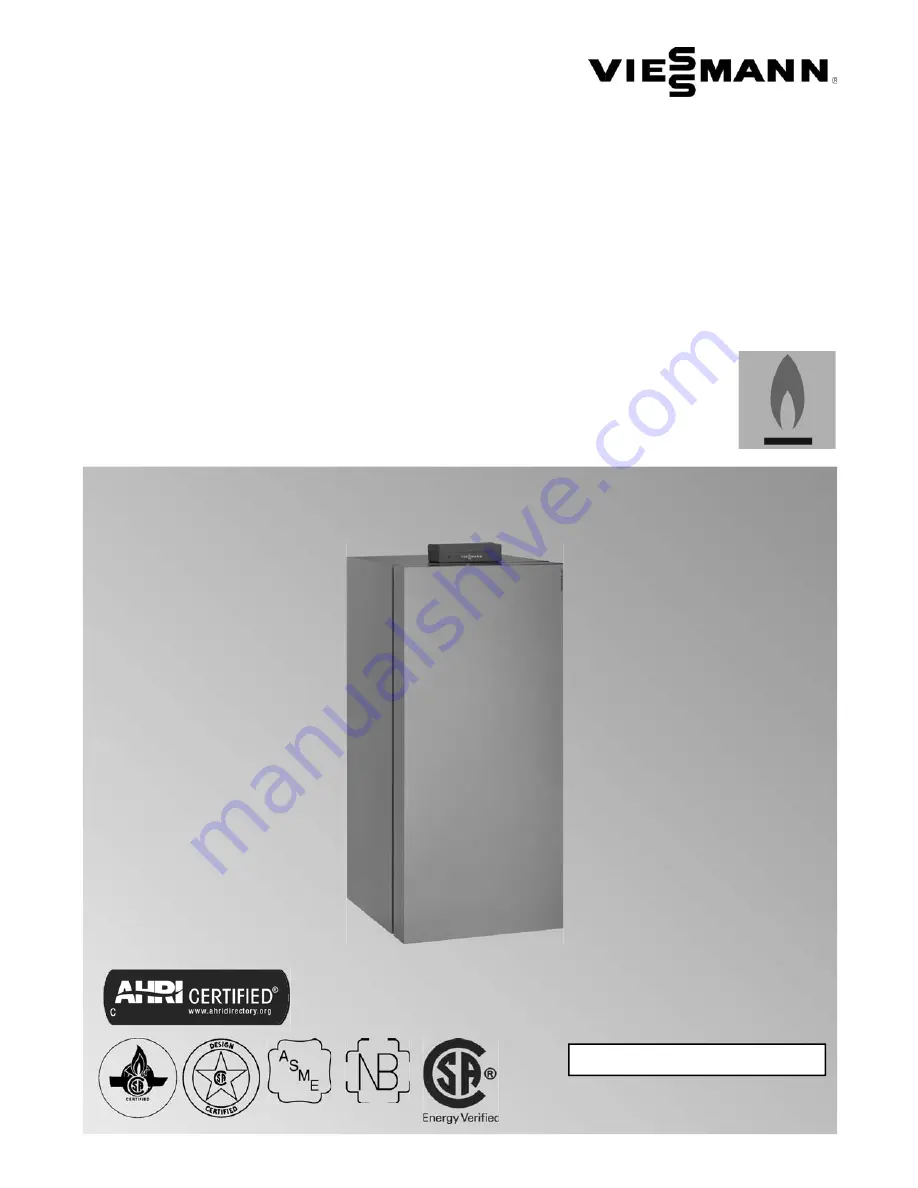
for use by heating contractor
Please file in Service Binder
5673 649 -18 10/2019
Service Instructions
VITOCROSSAL 300
Vitocrossal 300 CU3A
Models 26, 35, 45, 57, 94, 125, 160, 199
Floor mounted, gas-fired condensing boiler with MatriX gas burner and Lambda Pro control
For operation with natural gas and liquid propane gas
Heating input 19 to 199 MBH
5.6 to 58 kW
Read and save these instructions
for future reference.
Product may not be exactly as shown
IMPORTANT
H