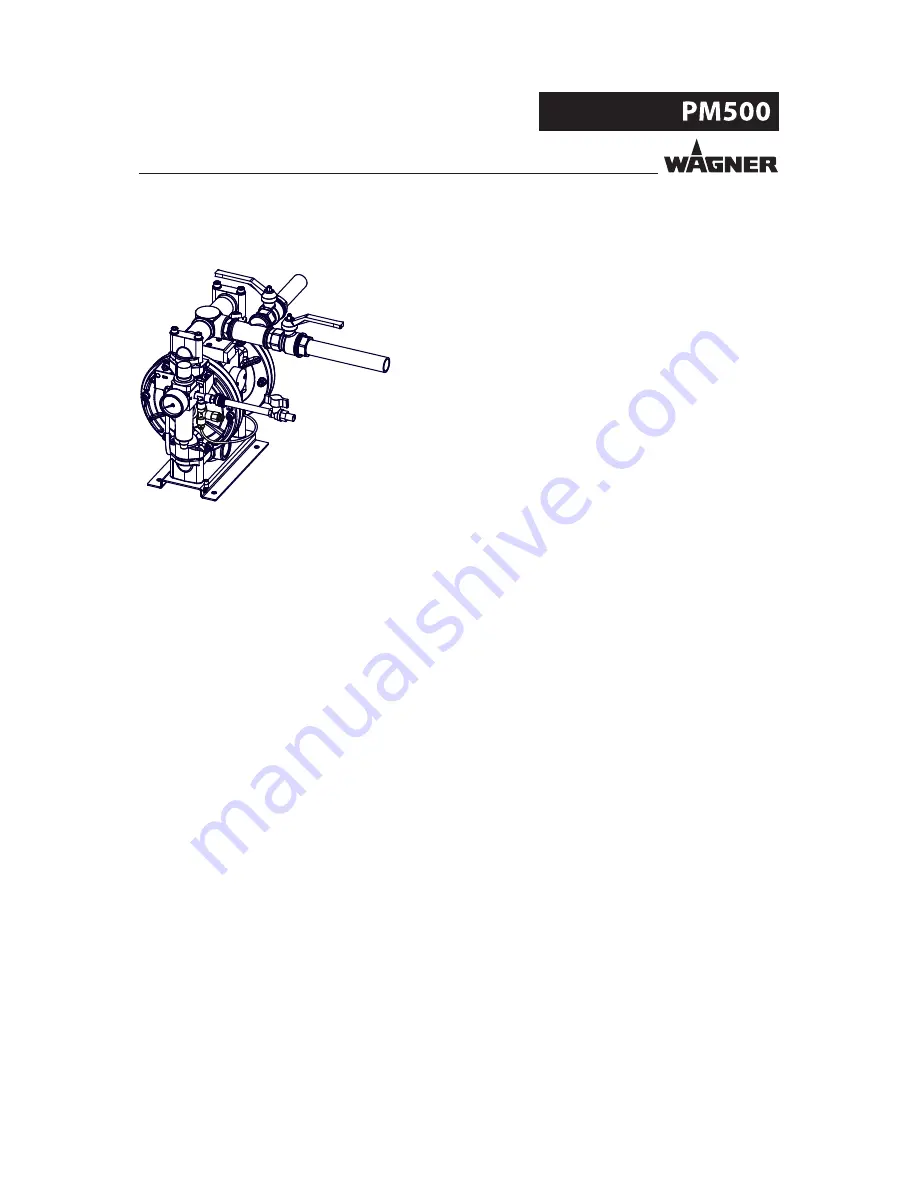
31
B_04212
OPERATING MANUAL
VERSION 01/2013
ORDER NUMBER DOC 2335747
Close the return valve, if installed.
Let the solvent fl ow through the pump for 2 or 3 minutes.
6.5.3
UNIT PRESSURE TIGHTNESS TEST
Close the material delivery valve, once the pump is primed.
Gradually increase the pressure until reaching the maximum allowed value for the pump
and the devices connected to it. Ensure that no air or liquid escapes.
Opened
Opened
Closed
Delivery
Discharge
(Return line)
Air
Содержание PM500
Страница 2: ......
Страница 51: ......
Страница 52: ...Order No 2335747 People s Republic of China Phone Telefax Germany Phone Telefax E mail ...