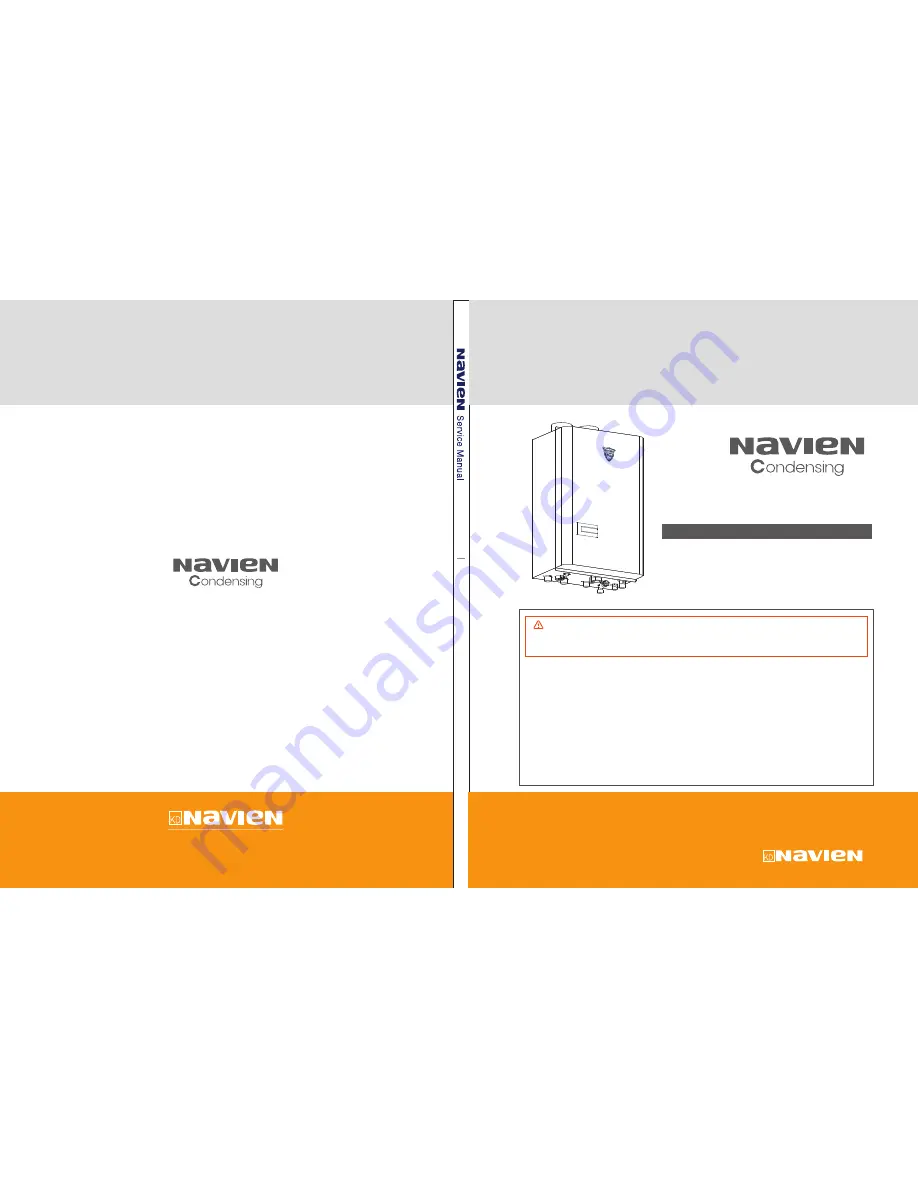
CH-180 CH-210 CH-240
CH-240 ASME
Combination Water Heater
/ Heating Boiler
MODEL
CH
Combination Water Heater / Heating Boiler
Combination Water Heater / Heating Boiler
Ver. 1.00
Service Manual Service Manual
Service Manual
Navien America, Inc.
20 Goodyear lrvine, CA 92618
TEL +949-420-0420 FAX +949-420-0430
www.naviennamerica.com
1
st
Edition - July 2010
No. 20A-GT-002
-
Do not store or use gasoline or other flammable vapors and liquids in the vicinity
of this or any other appliance.
-
WHAT TO DO IF YOU SMELL GAS
-
Installation and service must be performed by a qualified installer,
service agency or the gas supplier.
WARNING
If the information in this manual is not followed exactly, a fire or explosion may result causing
property damage, personal injury or loss of life.
●
Do not try to light any appliance.
●
Do not touch any electrical switch; do not use any phone in your building.
●
Immediately call your gas supplier from a neighbor’s phone. Follow the gas supplier’s
instructions.
●
If you cannot reach your gas supplier, call the fire department.
Summary of Contents for CH-180
Page 2: ......
Page 31: ...29 4 4 Wiring Diagram Navien America Inc 2010 CH series service Manual Version 1 0...
Page 143: ...Navien America Inc 2010 CH series service Manual 141 Version 1 0 9 2 Burner Disassemble G...
Page 146: ...Navien America Inc 2010 CH series service Manual 144 Version 1 0 9 3 Water Way Disassemble...
Page 152: ...Navien America Inc 2010 CH series service Manual 150 Version 1 0 Memo...
Page 153: ...Navien America Inc 2010 CH series service Manual 151 Version 1 0 Memo...
Page 154: ...Navien America Inc 2010 CH series service Manual 152 Version 1 0 Memo...
Page 155: ......