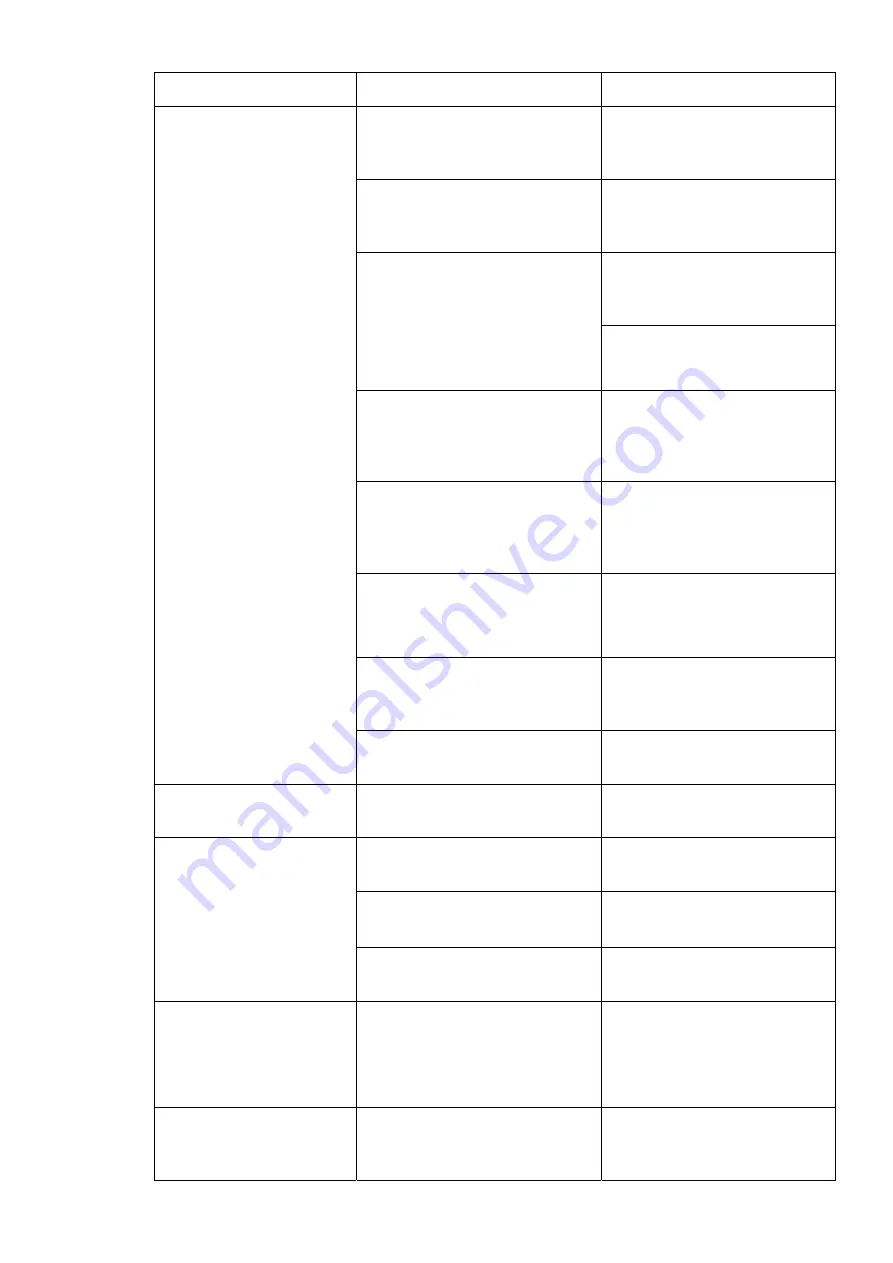
23
5. Troubleshooting
Status
Cause
Troubleshooting
Ultimate pressure is low
or unstable, or
evacuation performance
is low.
The ambient temperature at
the installation site is high.
Decrease the ambient
temperature to 25°C by
cooling.
Operation time is too long after
installation or long termination.
Operate 24 hours to 48
hours, and then perform
checking.
Leakage is detected.
Check components that were
maintained before ultimate
pressure changes.
Clean glass bell jar and
O-ring, or replace
consumables.
Deterioration of the oil for the
oil diffusion pump.
If the cause of the
deterioration is clear
(incorrect air intake, leakage,
etc.), replace the oil.
The temperature o the water is
too high.
The amount if the water is not
sufficient.
Adjust it to 20°C to 25°C.
Adjust it to 2 L/min.
Material (substrate) that
involves large-amount gas
release was used (e.g., resin
substrate).
Change the material.
Take longer evacuation time.
Failure in the oil sealed
vacuum pump
Refer to the Oil Sealed
Vacuum Pump User’s
Manual.
Failure in measuring
instrument
Refer to the user’s manual of
each instrument.
The oil diffusion pump
stays cold.
The heater is disconnected.
Replace the heater.
No current flows through
the electrode even when
the evaporation power
supply is operated.
Evaporation power supply is
disconnected.
Replace the evaporation
power supply.
The electrode may be shorted
in the feed-through collar.
Repair the point of short to
recover isolation.
Failure in evaporation power
supply
Refer to the Evaporation
Power Supply User’s Manual.
Pressure measured on the
roughing side indicates
wrong values when the
vacuum chamber is
exposed to open air.
The main valve is not opened
completely.
Clean the internal face of the
seal on the main valve.
The thermal protector for
oil sealed vacuum pump
operates.
Overloaded
Refer to the Oil Sealed
Vacuum Pump User’s
Manual.