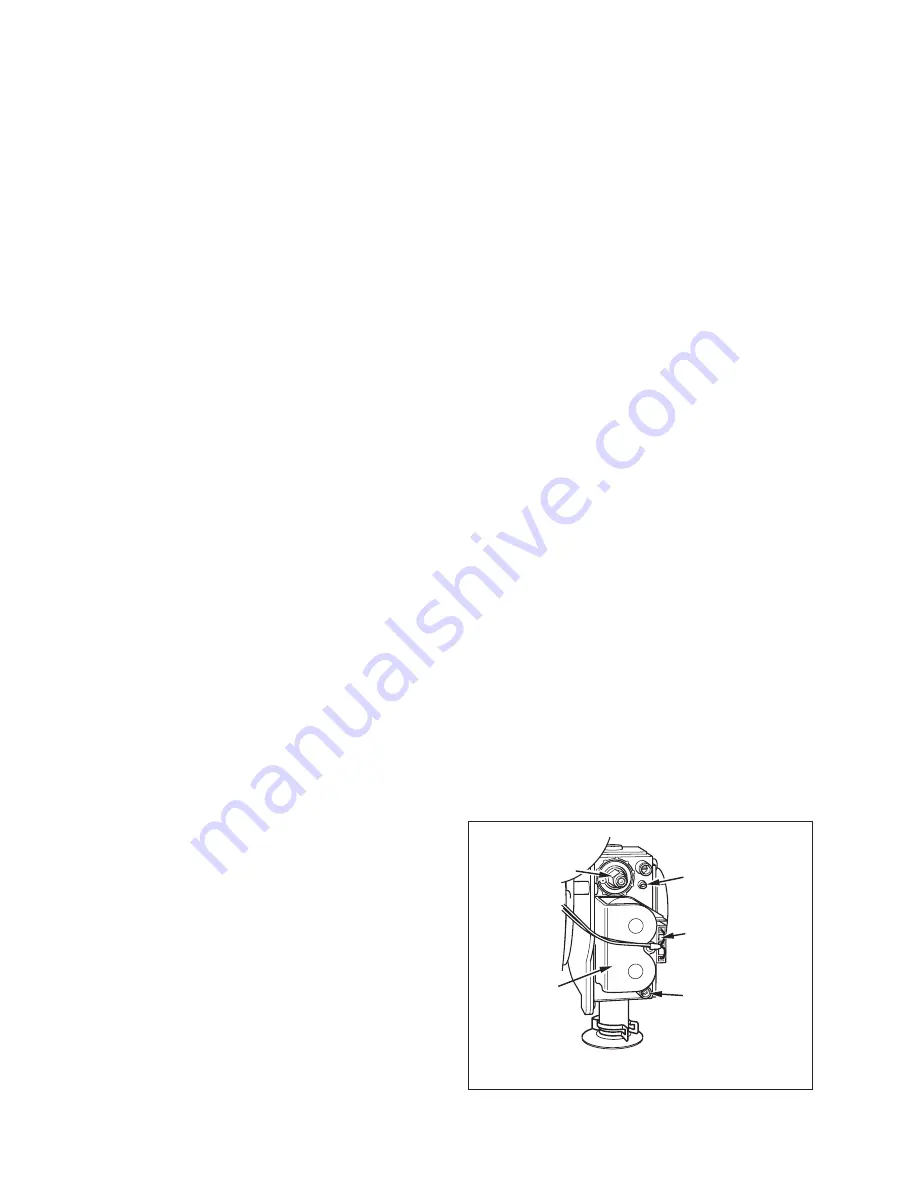
Instructions for Use, Installation and Servicing ecoMAX pro
22
13 Commissioning
The boiler will then continue to fire until the user controls
are satisfied.
Note: After the first power up the firing sequence
changes. After one minute stabilisation time the boiler
will ramp slowly to full rate rather than going immediately
to full rate, this feature is designed to cope with small
system requirements.
13.5 Testing - Gas
The boiler is supplied ready adjusted and no further gas
adjustments are necessary, however both the gas inlet
working pressure and the maximum gas rate should be
checked at least 10 minutes after the burner has lit.
The gas inlet working pressure can be checked at the
pressure test point on the gas valve (Fig 13.2.). The gas
inlet working pressure should be 20 mbar when the
boiler is firing at full rate.
After testing the inlet pressure remove the U gauge,
tighten the sealing screw and test for tightness.
The approximate gas rates are:
18 E : 2.00 m
3
/h
28 E : 3.02 m
3
/h
Note: The burner pressure cannot be measured at the
gas valve due to the fan/burner design.
Replace the inner and front casing panels.
Record appliance working gas inlet pressure (mbar) in
Benchmark Installation, Commissioning and Service log
book.
13.6 Testing - Heating System
Check that all remote controls are calling for heat. The
boiler will fire automatically. Fully open all radiator
valves, flow control valve ‘A’ and bypass valve ‘B’ if
fitted, see Fig. 5.4.
Balance the radiators as required and if fitted adjust
valve ‘A’ to give the required system differential. Turn off
all radiators that can be shut off by the user and check
to see if less than the maximum differential allowed of 20
°C can be achieved across flow and return.
Allow the system to reach maximum temperature then
switch off the boiler by isolating from the electrical
supply.
Drain the entire system rapidly whilst hot, using the drain
tap at the lowest part of the system. Fill and vent the
system as described previously.
Lock or remove the handles from controls valve ‘A’ and
bypass valve ‘B’ to prevent unauthorised adjustment.
13.7 User Controls and Options
The mains/reset switch is used to restart the boiler after
a fault condition has occurred, i.e. ignition failure.
The user display (see section 3.3) allows the user to set
the desired central heating temperature.
13.8 Temperature Display
The boiler shows the operating temperature of the unit.
13.9 Pump Exercise Programme
After a power cut or every 24 hour in frost setting/
summer mode the pump will run for one minute to
prevent it from sticking. This will also occur during
normal operating if there is no demand for more than 24
hours.
13.10 Handover to user
Instruct and demonstrate the lighting procedure and
advise the user on the safe and efficient operation of the
boiler. Instruct on and demonstrate the operation of any
heating system controls.
Advise that to ensure the continued efficient and safe
operation of the boiler it is recommended that it is
checked and serviced at regular intervals. The frequency
of servicing will depend upon the installation conditions
and usage, but in general, once a year should be
adequate.
Draw attention, if applicable, to the current issue of the
Gas Safety (Installation and Use) Regulations, Section
35, which imposes a duty of care on all persons who let
out any property containing a gas appliance.
It is the Law that any servicing is carried out by a
competent person.
Advise the user that, like all condensing boilers this
appliance will produce a plume of condensation from the
flue terminal in cool weather. This is due to the high
efficiency and hence low flue gas temperature of the
boiler.
Advise the user of the precautions necessary to prevent
damage to the system, boiler and the building, in the
event of the heating system being out of use during frost
or freezing conditions.
Advise the user that the permanent mains electrical
supply SHOULD NOT be switched off, as the built in
frost protection and pump saver program would not be
operable.
Reminder, leave these instructions and the ‘Benchmark’
logbook with the user.
PRESSURE TEST
POINT
ELECTRICAL
PLUG
GAS CONTROL
VALVE
THROTTLE
OFFSET
ADJUSTMENT
Fig 13.2
12701