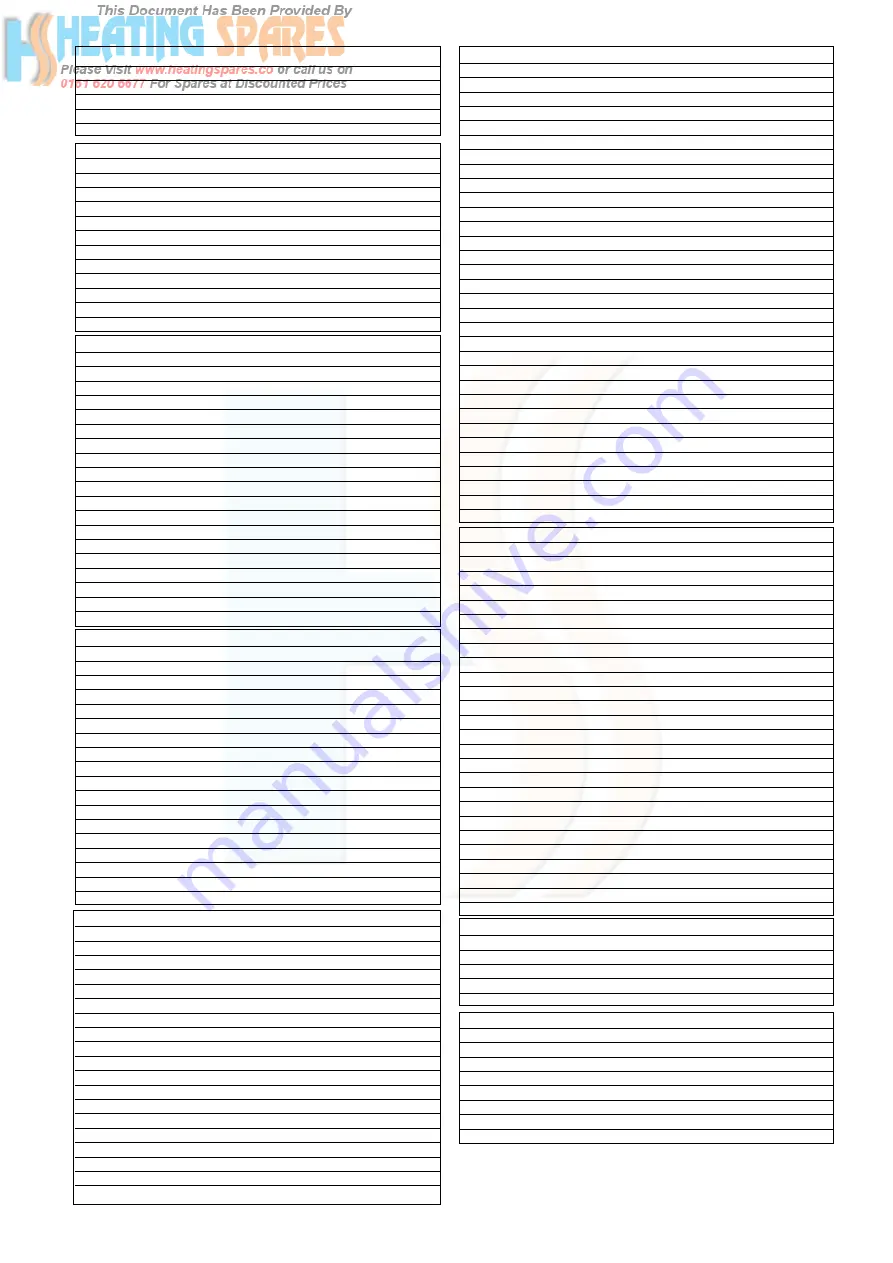
Supplied By www.heating spares.co Tel. 0161 620 6677
2
Contents
Design principles and operating sequence
Page
1.1
Principle components
4
1.2
Mode of operation (at rest)
4
1.3
Mode of operation (heating)
4
1.4
Mode of operation (DHW)
4
1.5
Safety devices
4
Technical data
Page
2.1
Central heating
5
2.2
Domestic hot water
5
2.3
Gas pressure
5
2.4
Expansion vessel
5
2.5
Dimensions
5
2.6
Clearances
5
2.7
Connections
5
2.8
Electrical
5
2.9
Flue details
5
2.10
Efficiency
5
2.11
Pump duty
6
2.12
Appliance
6
General requirements (UK)
Page
3.1
Related documents
7
3.2
Location of appliance
7
3.3
Gas supply
7
3.4
Flue system
7
3.5
Air supply
7
3.6
Water circulation
7
3.6.1
Pipework
8
3.6.2
Automatic by-pass
8
3.6.3
Drain cocks
8
3.6.4
Air release points
8
3.6.5
Expansion vessel
8
3.6.6
Filling point
8
3.6.7
Low pressure sealed system
8
3.6.8
Frequent filling
8
3.7
Electrical supply
8
3.8
Showers
8
3.9
Mounting on a combustible surface
9
3.10
Timber framed building
9
3.11
Inhibitors
9
Installation
Page
4.1
Delivery
10
4.2
Contents
10
4.3
Unpacking
10
4.4
Preparation for mounting the appliance
10
4.5
Fitting the flue
10
4.5.1
Concentric horizontal flue
10
4.5.2
Concentric vertical flue
11
4.6
Connecting the gas and water
12
4.6.1
Gas
12
4.6.2
Flow and return
12
4.6.3
Cold water inlet
12
4.6.4
Hot water outlet
12
4.6.5
Safety valve
12
4.6.6
Condense pipe
12
4.7
Electrical connections
13
4.7.1
Casing removal
13
4.7.2
Appliance terminal block
13
4.7.3
Connecting the mains (230V) input
13
Commissioning
Page
5.1
Gas supply installation
14
5.2
The heating system
14
5.3
Initial filling of the system
14
5.4
Initial flushing
14
5.5
Filling the hot water system
14
5.6
Pre-operation checks
14
5.7
Initial lighting
14
5.7.1
Checking burner pressures
14
5.8
Final flushing of the heating system
14
5.8.1
Inhibitors
14
5.9
Setting the boiler operating temperature
14
5.9.1
Setting the DHW temperature
15
5.10
Setting the system design pressure
15
5.11
Regulating the hot water
15
5.11.1 Changing the flow restrictor
15
5.11.2 Regulating the central heating system
15
5.12
Final checks
15
5.13
Instructing the user
15
5.14
Technical assistance
15
Servicing instructions
Page
6.1
General
16
6.2
Routine annual servicing
16
6.3
Replacement of components
