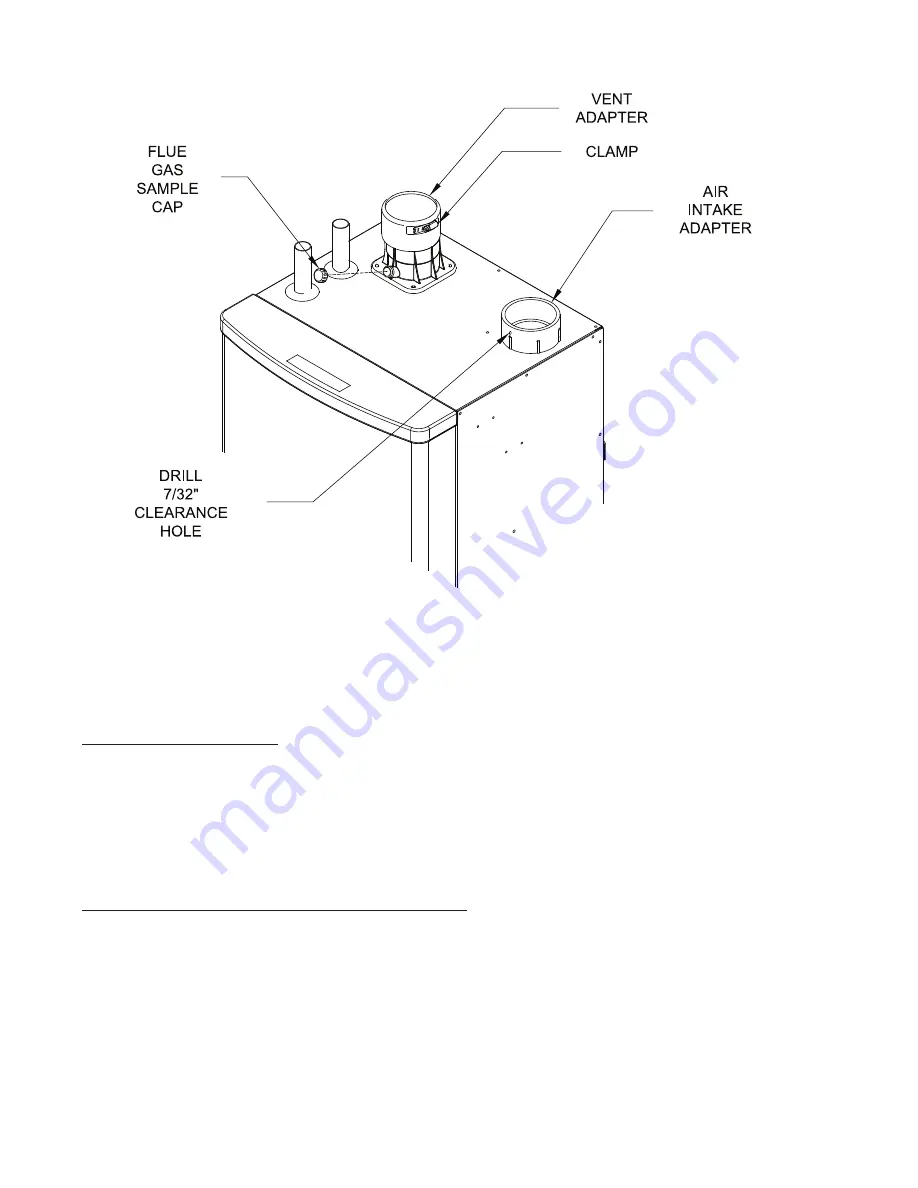
44
VII. Venting
E. Assembly of CPVC/PVC Vent Systems (continued)
Figure 7.26: Vent Connections and Flue Gas Sample Cap Location
h. Maintain the clearances from the vent pipe outlined in Part VII-A of this manual. If exiting the exterior wall using PVC
pipe, use half of an appropriately sized wall thimble (or a sheet metal plate) on the exterior of the building, to provide a
weather tight seal while maintaining the proper clearance in the wall penetration. Seal the joint between the pipe and the
wall plate using RTV applied on the exterior side of the wall. This sealant must not restrain the expansion of the vent pipe.
2. Installation of Air Intake System - Start assembly of the PVC air intake system at the boiler. Assembly of the air intake
system is done in the same manner as the vent system except as follows:
a. Drill a 7/32" clearance hole into the front side of the air intake adapter. Insert the first piece of PVC air intake pipe
into the air intake connection and drill a 1/8" tap hole into the PVC which lines up with the 7/32" clearance hole and
secure them together with a #10 x 1" sheet metal screw. Seal the joint between the intake pipe and the adaptor with
RTV.
b. All intake piping may be PVC.
c. There is a 0" minimum clearance between the air intake piping and all types of construction.
d. To the extent possible, pitch horizontal air intake piping towards the outdoors.
3. Installation of Horizontal Fitting Terminals (Terminal Option A):
a. See Figure 7.27 for proper orientation of twin pipe horizontal terminals. Outer edge of both terminals must be within 10"
from wall surface. (Figure 7.6)
b. If desired, the terminals can be attached to the end of the vent and/or intake pipes with field supplied stainless steel screws
so that they can be later removed for cleaning and inspection. If this is done, drill a clearance hole in the coupling or
elbow and a tap hole in the end of the vent/intake pipes to accept these screws.
c. If these terminals are installed on snorkels, assemble the snorkels as shown in Figure 7.12. Brace the vertical run of
piping on the building exterior as required.
Содержание Raptor RPTR155
Страница 1: ...1 ...
Страница 13: ...13 Figure 5 1 Wall Layout Mounting Hole Location V Mounting The Boiler continued ...
Страница 14: ...14 Figure 5 2 Boiler Mounting Bracket Installation Boiler Wall Mounting V Mounting The Boiler continued ...
Страница 87: ...87 Figure 10 5 Internal Wiring Ladder Diagram X Wiring continued ...
Страница 88: ...88 X Wiring continued ...
Страница 97: ...97 Operating Instructions XI Start Up and Checkout continued ...
Страница 142: ...142 XV Repair Parts continued 3A 3B 3C 3D 3F 3E 3G 3H 3O 3P 3Q 3R 3J 3K 3I 3M 3N 3L All Models ...
Страница 148: ...148 XV Repair Parts continued 6D 6B 6A 6E 6I 6G 6L 6N 6H 6C 6K 6M 6C 6C 6J 6J 6F All Models ...
Страница 172: ...172 ...