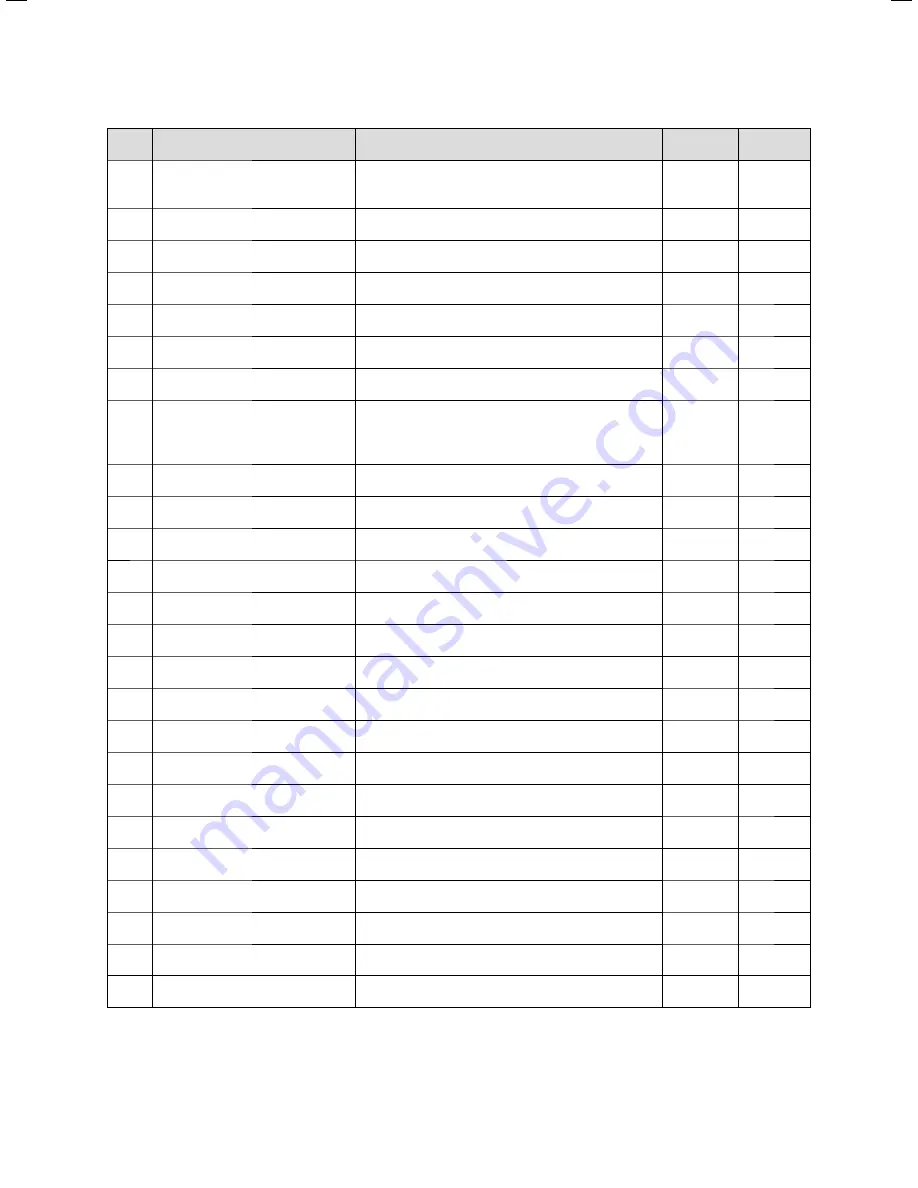
Adapting the boiler to the heating installation
44
Installation and maintenance instructions ecoTEC 0020173113_01
11
Code
Parameters
Adjustable values
Factory
setting
Your own
setting
D.000
Heating partial load
Adjustable heating partial load in kW
Auto: Boiler automatically adjusts max. partial load to cur-
rent system demand
Auto
D.001
Overrun time of internal pump for
heating mode
1 - 60 min
5 min
D.002
Max. burner anti-cycling time heating
at 20 °C flow temperature
2 - 60 min
20 min
D.003
Outlet temp. actual value
in °C
Not adjusta-
ble
D.004
Measured value of hot water sensor
Not relevant
Not adjusta-
ble
D.005
Flow temperature target value (or
return target value)
In °C, max. of the value set in d.71, limited by an eBUS con-
troller if connected)
Not adjusta-
ble
D.006
Hot water temperature target value
(VUW boilers only)
35 to 65 °C
Not adjusta-
ble
D.007
Warm start temperature target value
(only with VUW boilers)
Cylinder temperature target value
(only with VU boilers)
40 to 65 °C
15 °C frost protection, then 40 to 70 °C;
(max. temperature can be adjusted under D.020)
Not adjusta-
ble
D.008
Room thermostat at terminal RT
Room thermostat open (no heat requirement)
Room thermostat closed (heat requirement)
Not adjusta-
ble
D.009
Target value from external eBus con-
troller
in °C
Not adjusta-
ble
D.010
Status of internal pump
1 = on, 0 = off
Not adjusta-
ble
D.011
Status of external heating pump
1 to 100 = on, 0 = off
Not adjusta-
ble
D.012
Status of cylinder charge pump
Not relevant
Not adjusta-
ble
D.013
Status of hot water circulation pump
Not relevant
Not adjusta-
ble
D.014
Target pump speed (high-efficiency
pump)
Not relevant
Not adjusta-
ble
D.015
Actual pump speed (high-efficiency
pump)
Not relevant
Not adjusta-
ble
D.016
Room thermostat 24 V DC open/
closed
0 = Room thermostat open (no heating mode)
1 = Room thermostat closed (heating mode)
Not adjusta-
ble
D.017
Heating flow/return regulation
changeover
0 = Flow, 1 = Return
0
D.018
Pump operating mode setting
1 = Comfort (continuously operating pump)
3 = Eco (intermittently operating pump)
3
D.019
Operating mode of 2-stage pump
Not relevant
Not adjusta-
ble
D.020
Max. setting for cylinder target value
Not relevant
Not adjusta-
ble
D.022
Hot water demand via C1/C2, internal
hot water control system
Not relevant
Not adjusta-
ble
D.023
Summer/winter operating mode (heat-
ing on/off)
1 = Heating on, 0 = Heating off (summer mode)
Not adjusta-
ble
D.025
Hot water generation enabled by eBUS
controller
1 = Yes, 0 = No
Not adjusta-
ble
D.026
Auxiliary relay control
Not relevant
Not adjusta-
ble
11.1
Diagnosis codes