16
6.4
Component removal procedure
16
6.5
Pump assembly
16
6.6
Safety valve
16
6.7
Automatic air release valve
16
6.8
Water pressure switch
17
6.9
Pressure gauge
17
6.10
Primary thermistor
17
6.11
High limit thermostat
17
6.12
PCB
17
6.13
Gas valve
17
6.14
Integral time switch
18
6.15
Electrode, burner thermostat, burner & injectors
18
6.16
Flue fan
18
6.17
Main heat exchanger
19
6.18
Air pressure switch
19
6.19
Flow restrictor
19
6.20
DHW flow switch
19
6.21
DHW heat exchanger
20
6.22
Valve actuator
20
6.23
Divertor valve cartridge
20
6.24
DHW thermistor
20
6.25
Automatic by-pass
20
6.26
DHW non-return valve
20
6.27
Expansion vessel
20
6.27.1 Expansion vessel removal
(with sufficient clearance above)
20
6.27.2 Expansion vessel removal
(with insufficient clearance above)
21
6.28.1 Latent heat collector
21
6.28.2 Dismantling the latent heat collector
21
6.29
Condense trap removal
21
Checks, adjustments and fault finding
page
7.1
Checking appliance operation
22
7.2
Appliance mode of operation
22
7.2.1
Selector switch in the OFF position
22
7.2.2
Selector switch in the hot water only position
22
7.2.3
Selector switch in the heating & hot water position
22
7.2.4
Appliance functions
22
7.2.5
DHW mode
22
7.2.6
Heating mode
23
7.3
Checking & adjusting burner pressure
24
7.3.1
Setting the maximum burner pressure
24
7.3.2
Setting the minimum burner pressure
24
7.3.3
Setting the minimum CH output
24
7.4
Combustion analysis test
24
7.5
Checking the expansion vessel
25
7.6
External faults
25
7.6.1
Installation faults
25
7.7
Electrical checks
25
7.7.1
Earth continuity test
25
7.7.2
Short circuit check
25
7.7.3
Polarity check
25
7.7.4
Reversed polarity or supply fault
26
7.7.5
Resistance to earth check
26
7.8
Fault finding
26
7.8.1
Replacing the main PCB
26
7.9
Fault codes
26
7.10
Fault finding
27-32
Wiring diagrams
Page
8.1
External wiring
33
8.2
Typical control applications
33
8.3
Room thermostat
33
8.4
Other controls
33
Functional diagram
34
L.P.G. instructions
Page
10.1
Related documents
35
10.2
Technical data
35
10.3
Converting the appliance gas supply
35
10.4
Gas supply
35
10.5
Gas supply installation
35
10.6
Checking & adjusting burner pressure
35
10.6.1 Setting the maximum burner pressure
35
10.6.2 Setting the minimum burner pressure
35