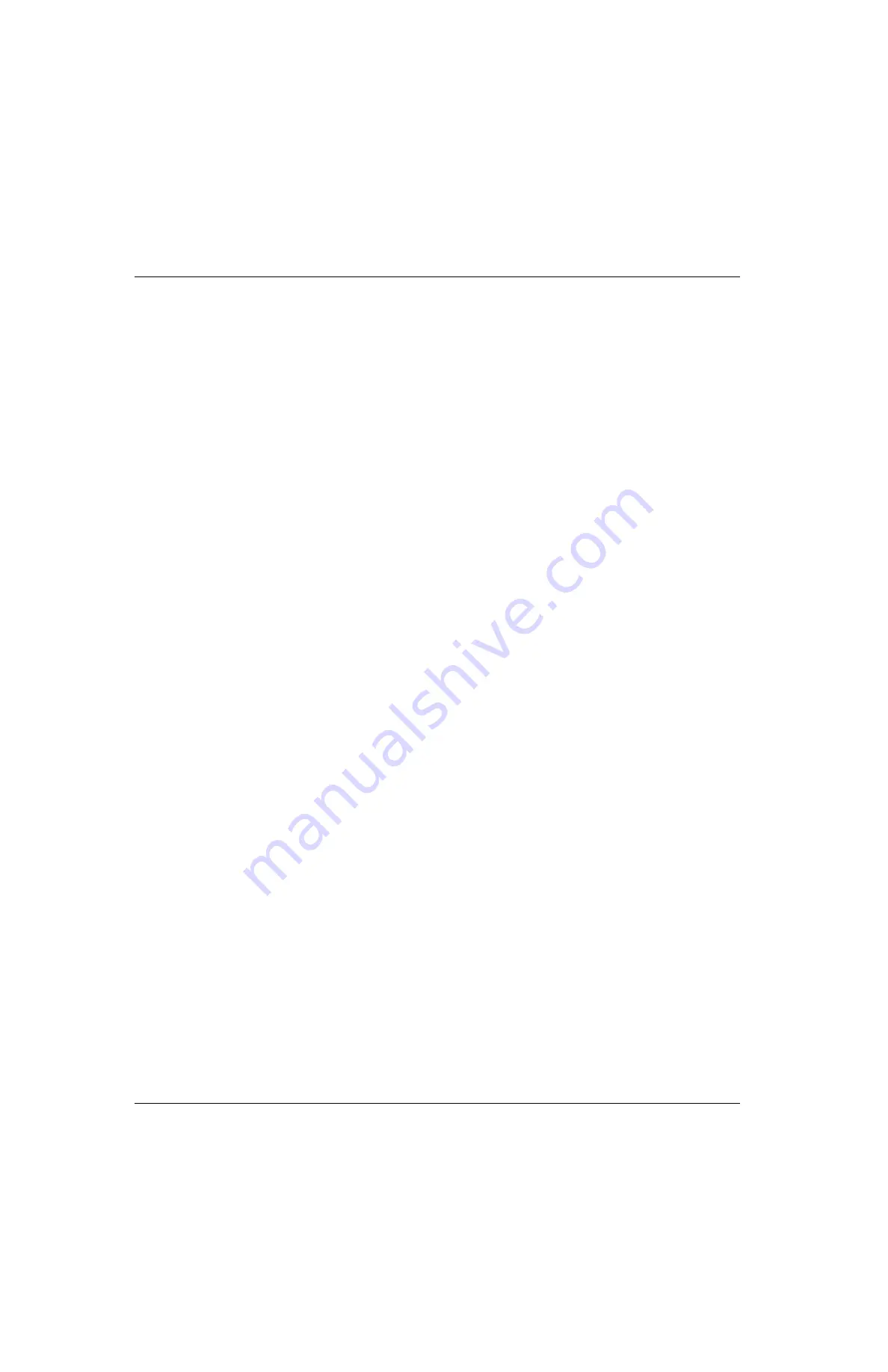
Torque Hubs
Section 2 - Service and Repair
Page 2-14
104045-021 - AB62 Work Platform - European Model
T
O R Q U E
H
U B
I
N S T A L L A T I O N
Refer to Figure 2-11 on page 2-13.
NOTE:
Torque all hardware to torques listed in the General Information section unless otherwise specified.
1. Install the torque hub using hardware previously removed.
2. Using SAE 90W weight gear lube, fill the torque hub. The torque hub must be half full.
3. Using a new gasket, install the brake.
4. Using a new gasket, install the drive motor.
5. Secure the assembly using washers and bolts.
6. Connect the hydraulic brake lines.
7. Connect the hoses to the drive motor.
8. Install the wheels.Torque the lug nuts to 257Nm (190 ft/lbs).
9. Bleed the brake lines if necessary.
10. Remove the jack stands and lower the rear end.
11. Connect the battery terminal.
12. Operate the machine and check for proper operation of the torque hub. Check the function of the brake.
D
I S A S S E M B L Y
O F
T
O R Q U E
H
U B
Refer to Figure 2-12 on page 2-17.
1. Slide the coupling (1) from the splines on the input shaft (2).
2. Position the assembly upright on the face of the spindle.
3. Remove the disengage cover (31) if necessary.
4. Remove the eight bolts (29) and the large cover (28) from the unit. The thrust washer (25) and the dis-
engage plunger (26) usually remain attached to the large cover (28) when it is removed. Remove the
thrust washer (25), disengage the plunger (26) and O-ring (27) from the large cover (28).
5. Remove the primary sun gear (24) from the end of the input shaft (2).
6. Remove the primary carrier assembly (22).
7. Remove the secondary carrier assembly (21).
8. Remove the input shaft (2) from the spindle (3). Remove the retaining rings (17), washers (18), and dis-
engage spring (19) from the input shaft (2) only if replacement is required.
9. One tab of the lock washer (15) will be engaged in the slot of the bearing nut (16); bend back to release.
Remove the bearing nut (16), lock washer (15), and thrust washer (14).
NOTE:
A special locknut wrench is required for the removal of the bearing locknut. The Bearing Locknut Tool, Bearing
Cone Driver and Spindle/Shaft Drive Tool are included in the Service Kit, part number 100254-020.
10. Bolt the Spindle Drive Tool (Service Kit #100254-020) to the ring gear (20). Grade 8 bolts should be
used. Drive the spindle (3) from the hub by turning the center bolt of the Spindle Drive Tool. Care should
be taken to avoid damaging splines and threads on spindle.
NOTE:
Bearing cone (13) has been designed with a press fit with respect to spindle (3). Considerable force will be
required to remove the cone from the spindle.
11. Remove the Spindle Drive Tool from the ring gear (20).
12. Remove the eighteen bolts (9) and washers (10) from the hub (11) and remove the ring gear (20). It
may be necessary to strike the ring gear (20) with a rubber mallet to loosen it from the hub (11).
13. Remove the boot seal (4) and oil seal (5) and bearing cones (6 & 13) from the hub (11). Inspect the
bearing cups (7 & 12) in position and remove only if replacement is required.