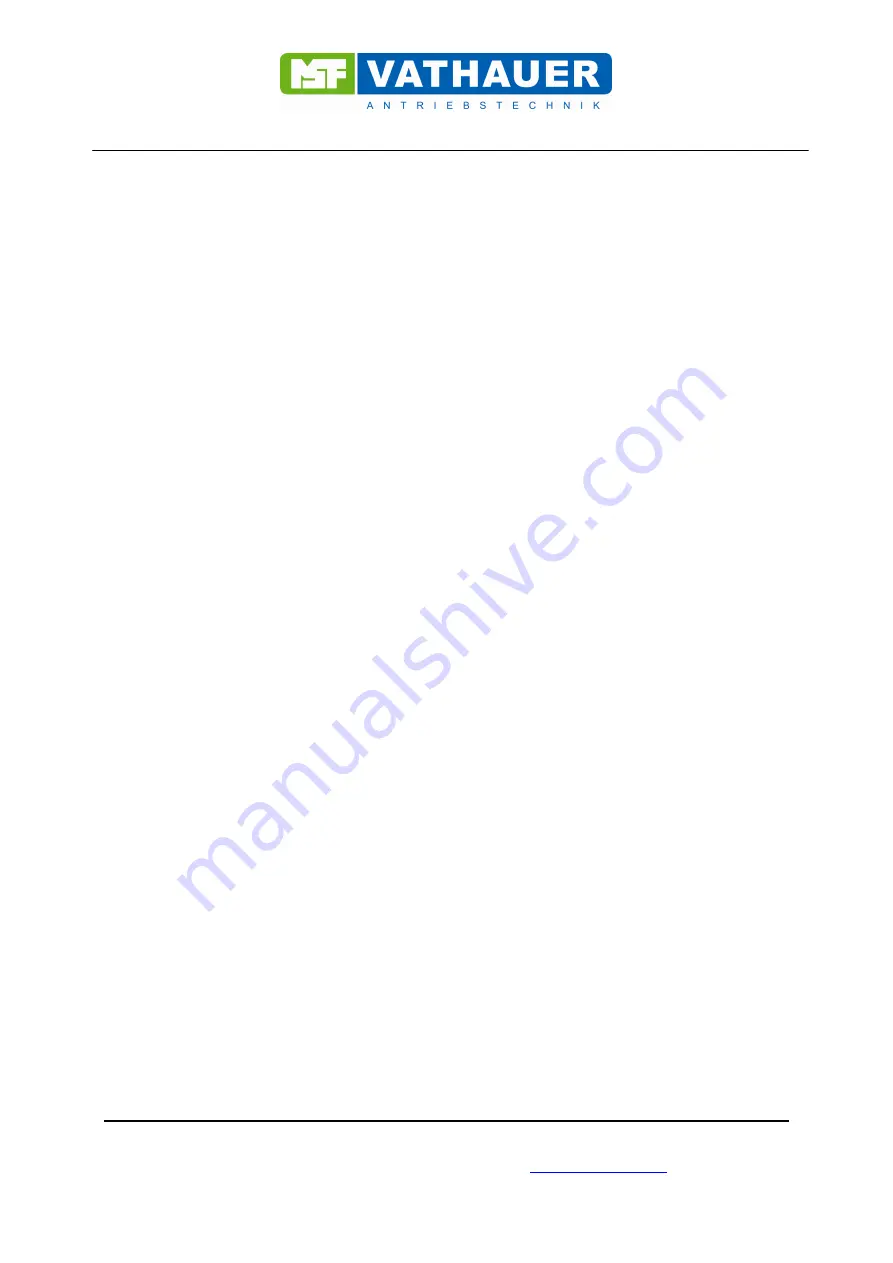
User Manual Frequency Inverter Vector Basic
MSF – Vathauer Antriebstechnik GmbH & Co KG
Tel: +49 (0) 5231 – 63030
Am Hessentuch 6-8
Fax: +49 (0) 5231-66856
32758 Detmold
Email:
Web: www.msf-technik.de
19 / 25
7. In- and Outputs
Terminals 3 and 4 are digital inputs and are assigned for the following functions:
Terminal 3: Start / Stop
Terminal 4: Left / Right cw/ccw
7.1. Start/Stop
The activation leads to the release of the pulses. After additionally the inverter has been enabled
(buttons "ON / OFF") than this function performs the acceleration of the motor with the set-up time until
reaching the set point with the said rotation.
The inactivation effects the running down with the set running down ramp down to the standstill.
7.2. Clockwise/Counter clockwise
In unconnected state the motor is always running right. When activating this function the motor is
running counter clockwise. When changing from clockwise to counter clockwise rotation during
operation, the motor moves in the current direction of the running down ramp to 0 Hz and accelerates
after at the acceleration ramp in the opposite direction of rotation.
8. Motor protection
Despite a high-grade sine modulation, additional losses occur in the motor in powering standard 3-
phase asynchronous motors. Even at nominal revolutions, these losses require a power reduction the
extent on which essentially depends on the exploitation of the temperature limits of the motor.
For drives of a square counter-torque (e.g. fans) and 50 Hz as maximum rotating field frequency, the
imposed power reduction is usually around 0 - 10%.
For drives of a constant counter-torque (compressors, conveyer belts, etc.), the power reduction has
to be selected accordingly larger, depending on the range of the adjustment.
To guarantee the safe operation of a motor in the adjustment range, the stationary load torque must lie
below the continuous operating characteristic of the motor to guarantee a safe operation of a motor.
During operation and starting, the drive will momentarily be in a position to submit or corresponding to
the current limitation of the inverter. The setting of the voltage increase (static Boost) essentially
determines the maximum torque below 10 Hz. During a continuous operation, an excessive high boost
setting for the lower rotating field frequency range (up to 15 Hz) can cause the motor to overheat
A comprehensive thermal protection of the self-cooling motor can be achieved by means of a
temperature sensor (e.g. PTC thermistor or thermal time-delay switch) built into the motor.
For revolutions above 120% of the nominal speed, the performance of the motor has to be checked.