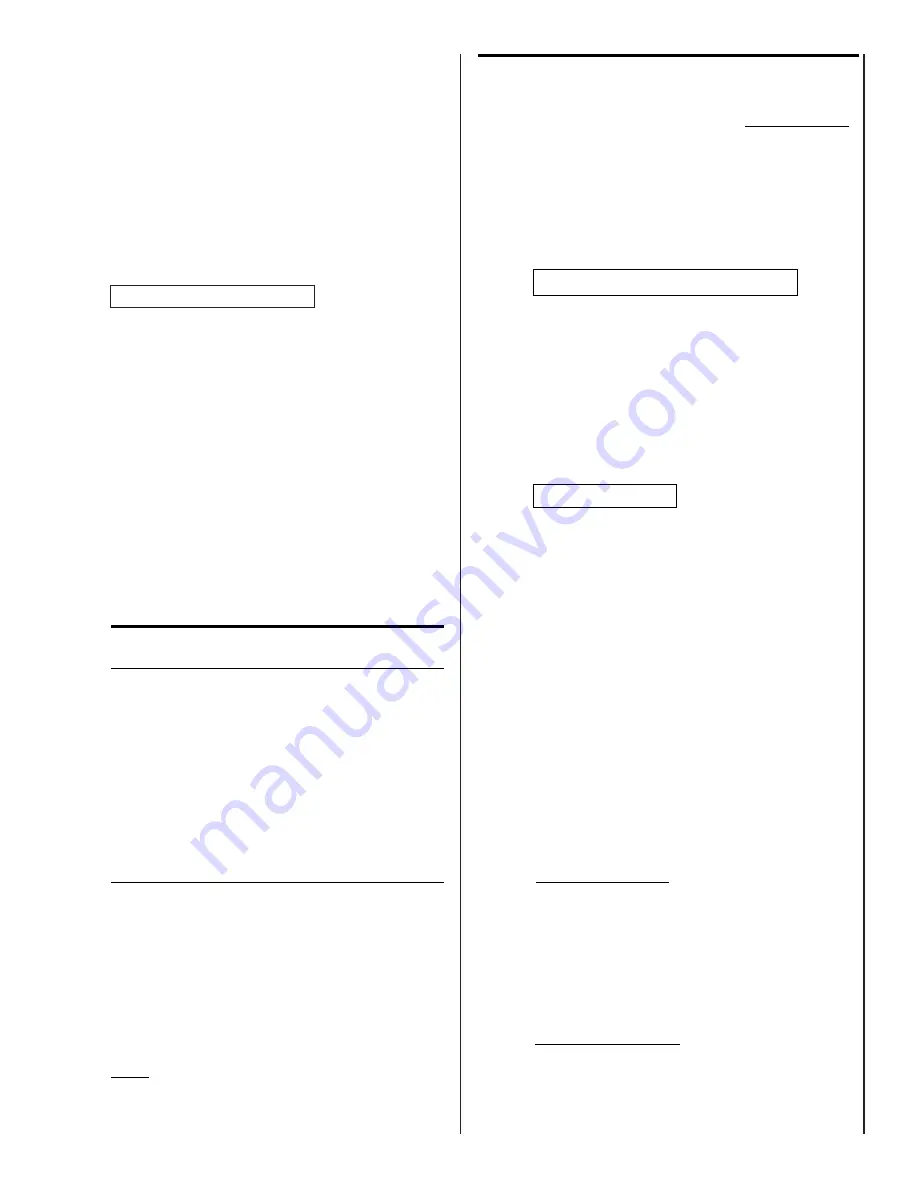
Tools Needed
Screwdriver
Components available for replacement are the
thermal assembly and the switches (per
Figures 3 and 4). Replace as follows:
Thermal Assembly Replacement
(1) Thermal assemblies are pre-calibrated at
the factory and can be easily interchanged with
the old one. Instructions are included with
each replacement assembly. See “In-Process
Adjustments” above for zero adjustment.
(2) Should the thermal assembly be moved for
any reason, it should be repositioned so that
the edge of its flange corresponds with the line
scribed on the instrument case.
Enclosed Types
(Except Explosion-Proof Types)
The leadwire configuration, though rather slack
from the switch bank assembly to the wire
clamp, is necessary for proper controller opera-
tion. This configuration should be duplicated
when replacing the switch.
(1) Turn the adjustment knob to the upper
range limit. This will permit access to all three
scale mounting screws.
(2) Remove the scale and unscrew the screw
holding pivot post mounting bracket. Be sure to
save the two spacers under the bracket. (Dual
switch types only.)
(3) Remove the tension spring from switch
bank assembly.
(4) The switch bank assembly can now be
removed from the pivot post.
Dual Switch Types
(a) Disassemble switch #1 extension spring.
This will permit access to whichever switch
needs replacement.
(b) Insert new switches and leadwires on
switch bank assemblies.
(c) Re-assemble switch #1 extension spring
and re-install entire assembly onto pivot post.
Single Switch Types
(a) Remove the cover from the switch.
(b) Insert new switch and leadwires back into
switch cover.
(c) Re-assemble switch assembly to pivot post.
Part III - Replacements
The set point of switch #1 is determined by the
red Adjustment Pointer. The set point of switch #2
may be adjusted by up to 25% of the range span
below the switch #1 set point by turning adjust-
ment “D” in (clockwise). See Figure 4. The set
point of switch #2 should not be above that of
switch #1.
To align switch #1 to the Adjustment Pointer,
loosen adjustment “A” and set the Adjustment
Pointer to the scale, then re-tighten adjustment
“A”.
Correction of Capillary
If the length of capillary immersed in the process
differs from the amount immersed at the factory
calibration bath, a calibration shift will occur. The
error may be corrected as follows:
Move set pointer to the highest temperature
setting. Note indicating scale reading with the
head and sensor at room temperature. Loosen
the two thermal assembly mounting screws. Re-
position the housing index against the calibration
on the instrument case (or skeleton casting) at a
rate of 1 division line per capillary length listed in
the following column. Move to the left if capillary is
to be added to the process, or to the right if capil-
lary is to be removed from process.
Model
Cap Length/
Number
Range
Division*
1
-180 to 120˚F
2 ft.
2
-125 to 350˚F
1 1/2 ft.
3
-125 to 500˚F
1 ft.
4
-40 to 120˚F
4 ft.
5
-40 to 180˚F
3 ft.
6
0 to 250˚F
2 1/2 ft.
7
0 to 400˚F
2 ft.
8
50 to 650˚F
2 ft.
M9
50 to 1000˚F
2 1/2 ft.
* Added to or taken away from the process.
Tighten the two thermal assembly mounting
screws. Note change indicated scale reading (if
any).
Turn zero adjustment “C” to bring indicating point-
er reading back to the original reading noted
before. Turning in lowers indicated reading.
Note: The thermal assembly can be returned to
its original position by aligning its flange with
the line scribed on the instrument case.
Содержание 800
Страница 7: ...Dimensions 800 Series 820E 822E ...