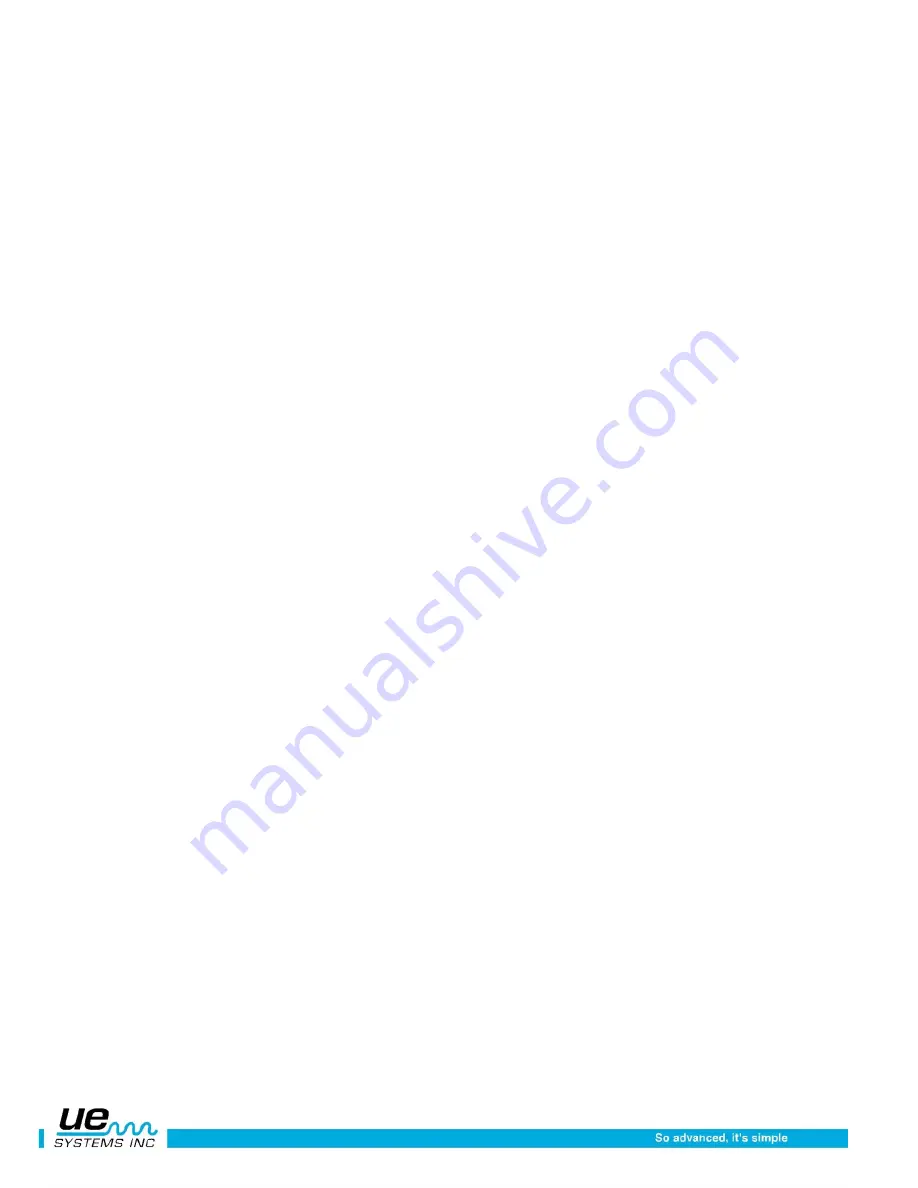
Version 1
26
Leakage Behind Walls
1. Look for water or steam markings such as discoloration, spots in wall or ceiling, etc.
2. If steam, feel for warm spots in wall or ceiling.
3. Test area using steps 1-3 as outlined on page 26, section "A", "Procedure".
4. Listen for leak sounds. The louder the signal the closer you are to the leak site.
Blockage in Pipes
If total blockage occurs in piping, there will be no sound since there will be no flow at the blocked site.
Procedure
1. Use steps 1-2 as outlined in VALVE TESTING.
2. Use 40 kHz or Fixed Band
3. Use the Tone Test method:
a. Make sure the downstream side of the pipe is clear of fluids.
b. Place a Tone Generator in the downstream side facing upstream.
c. At set intervals, touch along pipe with contact probe and listen for a drop off of the ultrasonic
signal from the Tone Generator.
Partial Blockage
When partial blockage exists, a condition similar to that of a by-passing valve is produced. The partial
blockage will generate ultrasonic signals (often produced by turbulence just downstream). If a partial
blockage is suspected, a section of piping should
be inspected at various intervals. The ultrasound
generated within the piping will be greatest at the site of the partial blockage
Procedure:
1. Use procedures 1-3 as outlined in VALVE TESTING.
2. Listen for an increase in ultrasound created by the turbulence of partial blockage.
Flow Direction
Flow in piping increases in intensity as it passes through a restriction or a bend in the piping. As flow travels
upstream, there is an increase in turbulence and therefore the intensity of the ultrasonic element of that
turbulence
at the flow restriction. In testing flow direction, the ultrasonic levels will have greater intensity in
the DOWNSTREAM side than in the UPSTREAM side.
Procedure
1. Use stethoscope mode.
2. Select LOG in Meter Selection Dial.
3. Start test in FIXED BAND mode. If it is difficult hearing the flow signal, adjust Frequency Selection
Dial to 40 kHz or to 25 kHz for higher viscosity fluids.
4. Begin test at 10 (maximum) sensitivity level.
5. Locate a bend in the pipe system (preferably 60, or more).
6. Touch one side of bend and note meter level.
7. Touch other side of bend and note meter level.
8. The side with the higher (louder) reading should be the downstream side.
NOTE:
Should it be difficult to observe a sound differential, reduce sensitivity and test as described until a sonic
difference is recognized
.