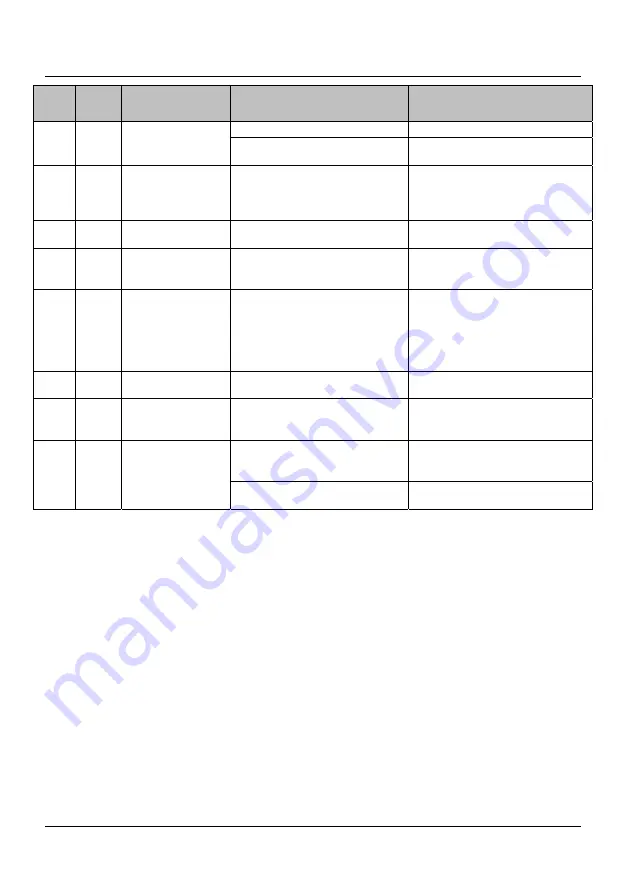
high performance crane special inverter User Manual
38
Chapter 6 Crane specialinverter faults and troubleshooting
Fault
num
ber
Fault
Code
Fault
Description
Possible Causes
Countermeasure
nput failure
Check whether there is phase loss
Output failure
Check whether there are phase loss
or short circuit
39
E.tPF
Torque verification
failure
output torque does not reach the
brake open torque
Check the torque verify value if
normal
Check the validation failure
detection time if too short
40
E.bLF
Brake failure
With brake release command but
did not received open feedback
Check the brake for malfunction
41
E.bEF
Brake set failure
With brake engaged command
but did not received a close
feedback
Check the brake for malfunction
42
E.oPF
Overspeed failure
Speed exceed the setting
maximum speed
Check if the given is normal
Check if the parameter settings are too
small
Check if the encoder is normal
Check if the inverter is running
normally
43
E.PbF
Stall failure
The running speed of the inverter is
deviated from the actual speed.
Check if the machine is faulty
44
E.0cF
Zero current failure
Motor output current is less than zero
current detection value
Check if the motor cable is connected
properly
Check if the setting value is too large
63
−LU−
Power under voltage
The power supply voltage is lower
than the minimum operating voltage
of the inverter
Check input power supply
Abnormal internal switching power
supply
Seek for technical support
6.2Hoisting equipments causes of common failures and analysis
◆
Slide down when start, low torque is insufficient:
1) Confirm inverter power if correctly selected , inverter should be selected according to the motor
rated current, require inverter rated current to amplify one power level based on corresponding motor
rated current. Because it is crane applications, the inverter and the motor are required to leave some
margin;
2) Ensure the load weight in the range of rated weigh;
3) Ensure there is no mechanical problem;
4) Do not switch direction during running.
5) If using the traditional brake control, need to check brake control sequence selection if correct ,
when brake open the inverter output torque if adequate;
6) If it is conical motor, need to set the frequency of brake open bigger, so that current is enough to
open the brake;
7) Check already set the motor parameters and finished auto tuning;
8) Improve initial frequency of inverter;
9) If using open-loop control mode P0.03=0 then increase the value of low-speed torque; if using
Содержание V5 Series
Страница 10: ......