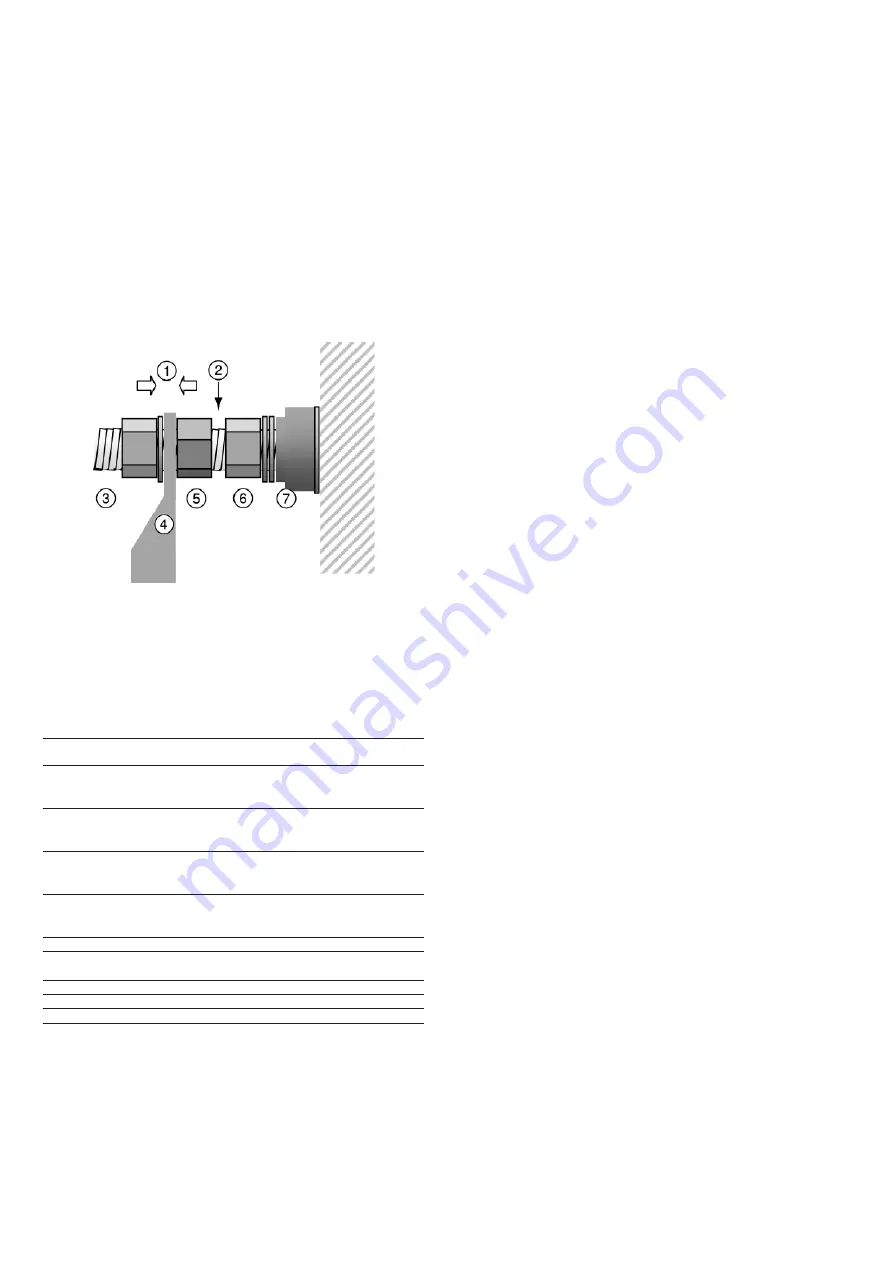
26
11.6 - Evaporator and condenser maintenance
Check that:
•
the insulating foam is intact and securely in place,
•
the sensors and flow switch are correctly operating
and correctly positioned in their support,
•
the water-side connections are clean and show no sign
of leakage.
11.7 - Compressor maintenance
11.7.1 - Oil filter change schedule
As system cleanliness is critical to reliable system operation,
there is a filter in the oil line at the oil separator outlet. The
oil filter is specified to provide a high level of filtration (5 µm)
required for long compressor life.
The filter should be checked after the first 500 hours of
operation, and every subsequent 2000 hours. The filter should
be replaced at any time when the pressure differential
across the filter exceeds 2 bar.
The pressure drop across the filter can be determined by
measuring the pressure at the discharge port (at the oil
separator) and the oil pressure port (at the compressor).
The difference in these two pressures will be the pressure
drop across the filter, check valve, and solenoid valve. The
pressure drop across the check valve and solenoid valve is
approximately 0.4 bar, which should be subtracted from the
two oil pressure measurements to give the oil filter pressure
drop.
11.7.2 - Compressor rotation control
Correct compressor rotation is one of the most critical appli-
cation considerations. Reverse rotation, even for a very
short duration, damages the compressor and can even
destroy it.
The reverse rotation protection scheme must be capable of
determining the direction of rotation and stopping the
compressor within one second. Reverse rotation is most
likely to occur whenever the wiring at the compressor
terminals has been modified.
To minimise the opportunity for reverse rotation, the follow-
ing procedure must be applied. Rewire the power cables to
the compressor terminals and/or the downstream variator
connection decks as originally wired.
For replacement of the compressor, a low pressure switch
is included with the compressor. This low pressure switch
should be temporarily installed as a hard safety on the high
pressure part of the compressor. The purpose of this switch
is to protect the compressor against any wiring errors at
the compressor terminal pin. The electrical contact of the
switch would be wired in series with the high pressure switch.
The switch will remain in place until the compressor has
been started and direction of rotation has been verified; at
this point, the switch will be removed.
11.4.2 - Connection precautions for the compressor power
terminals
These precautions must be applied during an intervention
that requires the removal of the power conductors connected
to the compressor supply terminals.
The tightening nut of terminal (6) supporting the isolator
(7) must never be loosened, as ist ensures terminal tightness
and compressor leak tightness.
The tightening of phase lug (4) must apply the torque
between counter nut (5) and tightening nut (3): during this
operation a counter-torque must be applied at counter nut
(5). Counter-nut (5) must not be in contact with the tightening
nut of terminal (6).
1. Torque application to tighten the lug
2. Avoid contact between the two nuts
3. Lug tightening nut
4. Flat lug
5. Counter-nut
6. Terminal tightening nut
7. Isolator
11.5 - Tightening torques for the main bolts and screws
Screw type
Used for
Torque
value,
N
·
m
M20 nut
Chassis
190
M20 nut
Heat exchanger side-side connection
240
M16 nut
Compressor fixing
190
H M16 screw
Heat exchanger water boxes, structure
190
H M16 screw
Compressor suction flanges
190
H M20 screw
Compressor suction flanges TU & TV
240
M16 nut
Compressor discharge line TU
190
M20 nut
Compressor discharge line TV
240
H M8 screw
Drier cover
35
1/8 NPT connection Oil line
12
TE nut
Compressor oil line
24,5
7/8 ORFS nut
Oil line
130
5/8 ORFS nut
Oil line
65
3/8 ORFS nut
Oil line
26
H M6 screw
Stauff collar
10
Taptite screw M6
Oil line collar
7
Metric screw M6
Plate fixing, control box, terminal box
7
Taptite screw M10
Oil filter, control box fixing
30
ATTENTION: The tightening of the connections at the
compressor terminals requires special precautions. Please
refer to the chapter above.