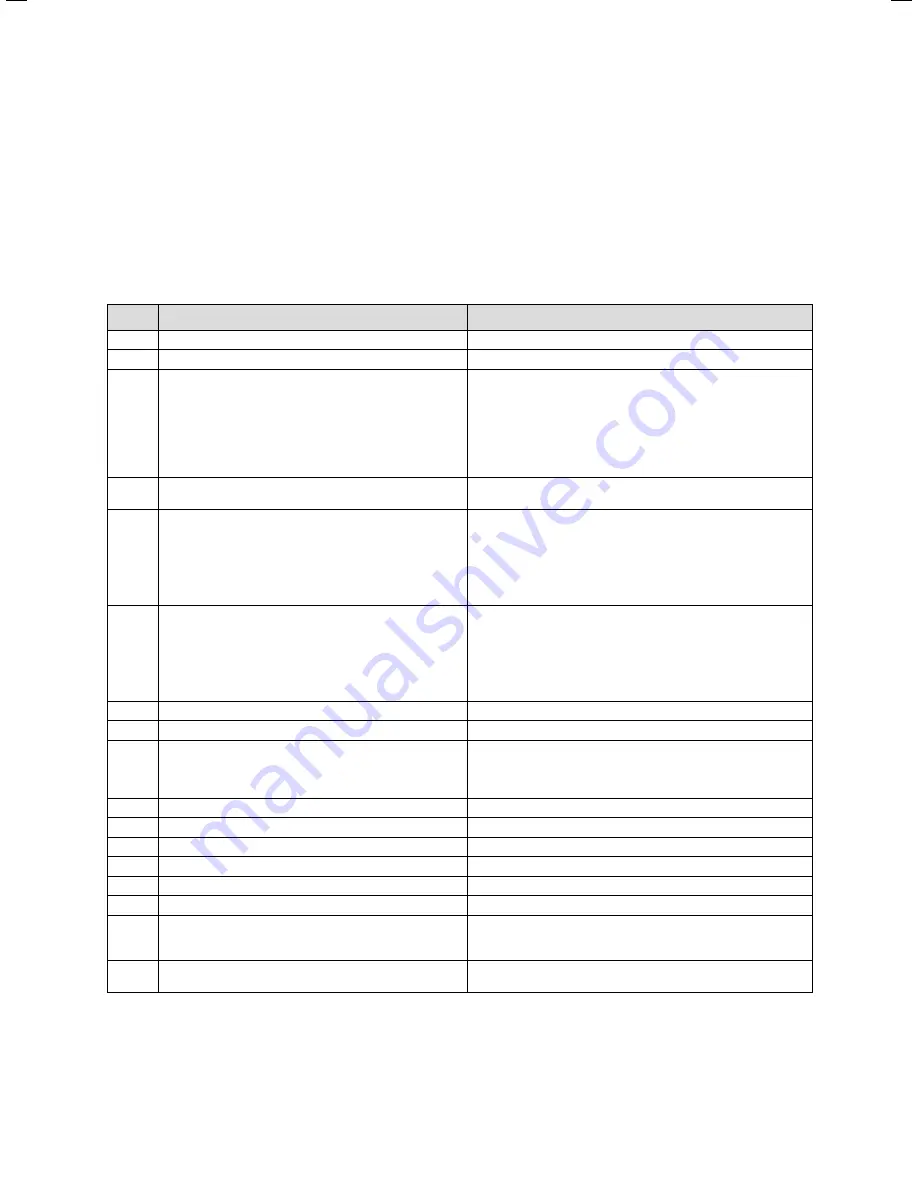
Installation and maintenance instructions ecoTEC plus 937 0020031552_06
61
Second diagnostic level
As described above in the first diagnostic level, scroll
through to the diagnosis number d.
97.
Change the displayed value to
17
(Password) and
push the button "
i
".
You are now in the second diagnostic level where all
information from the first diagnostic level (see
Table 9.2) and the second diagnostic level (see
Table 9.3) is displayed.
Display
Meaning
Displayed value/settable value
d.17
Heating flow/return regulation changeover
0 = flow, 1 = return (factory setting: 0)
d.18
Pump mode (return flow)
0 = overrun, 1 = continuous, 2 = winter (Factory setting: 0)
d.19
Operating modes of the two-speed heating pump
0 = Pre-ignition speed 1, Hot water or heating speed 2, overrun
speed 1
1 = Pre-ignition speed 1, hot water speed 2, heating speed 1,
overrrun speed 1
2 = Like 1 but speed in heating mode dependant on heating part
load d.0 (if d.0 is below 60 % of full load, then pump speed 1,
otherwise speed 2); Factory setting 2)
3 = Always speed 2
d.20
Maximum set value for external cylinder target tempera-
ture (system boilers only)
Setting range: 50 °C to 70 °C (Factory setting 65 °C)
d.27
Switching relay 1 on the accessories module
1 = Circulation pump (factory setting)
2 = Ext. Pump
3 = External cylinder charging pump
4 = Flue gas flap/extractor hood
5 = External gas valve
6 = External error message
d.28
Switching relay 2 on the accessories module
1 = Circulation pump
2 = Ext. pump (factory setting)
3 = External cylinder charging pump
4 = Flue gas flap/extractor hood
5 = External gas valve
6 = External error message
d.50
Offset for minimum fan speed
in upm/10, adjustment range: 0 to 300
d.51
Offset for maximum fan speed
in upm/10, adjustment range: -99 to 0
d.58
Activation solar pre-heat function
Setting range: 0 to 3
0 = solar post-heating deactivated (factory setting)
3 = Activation hot water target value min = 60 °C for solar pre-
heat
d.60
Number of safety temperature limiting switch-offs
Quantity
d.61
Number of unsuccessful ignitions
Number of successful ignitions in the last attempt
d.64
Average ignition duration
in seconds
d.65
maximum ignition duration
in seconds
d.68
Successful ignitions at the first attempt
Quantity
d.69
Successful ignitions at the second attempt
Quantity
d.70
Setting the diverter valve position
0 = Normal mode (factory setting)
1 = mid-position
2 = Permanent heating position
d.71
Maximum flow temperature knob setting
Adjustment range in °C 40 to 85 (Factory setting: 75)
Table 9.3 Diagnostic codes in the second level
>
>
Scroll and change values and exit diagnosis mode as
described in the first diagnosis level.
i
If you push the buttons "
i
" and "
+
" again
within 4 minutes after leaving the second
diagnosis level you will go directly to the sec-
ond diagnosis level without having to enter
the password again.
Troubleshooting 9
Содержание ecoTEC plus 937
Страница 1: ...For the heating engineer Installation and maintenance instructions GB IE ecoTEC plus 937 VUI...
Страница 74: ...74 Installation and maintenance instructions ecoTEC plus 937 0020031552_06...
Страница 76: ...76 Installation and maintenance instructions ecoTEC plus 937 0020031552_06...
Страница 77: ...Installation and maintenance instructions ecoTEC plus 937 0020031552_06 77...
Страница 78: ......
Страница 79: ......
Страница 80: ...0020031552_06 GBIE 102010 Subject to alterations...