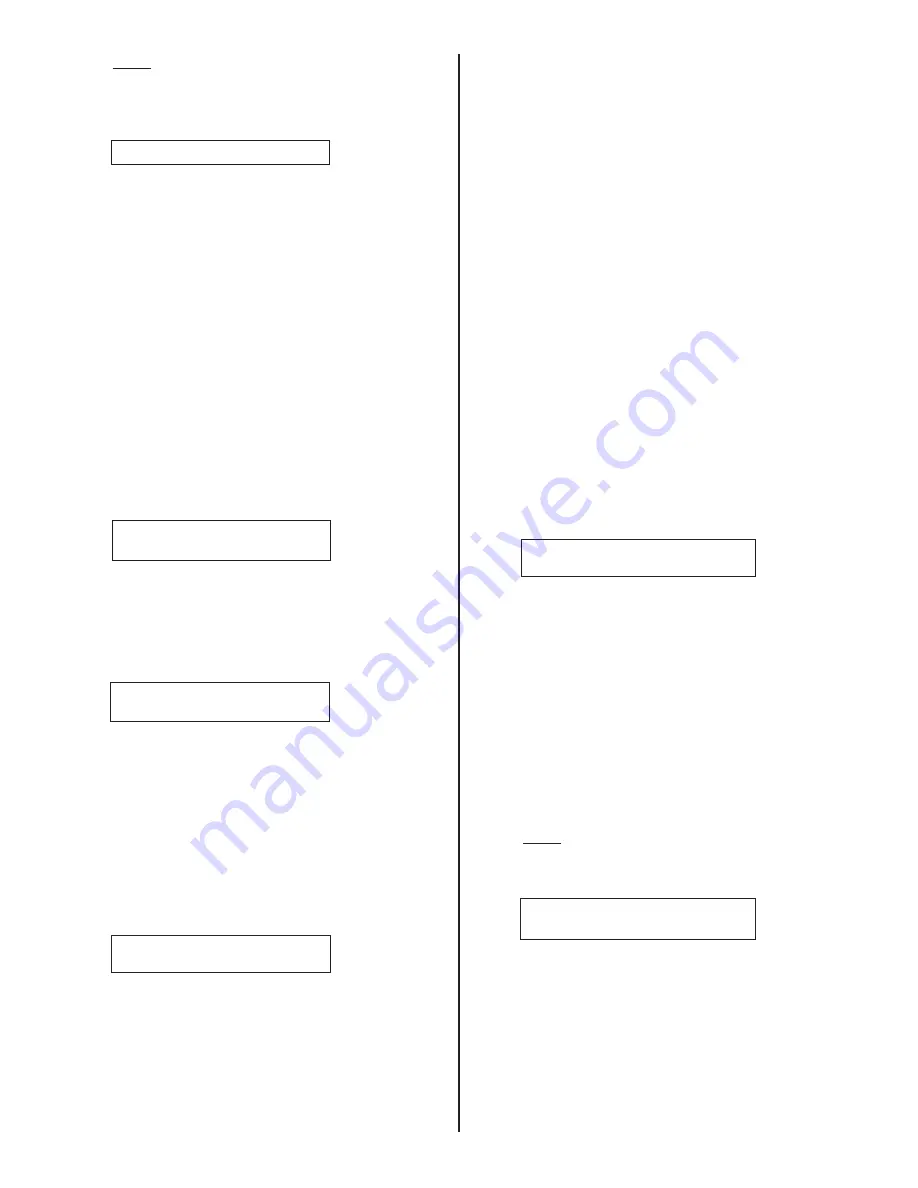
ered in order to accomplish the adjustment.
To adjust the set point of switch #1 above that of
switch #2 turn the red pointer down scale until it
agrees with the brown Indicating Pointer. Both
pointers must be below the upper scale limit by
an amount greater than the desired difference
between the switch settings. The foregoing step
enables the actuating lever to be moved by a
finger or tool simulating thermal assembly move-
ment. Connect test lights to indicate switch
operation or listen for the individual switch clicks.
The set point of switch #1 may be adjusted by up
to 50% of the range span above or below the
switch #2 set point. Turn adjustment “B” clock-
wise to raise or counter-clockwise to lower the
#1 switch set point. The set point of switch #2
will remain aligned to the red Adjustment Pointer.
Check the results of the adjustments made by
manipulating the actuating lever.
If it is necessary to align switch #2 to the red
adjustment pointer loosen adjustment “A”, set
the adjustment pointer as required and tighten
adjustment “A”.
Adjusting Dual Switch
Types 802 and 802S
Connect test lights to indicate switch operation or
listen for the individual switch clicks. The separa-
tion between switches is the difference between
the high and low set points. The set points are
determined by setting individual adjustment
pointers and may be separated up to 100% of
scale range apart.
To align either switch to the Adjustment
Pointer the corresponding adjustment “A” must be
loosened and the Adjustment Pointer set to the
Indicating Pointer, then tighten adjustment “A”.
Note: Switch #1, green pointer, cannot be set to
operate at a higher setting than switch #2, red
pointer.
Adjusting Dual Switch
Explosion-Proof Types 822E
Remove the explosion-proof die-cast cover to
permit access to the switches. Move the
Adjustment Pointer up scale beyond the
Indicating Pointer by an amount greater than the
difference between the switch settings by moving
the actuating lever upward with a finger or a tool
simulating thermal assembly movement.
Connect test lights to indicate switch operation or
listen for the individual switch clicks.
Note: The adjustment knob slides off adjustment
shaft for all controls except the 802. The 802
requires a 5/64” allen wrench. Be sure to replace
gasket when re-assembling.
In-Process Adjustments
Use an accurate test thermometer such as a
thermocouple with its probe mounted directly to
the center of the sensing bulb. Before making any
adjustments, allow process temperature to
stabilize; i.e., successive on-off cycles repeated.
Correct any difference between the Indicating
Pointer and the test thermometer by holding the
compensator with a 5/16” wrench while turning
the zero adjustment “C” on the thermal assembly
with a second 5/16” wrench, per Figure 3 until the
brown Indicating Pointer reads the same as the
test thermometer. Turning clockwise lowers indi-
cated reading. Compare the process temperature
with the set point Adjustment Pointer. Loosen
adjustment screw “A” to align set point
Adjustment Pointer with the Indicating Pointer.
Re-tighten screw “A”.
Adjusting Thermometer
Types T800 and T800S
Use the in-process adjustment to check the
control. Differences between the test instrument
and the thermometer can be corrected by turning
the zero adjustment “C” per Figure 3 on the ther-
mal assembly. Turning in lowers indicated reading.
Adjusting Single Switch
Types 800, 800S and 820E
Move the set point Adjustment Pointer up scale
beyond the brown Indicating Pointer. This
permits checking the set point by moving the
lever arm upward with a finger or tool simulating
thermal assembly movement. Connect test lights
to indicate switch operation or listen for the switch
to click. Loosen adjustment “A” and move the
Adjustment Pointer until it agrees with the
Indicating Pointer. When the switch clicks
re-tighten the screw.
Adjusting Dual Switch
Types 802P and 802PS
If it is desired to adjust the set point of switch #1
below that of switch #2 turn the red pointer up
scale beyond the black Indicating Pointer by an
amount greater than the desired difference
between the switch settings. If it is not possible to
do this because the black Indicating Pointer is
registering too high a temperature, the thermal
assembly sensing bulb temperature must be low-
Содержание 800
Страница 7: ...Dimensions 800 Series 820E 822E ...