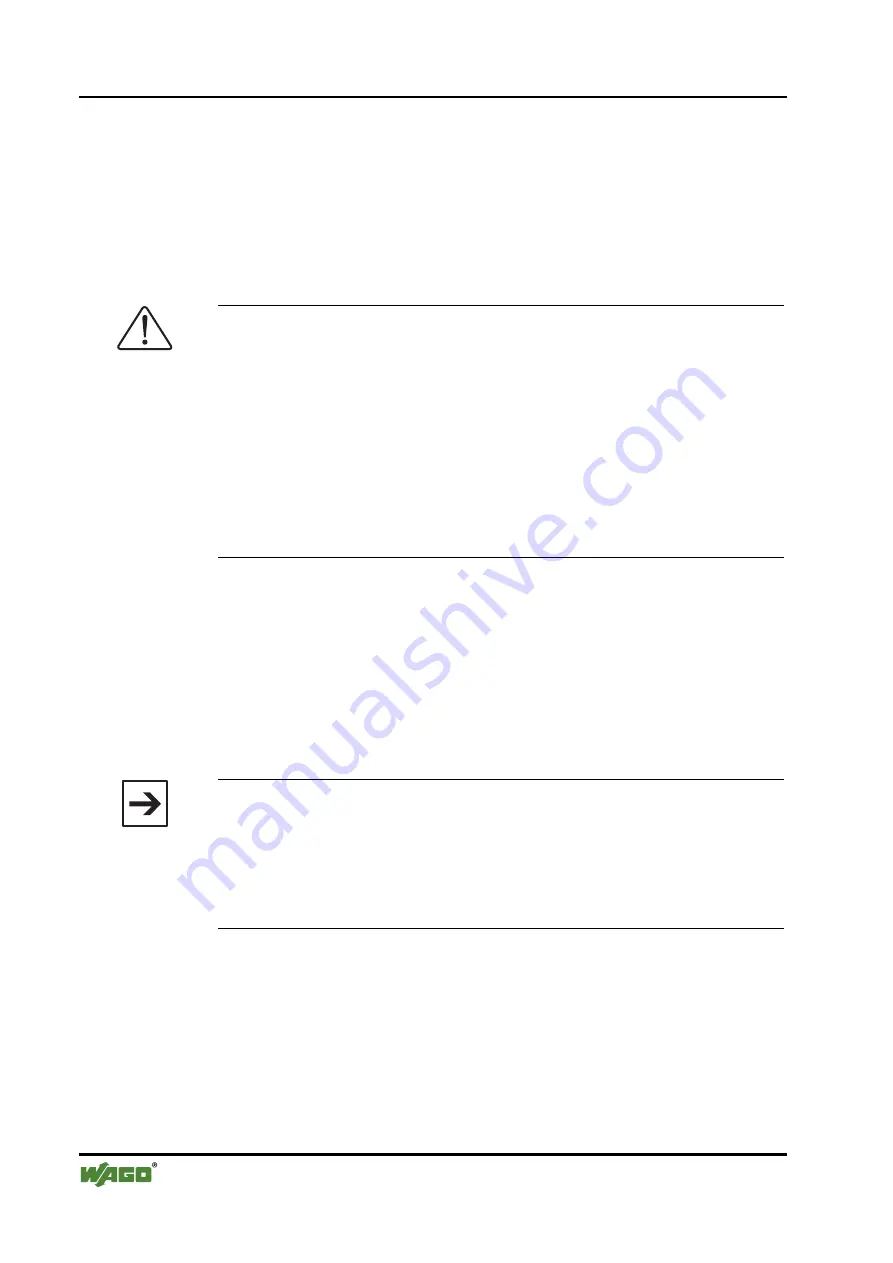
36
•
The WAGO-I/O-SYSTEM 750
Shielding (screening)
WAGO-I/O-SYSTEM 750
DeviceNet
2.8 Shielding (screening)
2.8.1 General
The shielding of the data and signal conductors reduces the electromagnetic
influences thereby increasing the signal quality. Measurement errors, data
transmission errors and even disturbances caused by overvoltage can thus be
avoided.
Attention
Constant shielding is absolutely required in order to ensure the technical
specifications in terms of the measurement accuracy.
The data and signal conductors should be laid separately from all high-
voltage cables.
The cable shield is to be laid over a large-scale surface onto the earth poten-
tial. With this, incoming disturbances can be easily diverted.
The shielding should be placed over the entrance of the cabinet or housing in
order to already repel disturbances at the entrance.
2.8.2 Bus Conductors
The shielding of the bus conductor is described in the relevant assembly
guideline of the bus system.
2.8.3 Signal Conductors
The bus terminals for analogue signals as well as some interface bus terminals
possess connection terminals for the shield.
Note
Improved shielding can be achieved if the shield is previously placed over a
large-scale surface. For this, we recommend the use of the WAGO shield
connecting system for example.
This is particularly recommendable for systems with large-scale expansions
where it cannot be ruled out that differential currents are flowing or high
pulse currents, i. e. activated by atmospheric discharge, may appear.