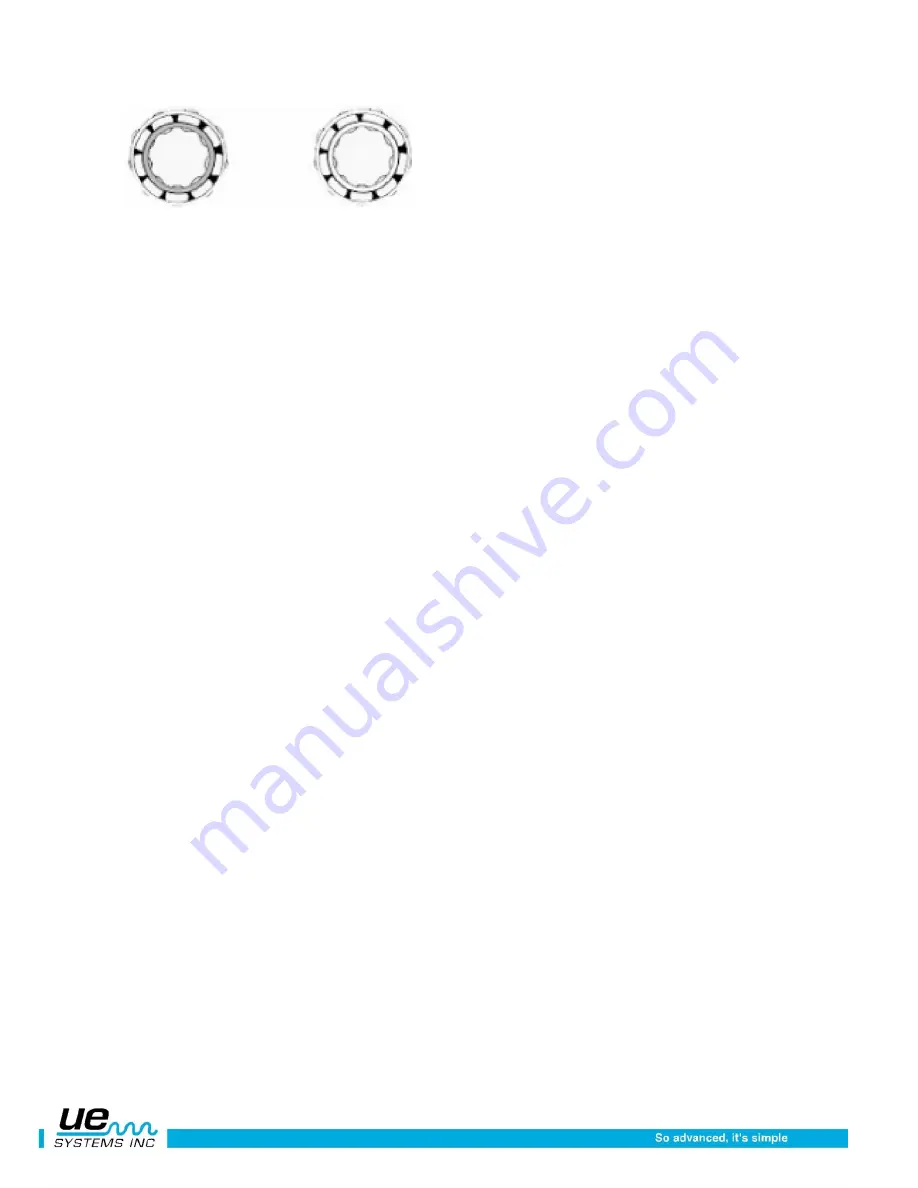
Version 1
21
Proper Lubrication
Lack of Lubrication Increases
Reduces Friction
amplitude levels
General Mechanical Trouble Shooting
As operating equipment begins to fall due to component wear, breakage or misalignment , sonic and more
importantly, ultrasonic shifts occur. The accompanying sound pattern changes can save time and guess
work in diagnosing problems if they are adequately monitored. Therefore, an ultrasonic history of key
components can prevent unplanned down-time. And just as important, if equipment should begin to fail in
the field, the ULTRAPROBE can be extremely useful in trouble shooting problems
.
Trouble Shooting
1. Use the contact (stethoscope) module.
2. Touch test area(s): listen through headphones and observe the meter.
3. Adjust sensitivity until mechanical operation of the equipment is heard clearly and the meter can
fluctuate
4. Probe equipment by touching various suspect areas.
5. To focus in on problem sounds, while probing, reduce sensitivity gradually to assist in locating the
problem sound at its' loudest point. (This procedure is similar to the method outlined in LEAK
LOCATION, i.e., follow the sound to its loudest point.)
Monitoring Operating Equipment
In order to understand and keep ahead of potential problems in operating equipment, it is necessary to
establish base data and observe shifts in that data. The data can be compiled from meter readings, chart
recordings and even tape recordings (for chart recording it will be necessary to have your Ultraprobe
converted at the factory).
Procedure:
1. Select key locations to be monitored and make permanent reference marks for future testing by
either marking with a center-punch or with paint or epoxy bond a washer to note the spot.
2. Follow steps 1-5 as outlined above in the Trouble Shooting section.
3. On a chart note:
a. Equipment
b. Location
c. Date
d. Meter Mode (LIN / LOG)
e. Frequency
f. Sensitivity level
g. Meter reading
NOTE:
In diagnosing any type of mechanical equipment, it is important to understand how that equipment
operates. Being able to interpret sonic changes is dependent on a basic understanding of the operations of
the particular equipment being tested. As an example, in some reciprocal compressors, the diagnosis of a
valve problem in the inlet manifold is dependent on recognizing the distinctive clicking sound of a good
valve vs. the muffled click of a valve in a "blow-by" mode.