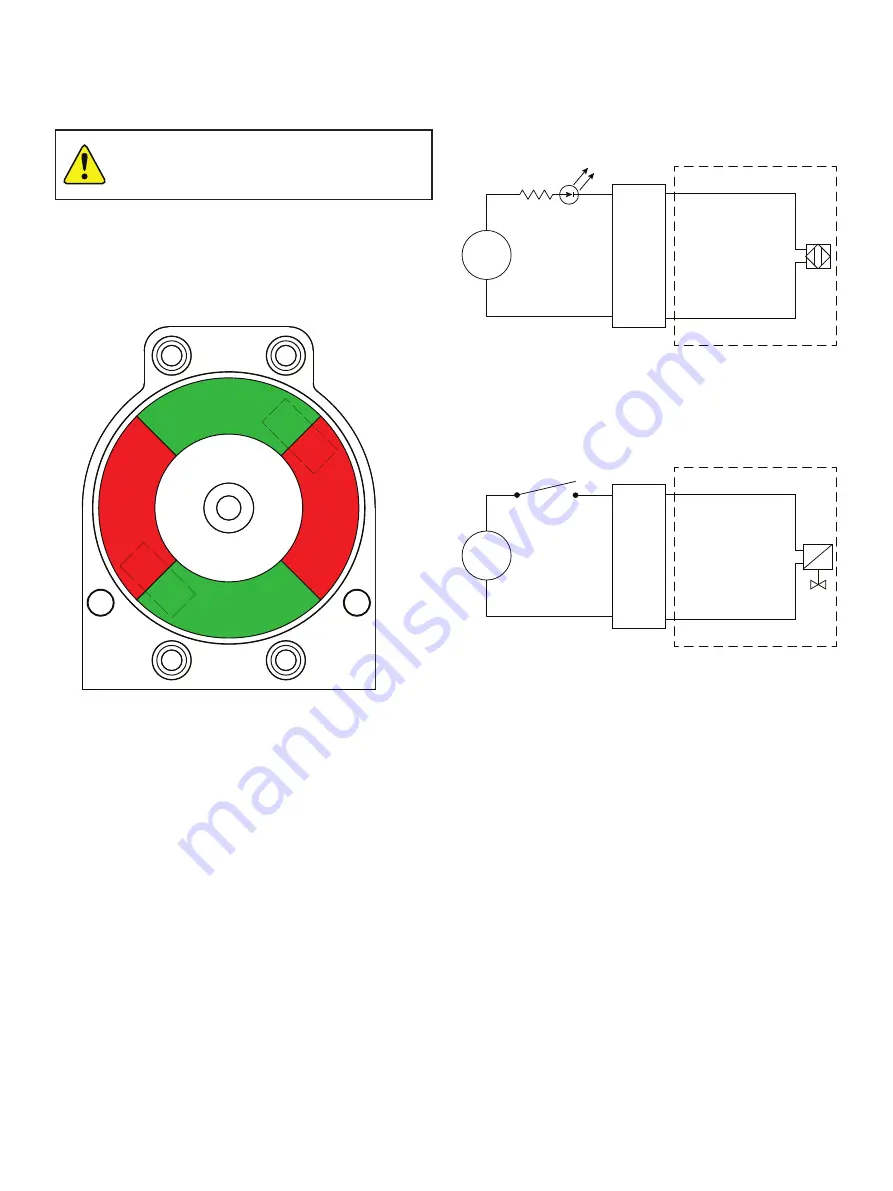
4.1.4 NAMUR SENSOR (45S) CONTINUED
Typical basic intrinsically safe circuits
NAMUR sensor circuit
Solenoid circuit
** Barrier off state (target off): current in NAMUR sensor circuit >2.1 mA
Barrier on state (target on): current in NAMUR sensor circuit <1.0 mA
power
source
Hazardous area
NAMUR
repeater
barrier
24 VDC
computer input
8 VDC
I = 0.5mA to 5.0mA**
NAMUR sensor
power
source
Hazardous area
solenoid
barrier
24 VDC
computer output
solenoid coil
Bench test procedure and sensor setting instructions
1.
Connect 24 VDC + to the CLOSED (+) and OPEN (+) terminals.
2. Connect 24 VDC - to the CLOSED (-) and OPEN (-) terminals.
3. Attach indicator such that the closed quadrants will face out when
in the closed position. This figure shows a Red Closed visual
indicator in the closed position.
Ma
gne
t
Ma
gn
et
Ma
gne
t
Green
R
ed
G
ree
n
Re
d
4. Save set-points:
a.
Operate actuator to the closed position.
b.
Press and hold SET CLOSED button until closed LED is
OFF (2 seconds). Release button.
c.
Operate actuator to the open position.
d.
Press and hold SET OPEN button until the open LED is OFF
(2 seconds). Release button.
NOTE: If red or green LEDs flash when trying to set the set-point,
the magnet is too far away from the sensing element. Adjust Visual
Indicator drum to bring the magnet slightly closer to the sensing unit
and try again.
5. Setpoints are retained even after power is removed.
6. To electrically test solenoid output, apply power to the
SOL PWR (+) and SOL PWR (-) terminals.
Note
If using only one of the sensors for valve position feedback, either
sensor may be used independently.
Caution:
Performing this procedure will cause the
sensor inputs to change state. Performing this procedure
is not recommended during a live process.
17
EC70EN - 6/2022 | Stonel product publication 105509revA